-
oa New Techniques in the Manufacture of Platinum-Iridium Mass Standards
- Source: Platinum Metals Review, Volume 30, Issue 2, Apr 1986, p. 74 - 79
-
- 01 Jan 1986
Preview this article:
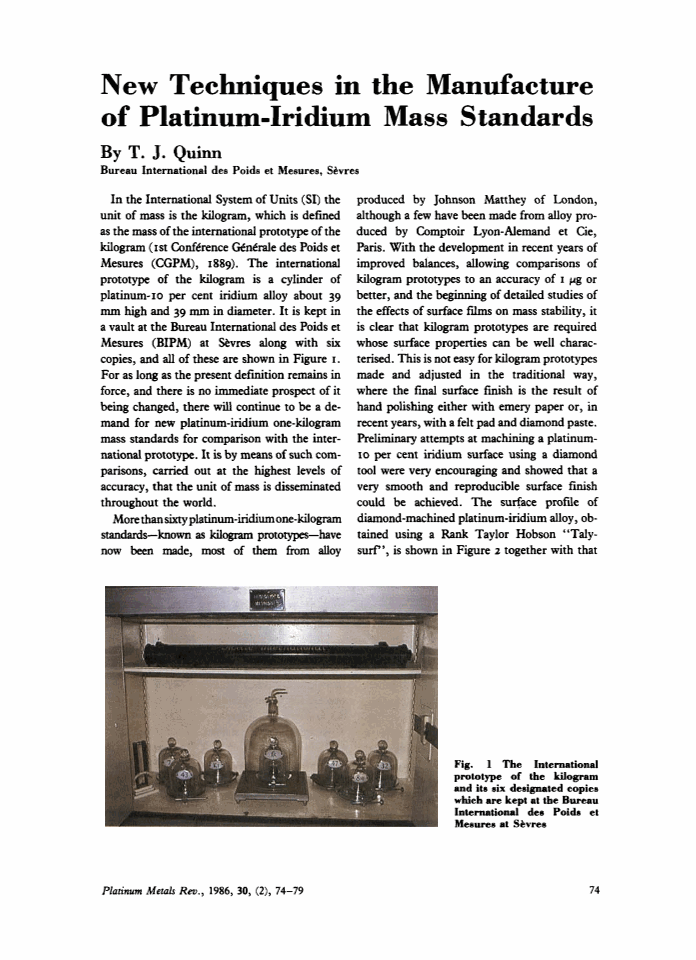



New Techniques in the Manufacture of Platinum-Iridium Mass Standards, Page 1 of 1
< Previous page Next page > /docserver/preview/fulltext/pmr/30/2/pmr0030-0074-1.gif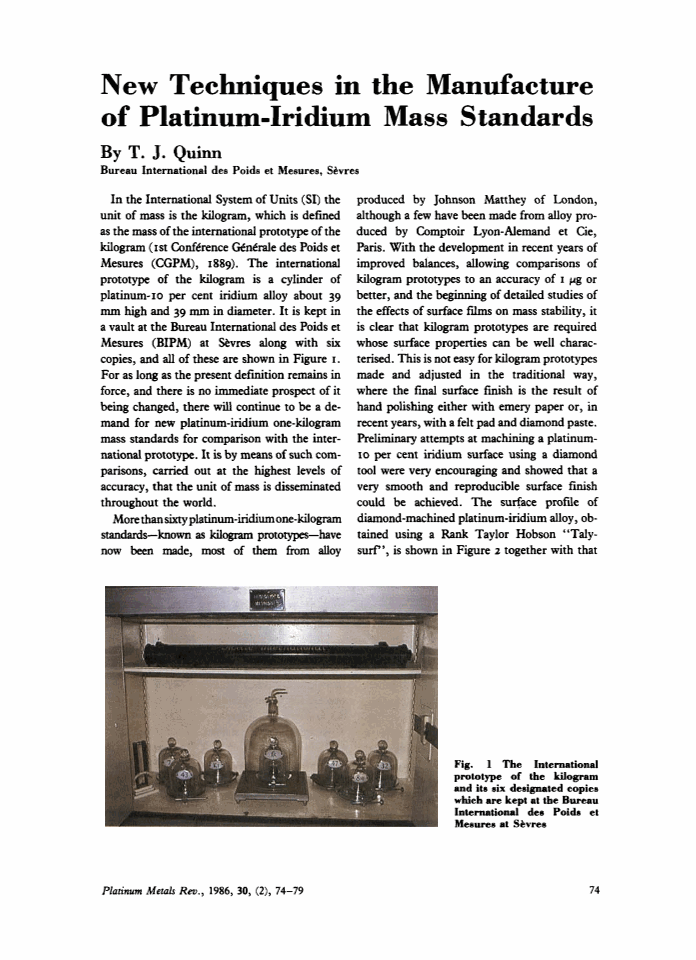
There is no abstract available.
© Johnson Matthey