-
oa Space Station Auxiliary Propulsion Jets
- Source: Platinum Metals Review, Volume 29, Issue 4, Oct 1985, p. 167 - 167
-
- 01 Jan 1985
Preview this article:
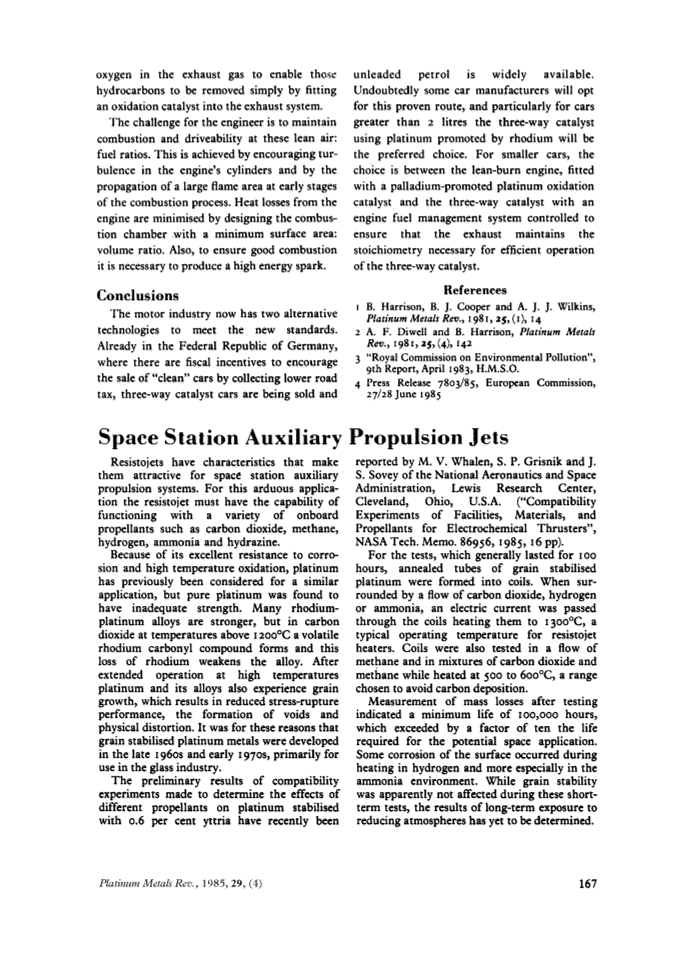



Space Station Auxiliary Propulsion Jets, Page 1 of 1
< Previous page Next page > /docserver/preview/fulltext/pmr/29/4/pmr0029-0167-1.gif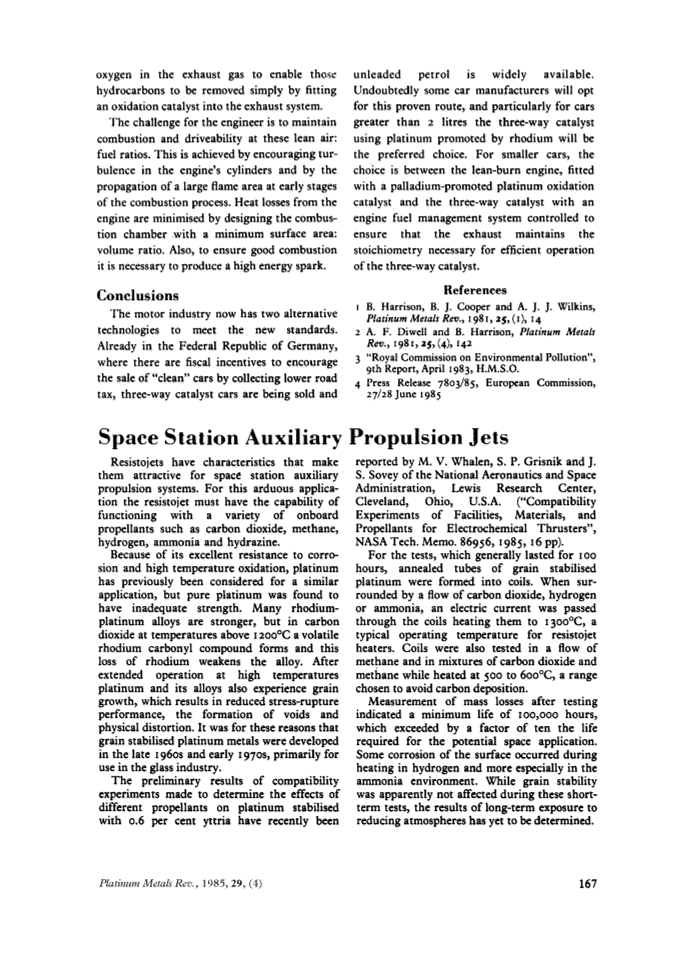
There is no abstract available.
© Johnson Matthey