-
oa Improved Iridium Alloy Welds
Four-Pole Oscillation Reduces Hot-Short Cracking
- Source: Platinum Metals Review, Volume 29, Issue 1, Jan 1985, p. 11 - 11
-
- 01 Jan 1985
Preview this article:
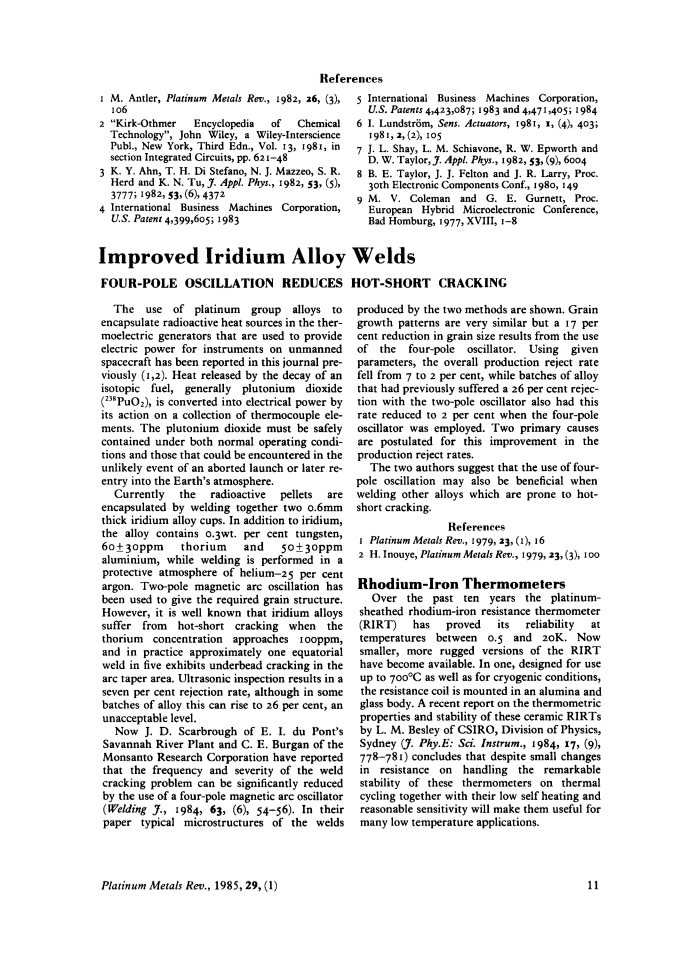



Improved Iridium Alloy Welds, Page 1 of 1
< Previous page Next page > /docserver/preview/fulltext/pmr/29/1/pmr0029-0011a-1.gif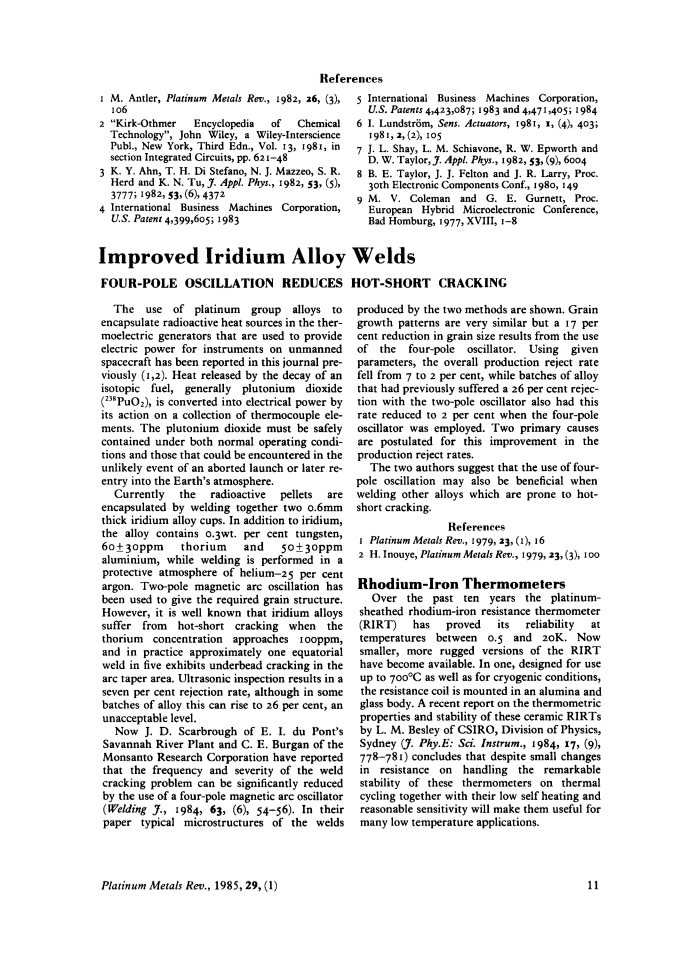
There is no abstract available.
© Johnson Matthey