-
oa The Hot Spot™ Reactor
Hydrogen Generation using A Novel Concept
- Source: Platinum Metals Review, Volume 33, Issue 3, Jul 1989, p. 118 - 127
-
- 01 Jan 1989
Preview this article:
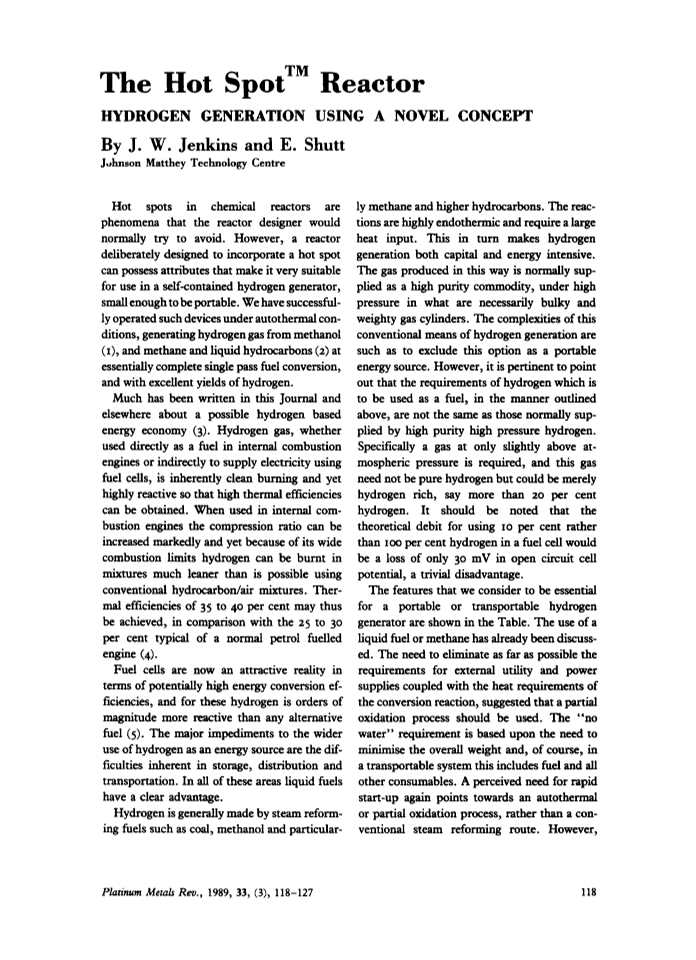



The Hot Spot™ Reactor, Page 1 of 1
< Previous page Next page > /docserver/preview/fulltext/pmr/33/3/pmr0033-0118-1.gif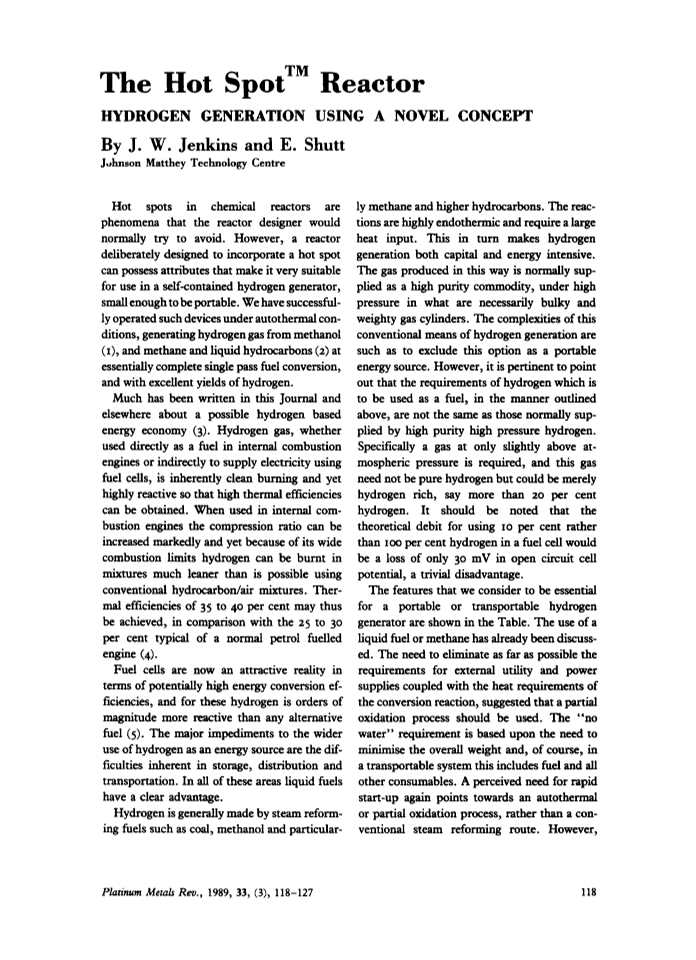
There is no abstract available.
© Johnson Matthey