-
oa A New Platinum-Wired Air Flow Meter
Fuel Economy of Petrol Injection Engines Improved
- Source: Platinum Metals Review, Volume 26, Issue 3, Jul 1982, p. 117 - 117
-
- 01 Jan 1982
Preview this article:
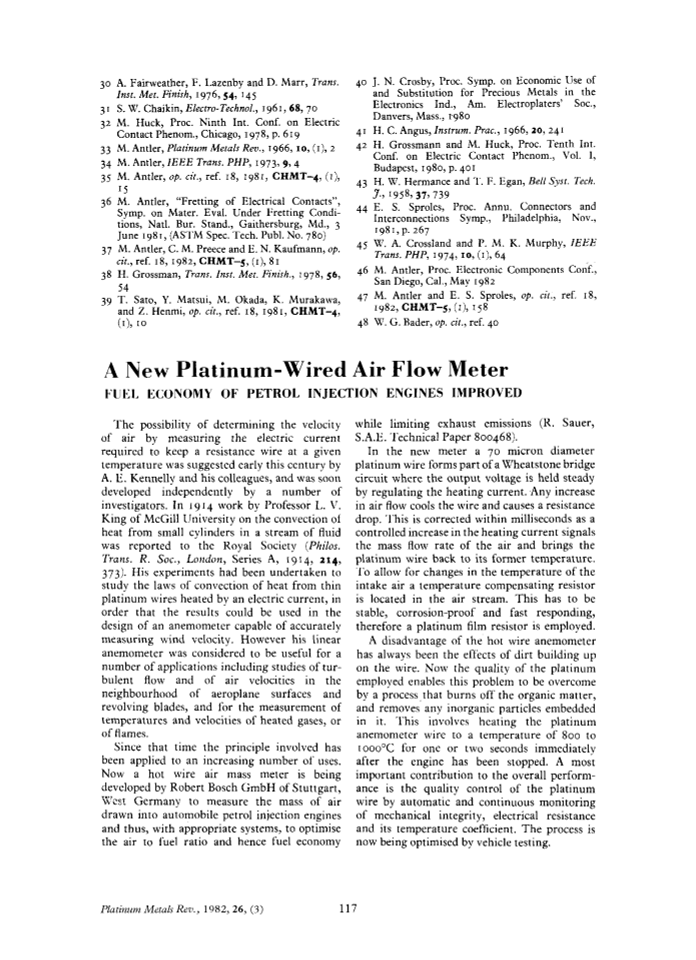



A New Platinum-Wired Air Flow Meter, Page 1 of 1
< Previous page Next page > /docserver/preview/fulltext/pmr/26/3/pmr0026-0117-1.gif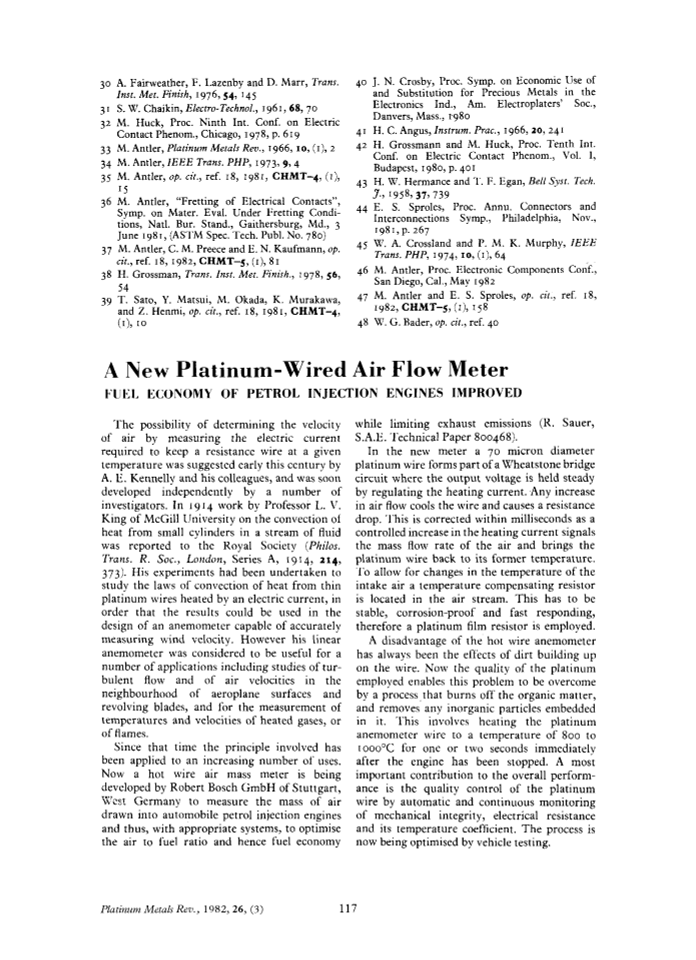
There is no abstract available.
© Johnson Matthey