-
oa Ternary and Complex Rhodium Alloys
An Investigation of Mechanical Properties
- Source: Platinum Metals Review, Volume 34, Issue 4, Oct 1990, p. 192 - 204
-
- 01 Oct 1990
Preview this article:
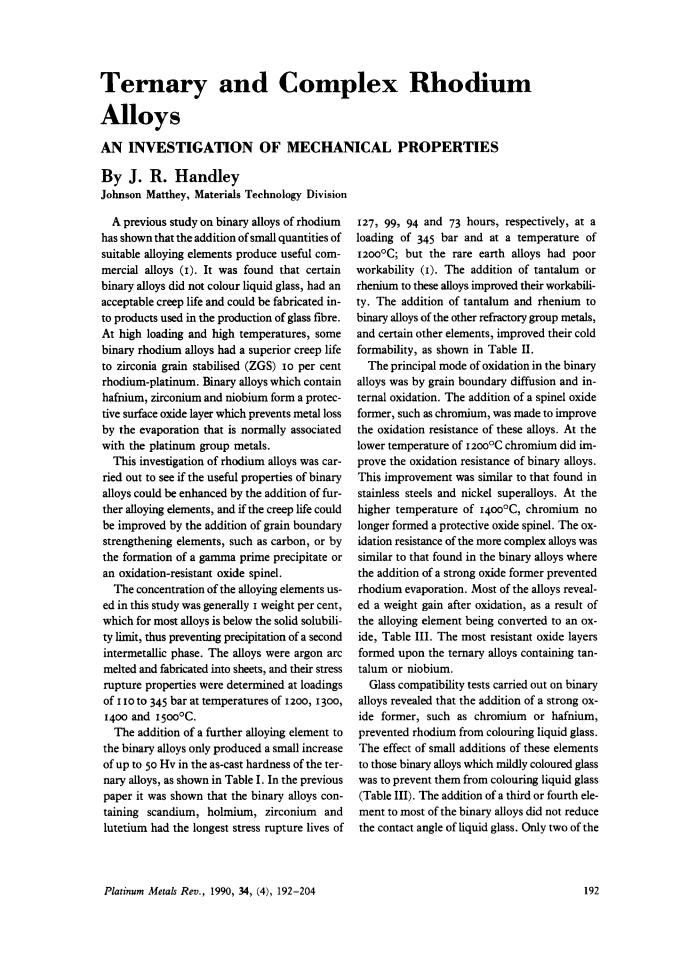



Ternary and Complex Rhodium Alloys, Page 1 of 1
< Previous page Next page > /docserver/preview/fulltext/pmr/34/4/pmr0034-0192-1.gif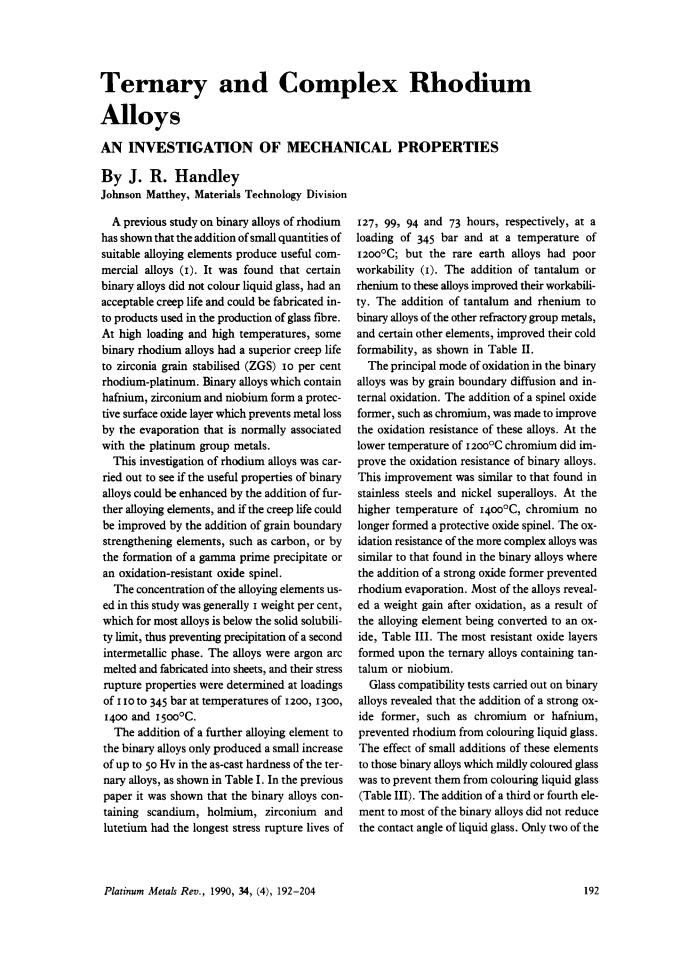
There is no abstract available.
© Johnson Matthey