-
oa Palladium-Nickel as a Gold Substitute
An Evaluation for Electronic Connectors
- Source: Platinum Metals Review, Volume 28, Issue 2, Apr 1984, p. 54 - 55
-
- 01 Jan 1984
Preview this article:
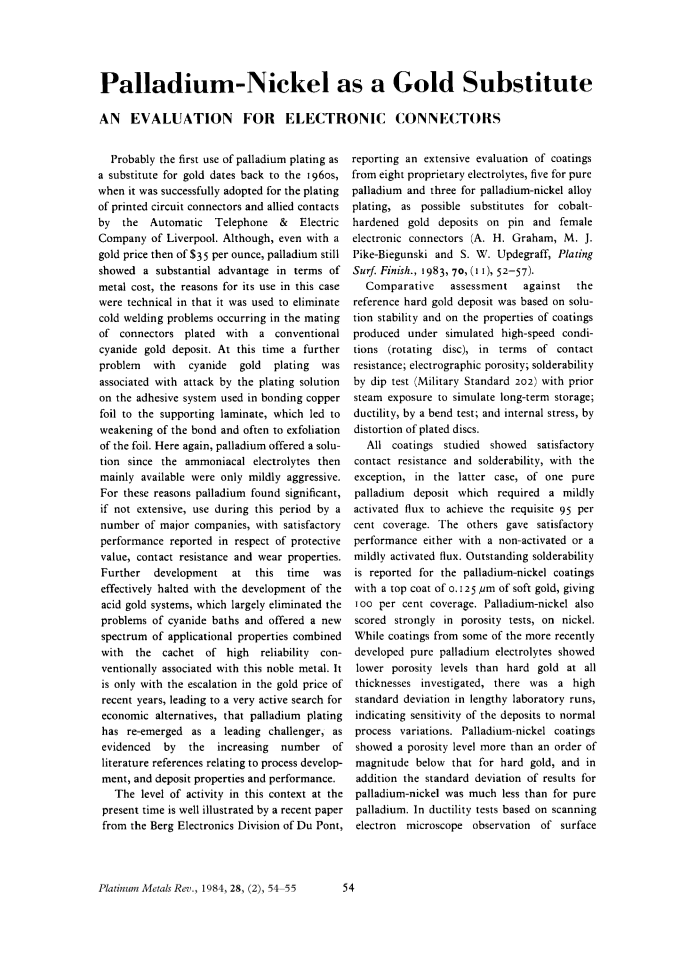



Palladium-Nickel as a Gold Substitute, Page 1 of 1
< Previous page Next page > /docserver/preview/fulltext/pmr/28/2/pmr0028-0054-1.gif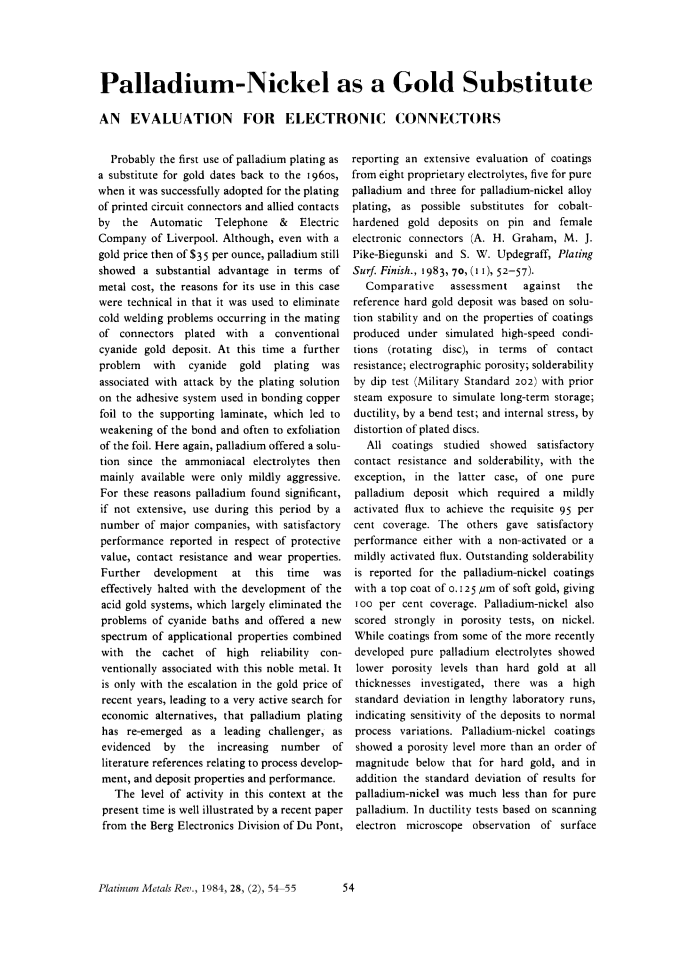
There is no abstract available.
© Johnson Matthey