-
oa Gamma Radiography with Iridium192
Advantages In The Non-Destructive Testing Of Castings And Welded Structures
- Source: Platinum Metals Review, Volume 3, Issue 1, Jan 1959, p. 12 - 16
-
- 01 Jan 1959
Preview this article:
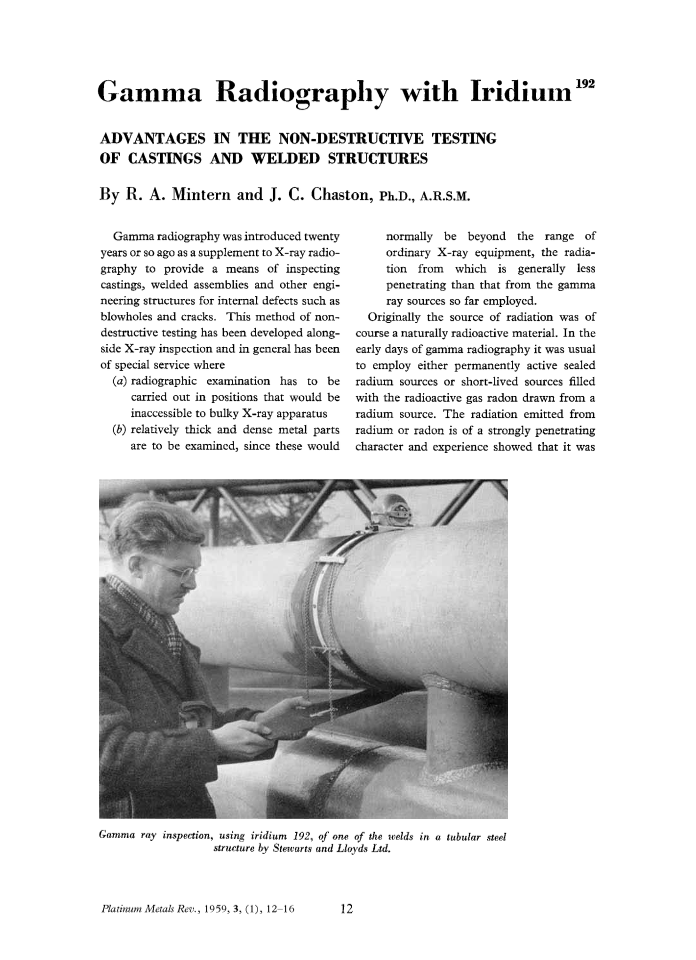



Gamma Radiography with Iridium192, Page 1 of 1
< Previous page Next page > /docserver/preview/fulltext/pmr/3/1/pmr0003-0012-1.gif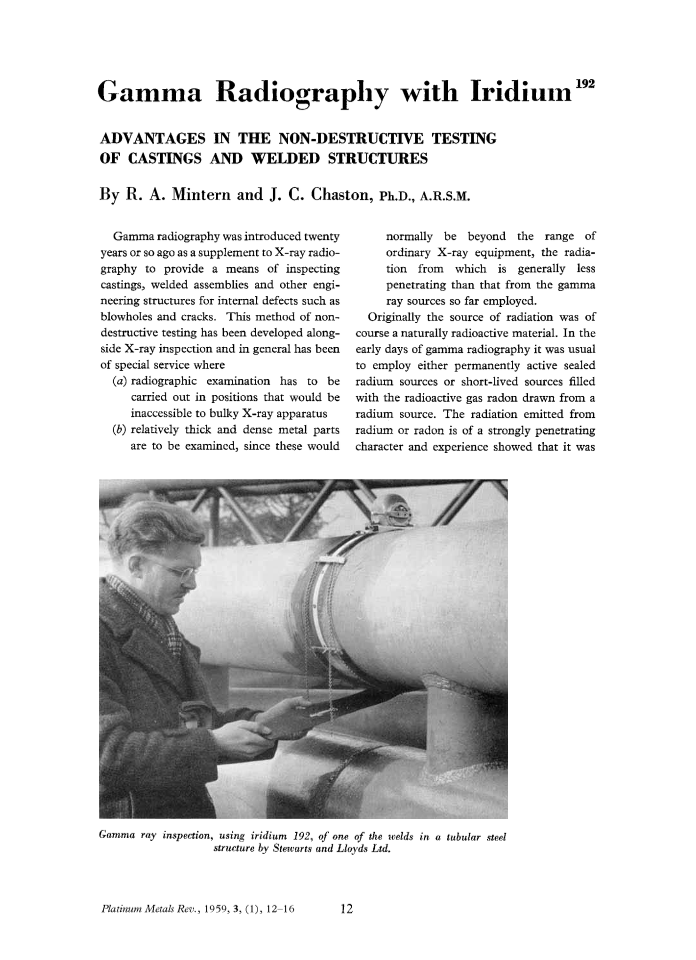
There is no abstract available.
© Johnson Matthey