-
oa New Platinum Analytical Standard
Synthetic Route to a Known Impurity Composition
- Source: Platinum Metals Review, Volume 31, Issue 3, Jul 1987, p. 133 - 136
-
- 01 Jan 1987
Preview this article:
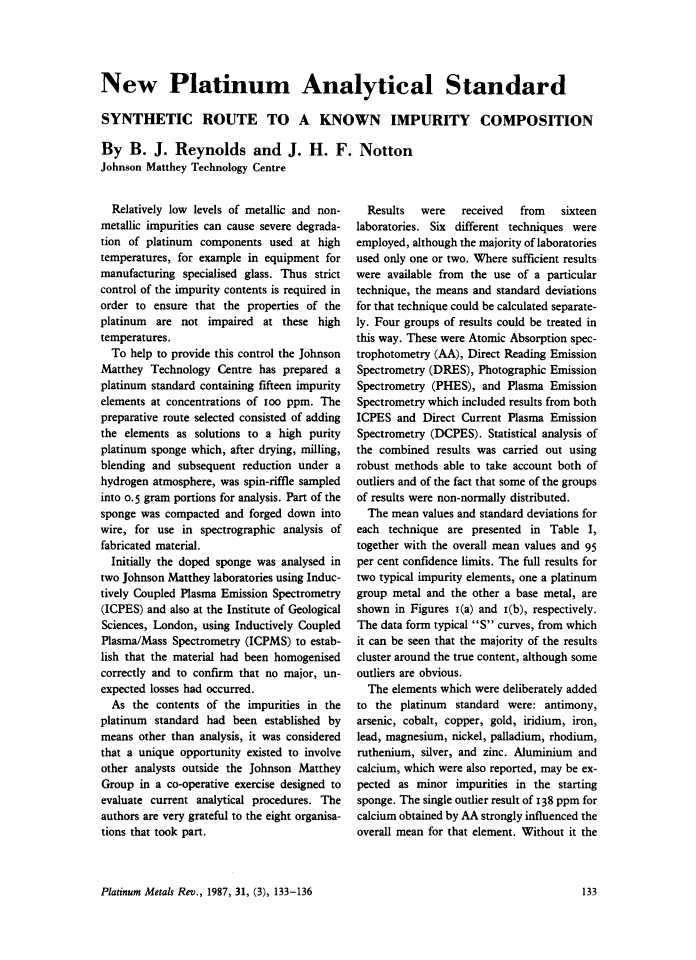



New Platinum Analytical Standard, Page 1 of 1
< Previous page Next page > /docserver/preview/fulltext/pmr/31/3/pmr0031-0133-1.gif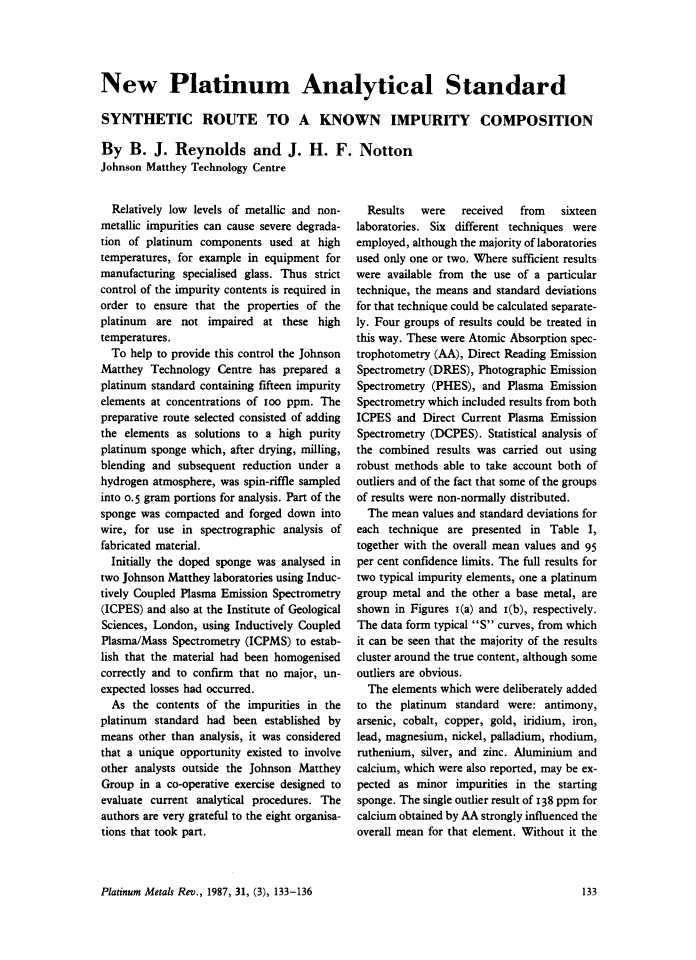
There is no abstract available.
© Johnson Matthey