-
oa A Positive Move Towards Low Lead Petrol
New Platformer Plant for Shell U.K. Limited
- Source: Platinum Metals Review, Volume 29, Issue 1, Jan 1985, p. 27 - 27
-
- 01 Jan 1985
Preview this article:
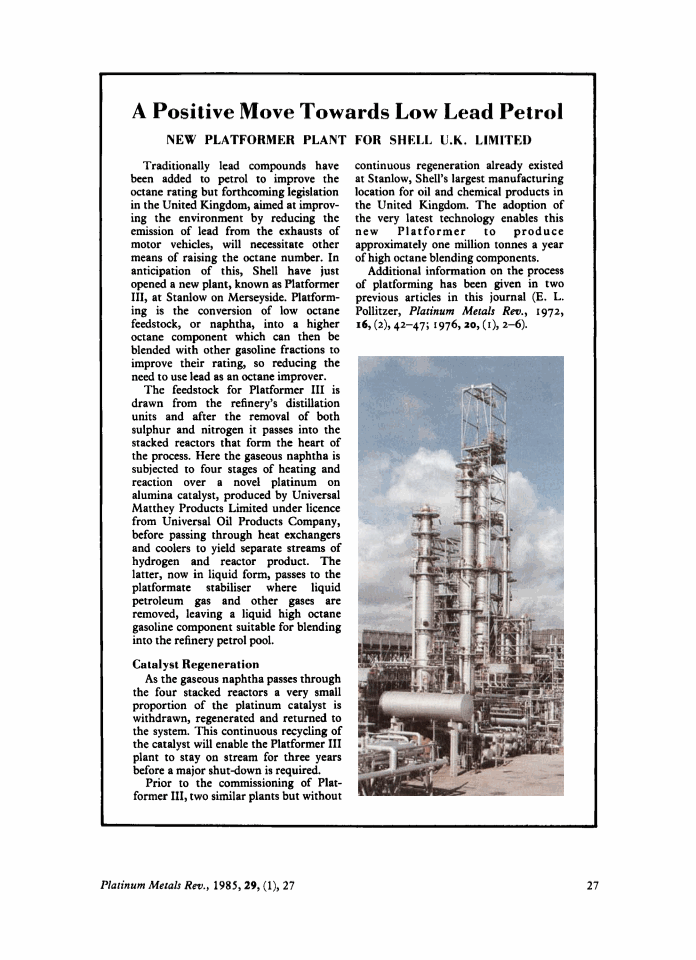



A Positive Move Towards Low Lead Petrol, Page 1 of 1
< Previous page Next page > /docserver/preview/fulltext/pmr/29/1/pmr0029-0027-1.gif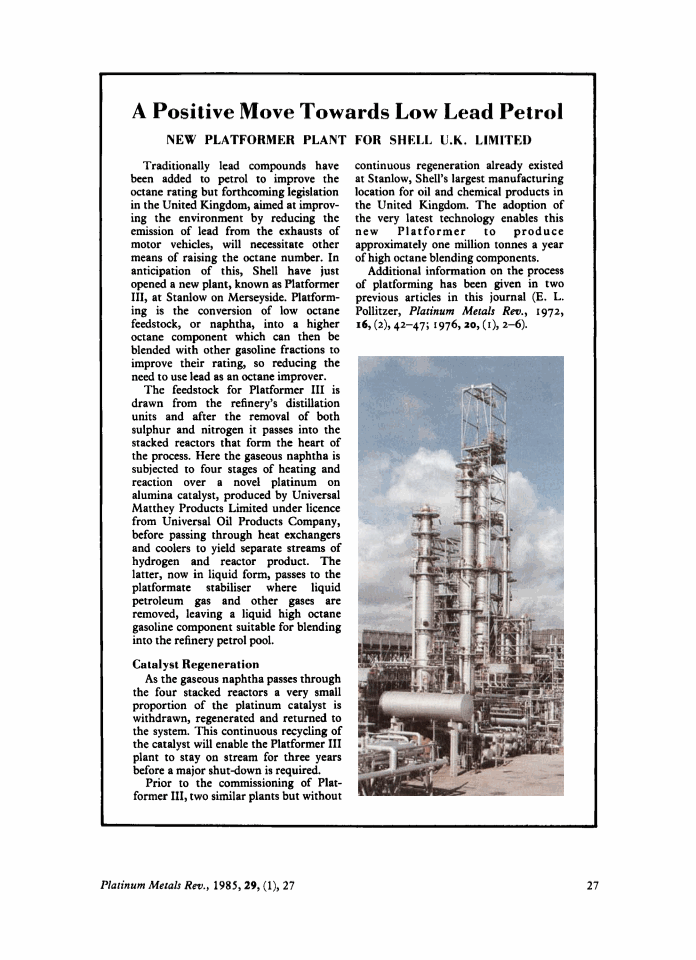
There is no abstract available.
© Johnson Matthey