-
oa Temperature Control in the Ford Foundry
Thermocouple Practice In The Production Of Grey Iron And Alloy Steel Castings
- Source: Platinum Metals Review, Volume 3, Issue 2, Apr 1959, p. 56 - 59
-
- 01 Jan 1959
Preview this article:
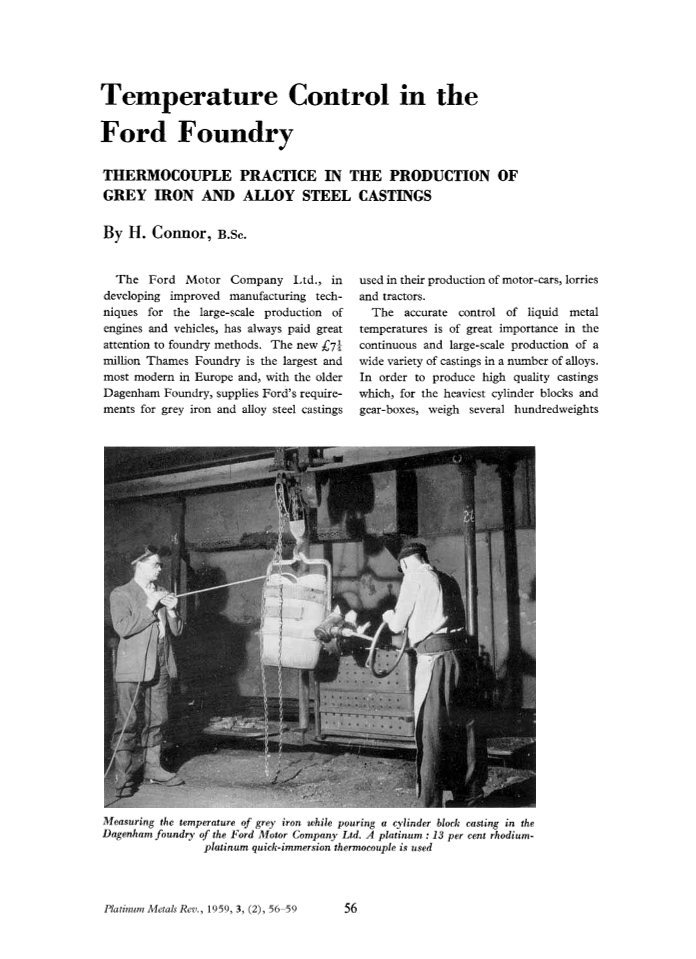



Temperature Control in the Ford Foundry, Page 1 of 1
< Previous page Next page > /docserver/preview/fulltext/pmr/3/2/pmr0003-0056-1.gif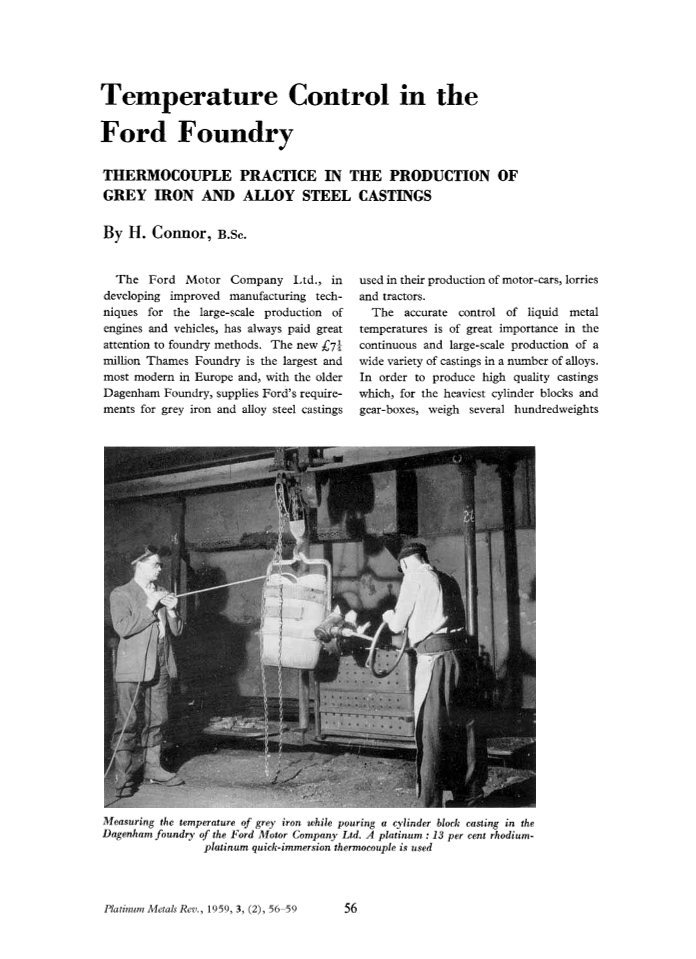
There is no abstract available.
© Johnson Matthey