-
oa Combustion in Wood-Burning Stoves
Platinum Catalyst Increases Thermal Efficiency and Greatly Reduces Pollution
- Source: Platinum Metals Review, Volume 28, Issue 3, Jul 1984, p. 115 - 116
-
- 01 Jan 1984
Preview this article:
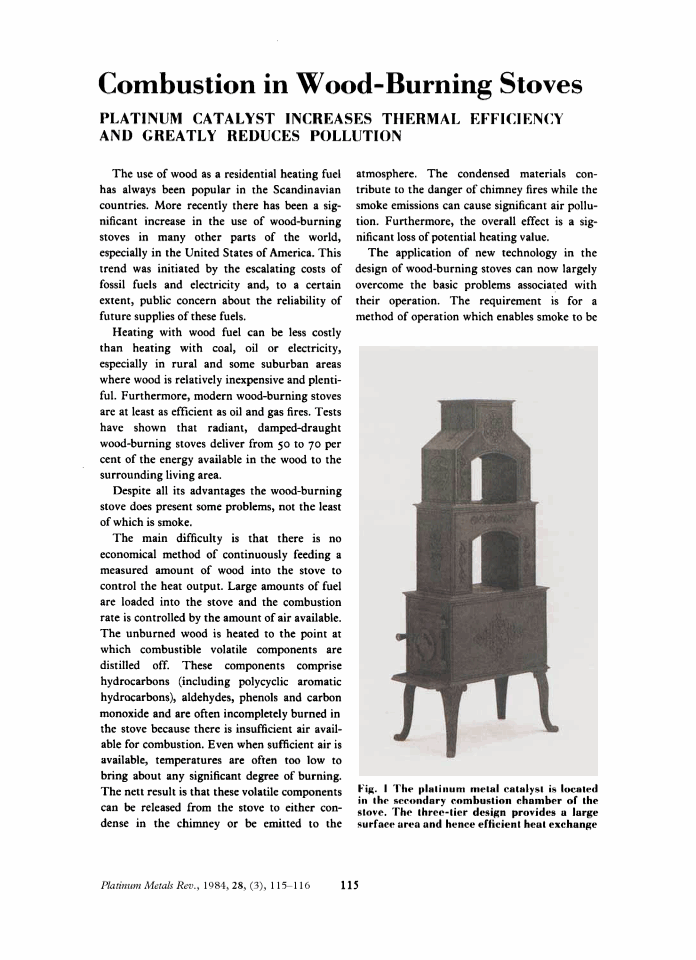



Combustion in Wood-Burning Stoves, Page 1 of 1
< Previous page Next page > /docserver/preview/fulltext/pmr/28/3/pmr0028-0115-1.gif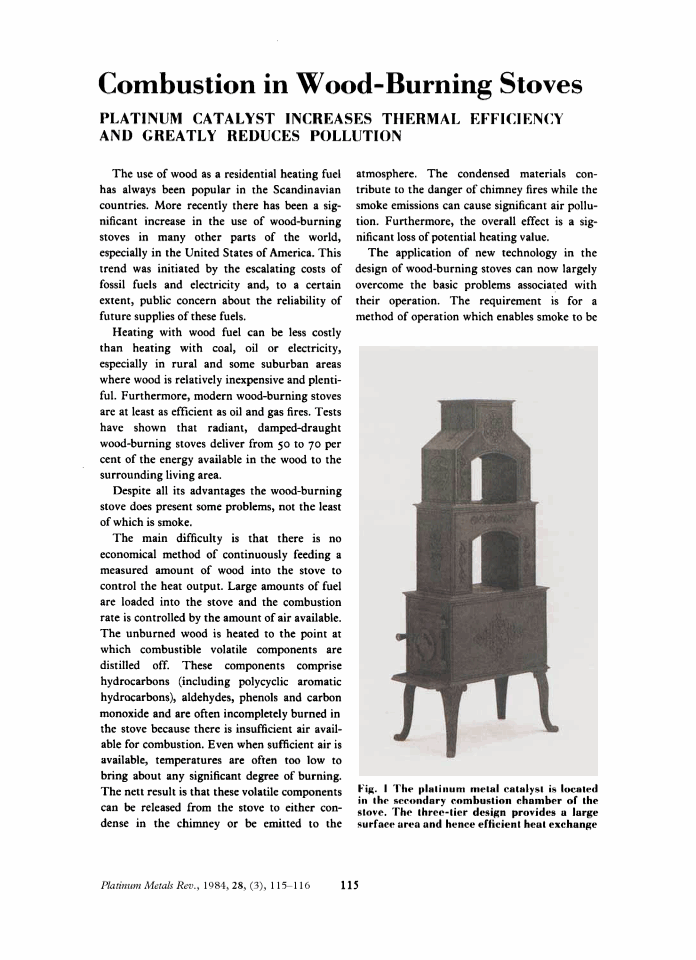
There is no abstract available.
© Johnson Matthey