-
oa The Beginnings of Chemical Engineering
THE DESIGN OF PLATINUM BOILERS FOR SULPHURIC ACID CONCENTRATION
- Source: Platinum Metals Review, Volume 1, Issue 2, Apr 1957, p. 51 - 54
-
- 01 Jan 1957
Preview this article:
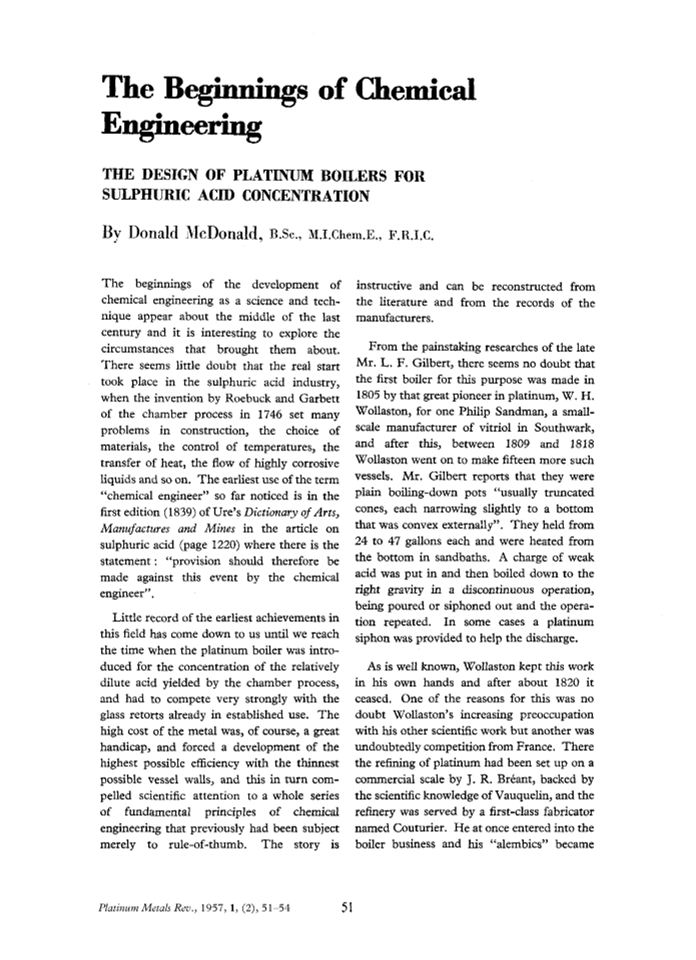



The Beginnings of Chemical Engineering, Page 1 of 1
< Previous page Next page > /docserver/preview/fulltext/pmr/1/2/pmr0001-0051-1.gif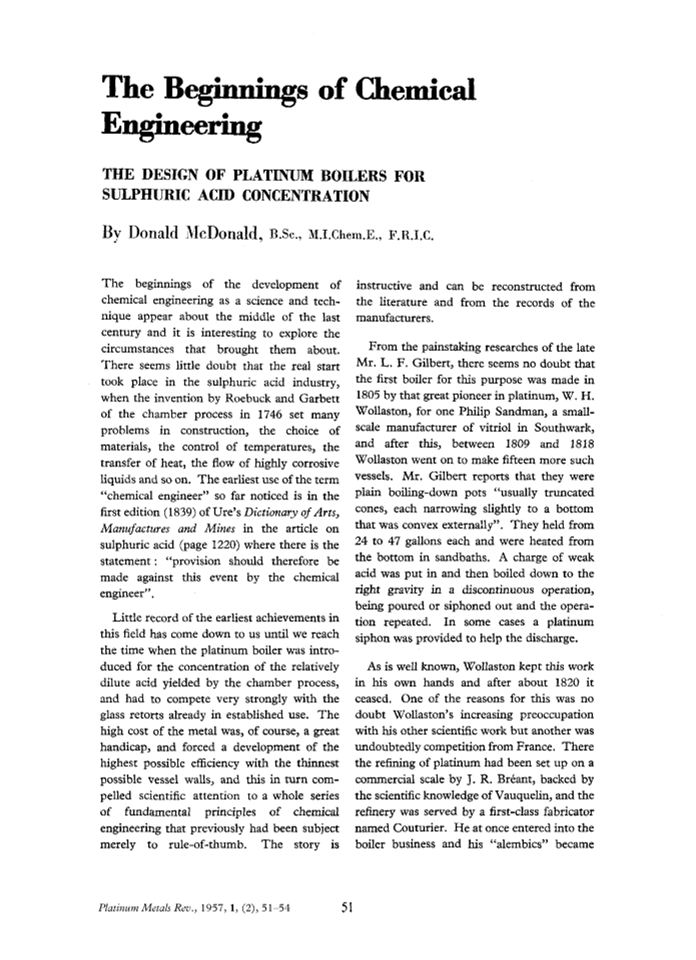
There is no abstract available.
© Johnson Matthey