-
oa Fixed Resistors for Use at High Temperatures
Noble Metal Films Provide Satisfactory Resistive Elements in Electronic Equipment
- Source: Platinum Metals Review, Volume 3, Issue 4, Oct 1959, p. 125 - 127
-
- 01 Jan 1959
Preview this article:
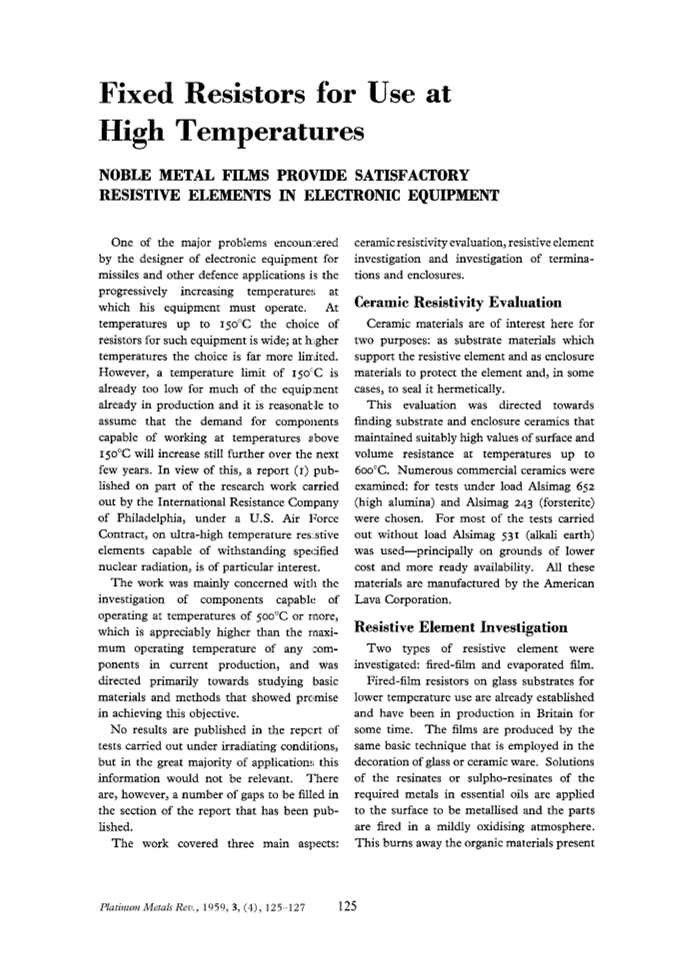



Fixed Resistors for Use at High Temperatures, Page 1 of 1
< Previous page Next page > /docserver/preview/fulltext/pmr/3/4/pmr0003-0125-1.gif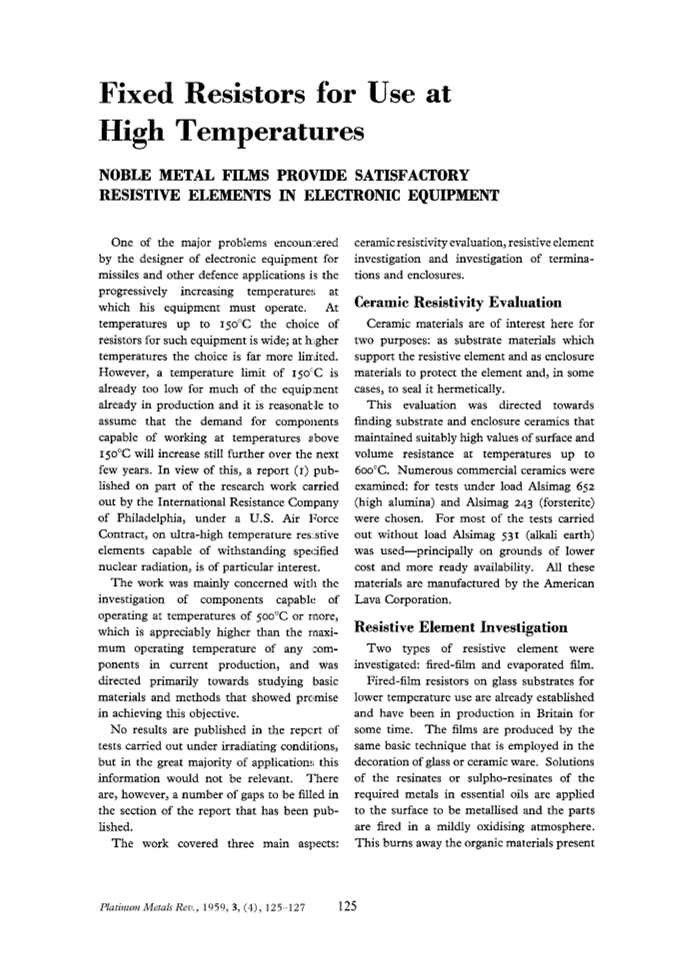
There is no abstract available.
© Johnson Matthey