-
oa Electrochemical Destruction of Toxic Organic Industrial Waste
- Source: Platinum Metals Review, Volume 34, Issue 1, Jan 1990, p. 10 - 14
-
- 01 Jan 1990
Preview this article:
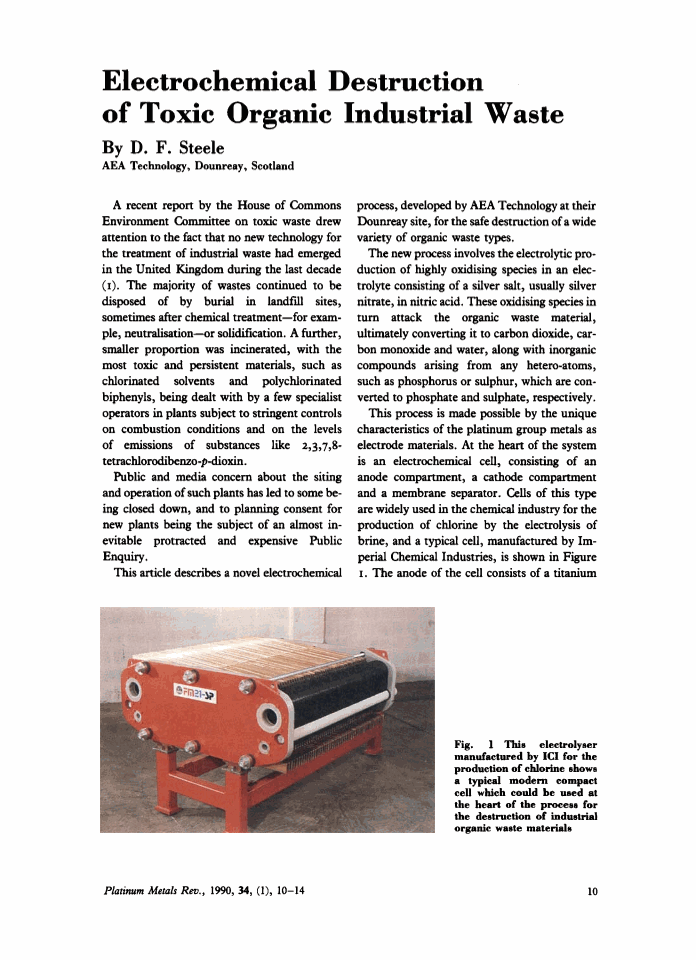



Electrochemical Destruction of Toxic Organic Industrial Waste, Page 1 of 1
< Previous page Next page > /docserver/preview/fulltext/pmr/34/1/pmr0034-0010-1.gif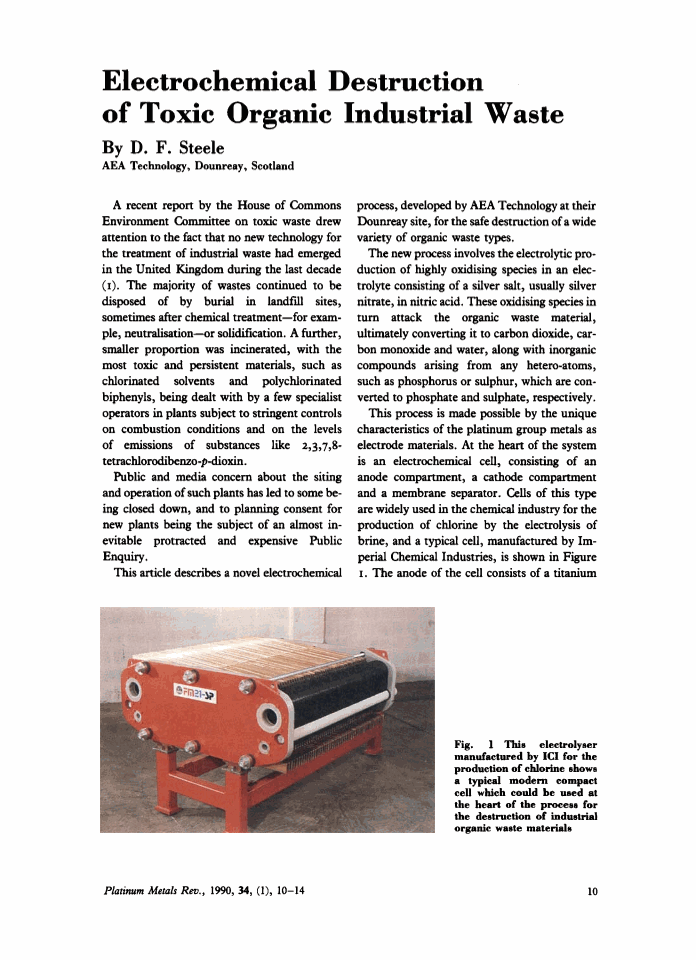
There is no abstract available.
© Johnson Matthey