-
oa Prevention of Contact Contamination in Sealed Relays
- Source: Platinum Metals Review, Volume 3, Issue 1, Jan 1959, p. 22 - 23
-
- 01 Jan 1959
Preview this article:
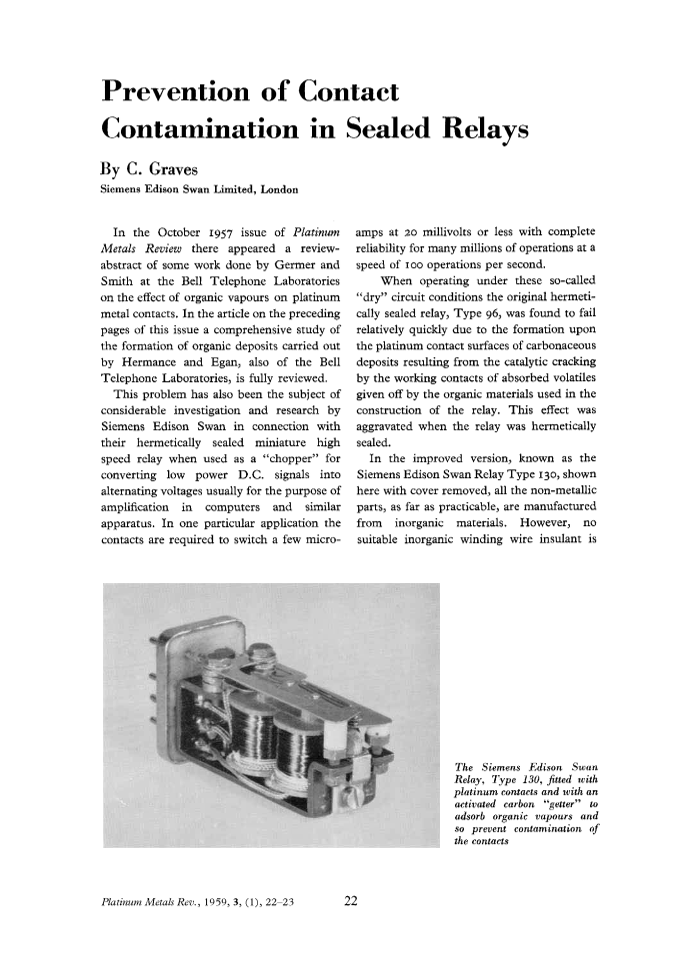



Prevention of Contact Contamination in Sealed Relays, Page 1 of 1
< Previous page Next page > /docserver/preview/fulltext/pmr/3/1/pmr0003-0022-1.gif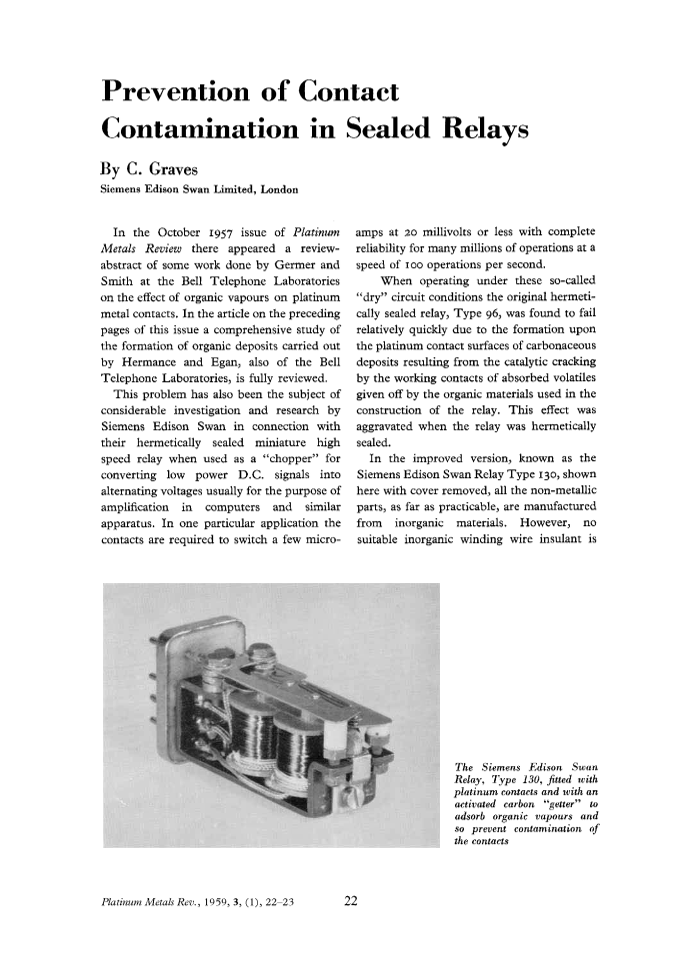
There is no abstract available.
© Johnson Matthey