-
oa Fifty Years of Research on the Platinum Metals
- Source: Platinum Metals Review, Volume 12, Issue 1, Jan 1968, p. 22 - 28
-
- 01 Jan 1968
Preview this article:
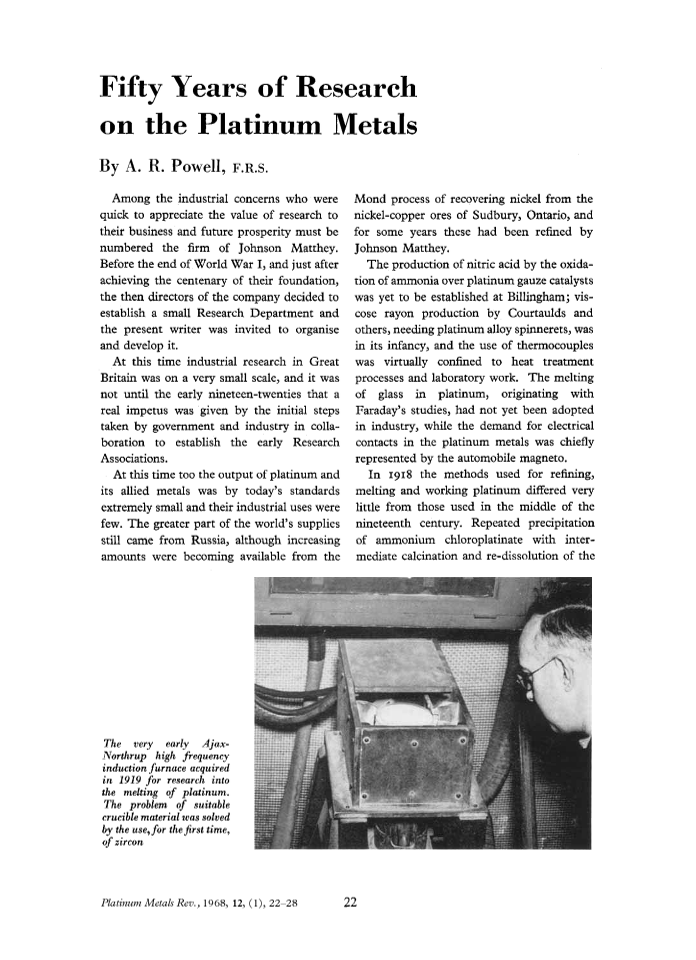



Fifty Years of Research on the Platinum Metals, Page 1 of 1
< Previous page Next page > /docserver/preview/fulltext/pmr/12/1/pmr0012-0022-1.gif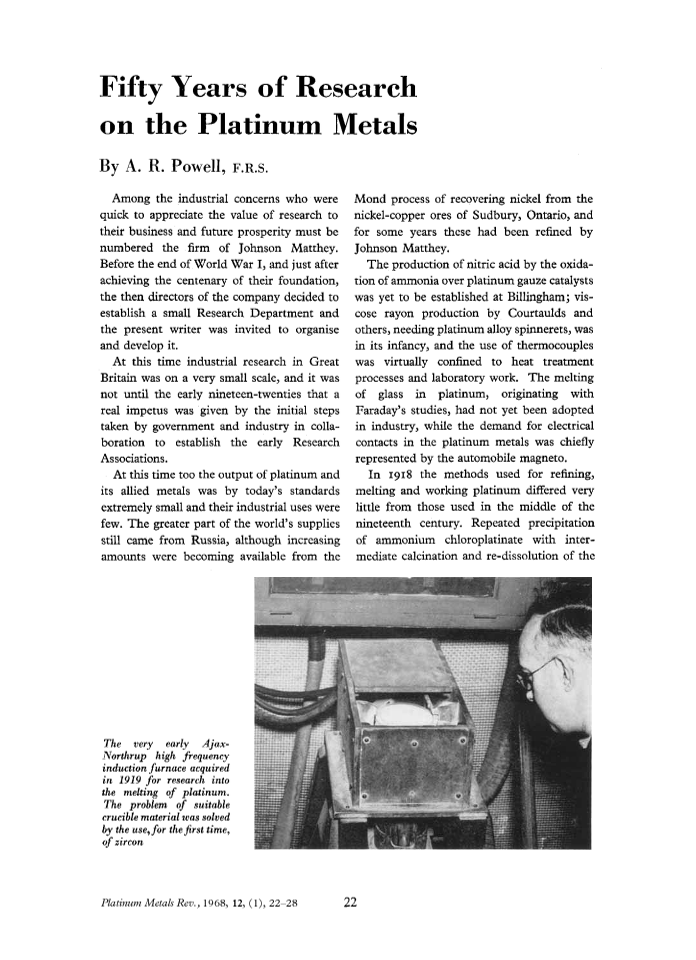
There is no abstract available.
© Johnson Matthey