-
oa Organic Deposits on Noble Metal Contacts
An Investigation Into Contact Contamination in Telephone Relays
- Source: Platinum Metals Review, Volume 3, Issue 1, Jan 1959, p. 19 - 21
-
- 01 Jan 1959
Preview this article:
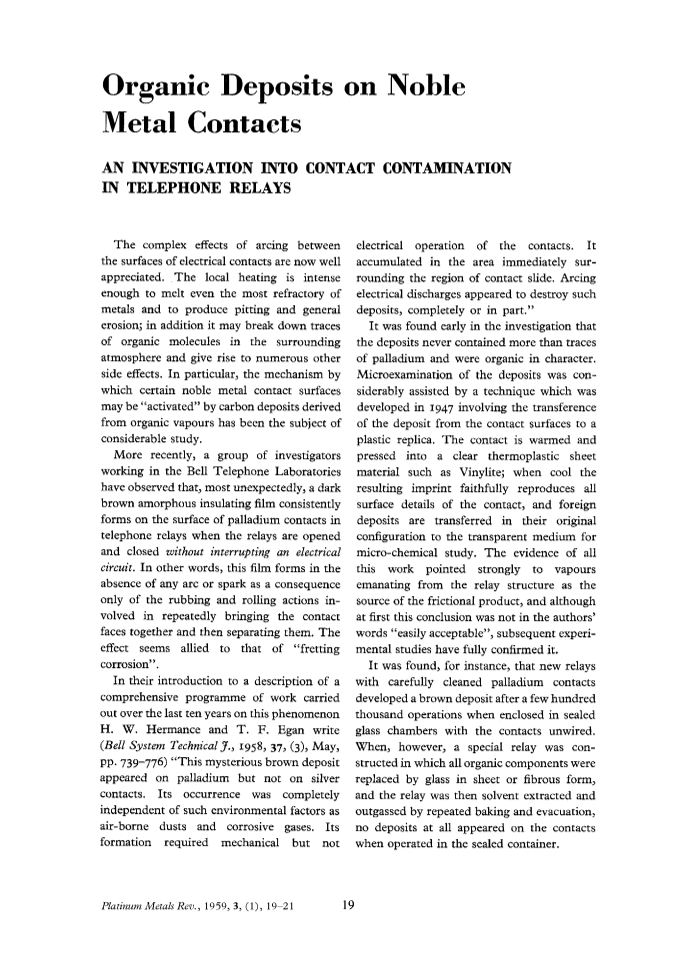



Organic Deposits on Noble Metal Contacts, Page 1 of 1
< Previous page Next page > /docserver/preview/fulltext/pmr/3/1/pmr0003-0019-1.gif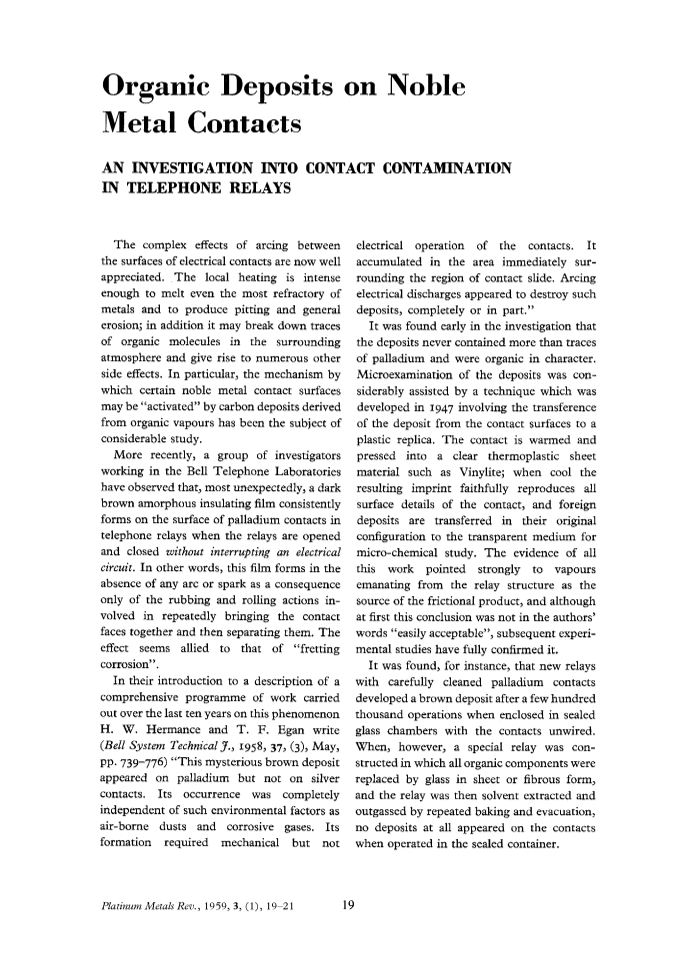
There is no abstract available.
© Johnson Matthey