-
oa Corrosion in Nitric Acid Plants
- Source: Platinum Metals Review, Volume 31, Issue 4, Oct 1987, p. 185 - 185
-
- 01 Jan 1987
Preview this article:
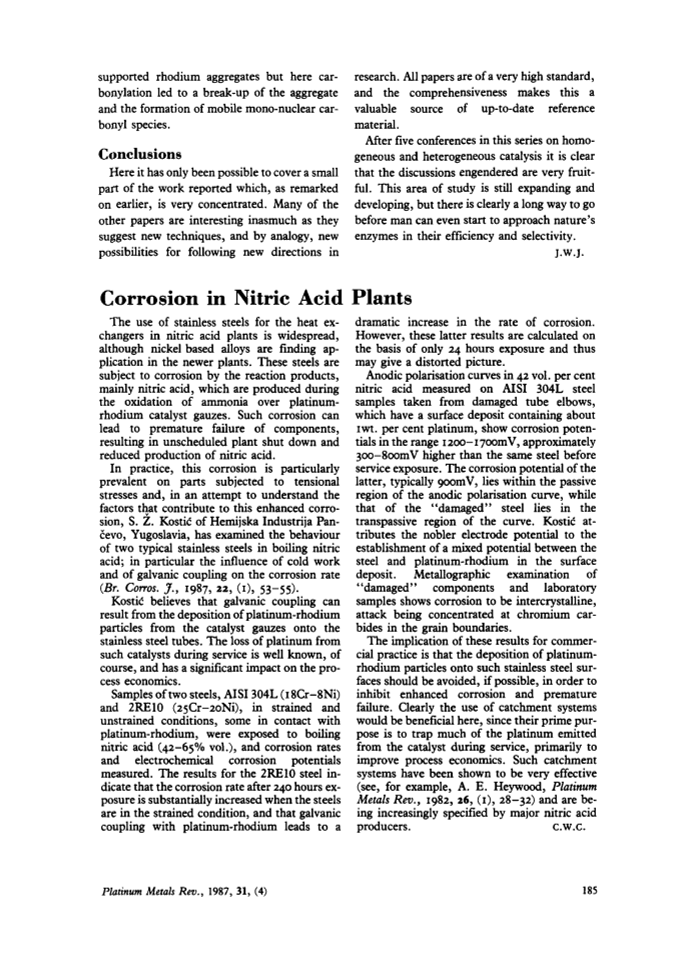



Corrosion in Nitric Acid Plants, Page 1 of 1
< Previous page Next page > /docserver/preview/fulltext/pmr/31/4/pmr0031-0185-1.gif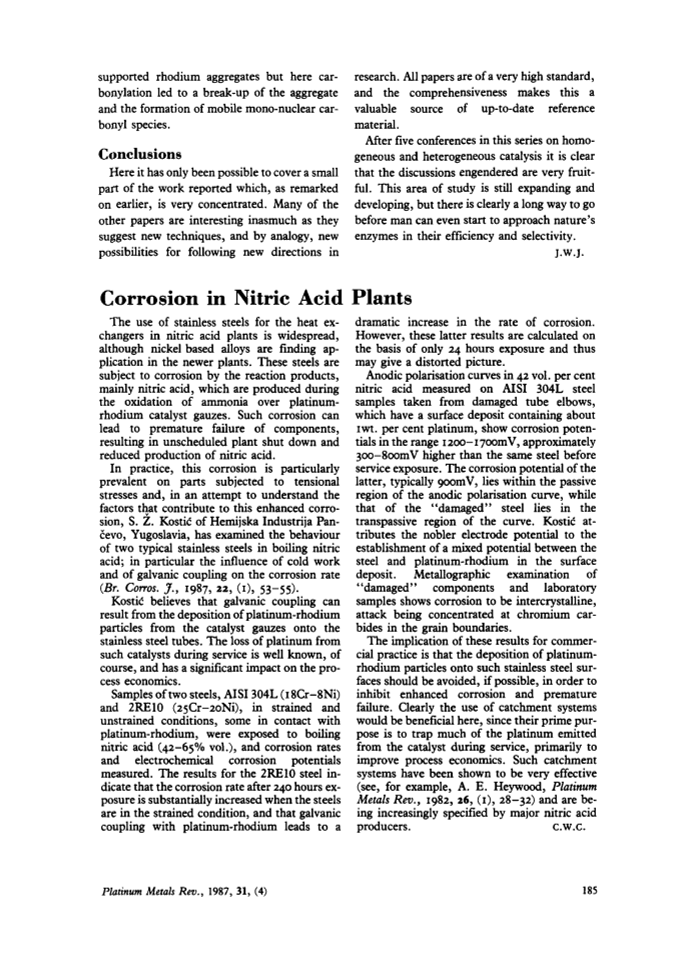
There is no abstract available.
© Johnson Matthey