-
oa Lean-Burn Oxygen Sensor Material
Platinum Catalyst Improves Response Time
- Source: Platinum Metals Review, Volume 32, Issue 4, Oct 1988, p. 199 - 199
-
- 01 Jan 1988
Preview this article:
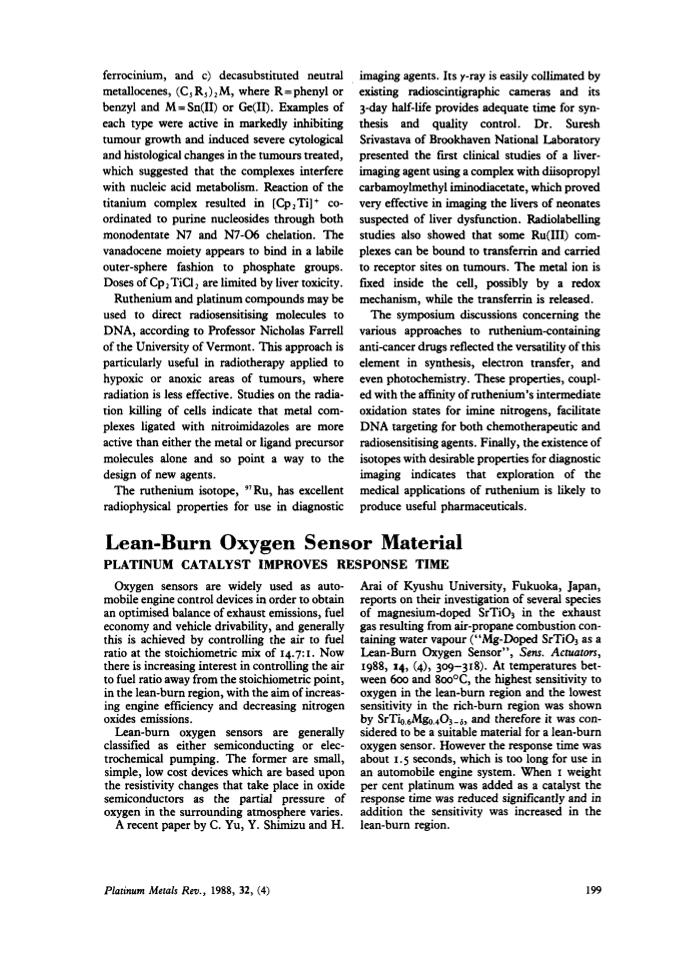



Lean-Burn Oxygen Sensor Material, Page 1 of 1
< Previous page Next page > /docserver/preview/fulltext/pmr/32/4/pmr0032-0199-1.gif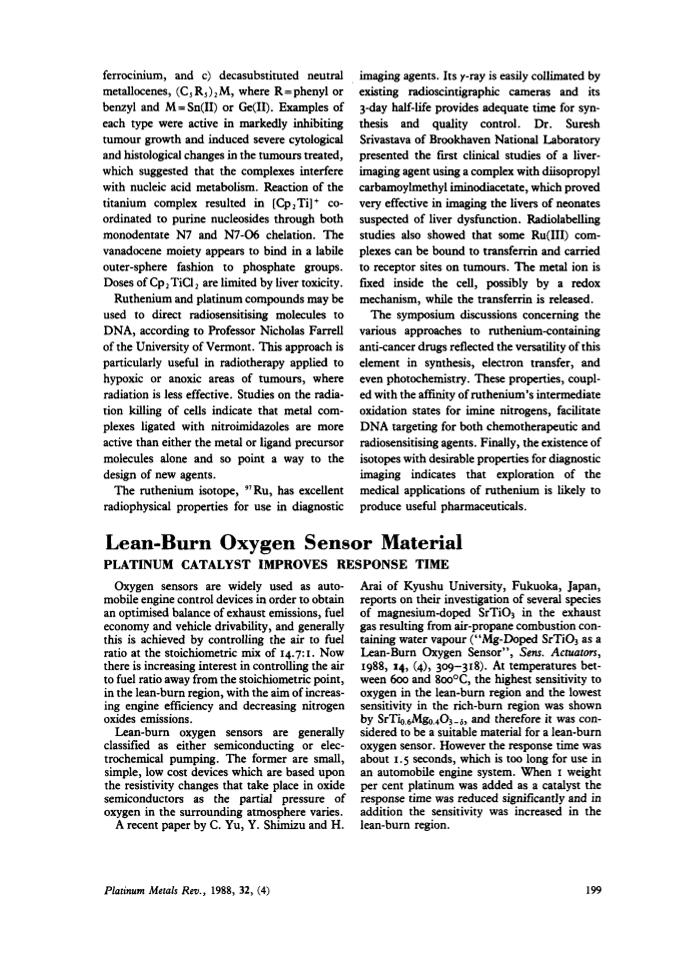
There is no abstract available.
© Johnson Matthey