-
oa A Means to a Cleaner Environment
Energy Efficient Platinum-Containing Fuel Cells to be Introduced Commercially in the Early 1990s
- Source: Platinum Metals Review, Volume 35, Issue 1, Jan 1991, p. 17 - 21
-
- 01 Jan 1991
Preview this article:
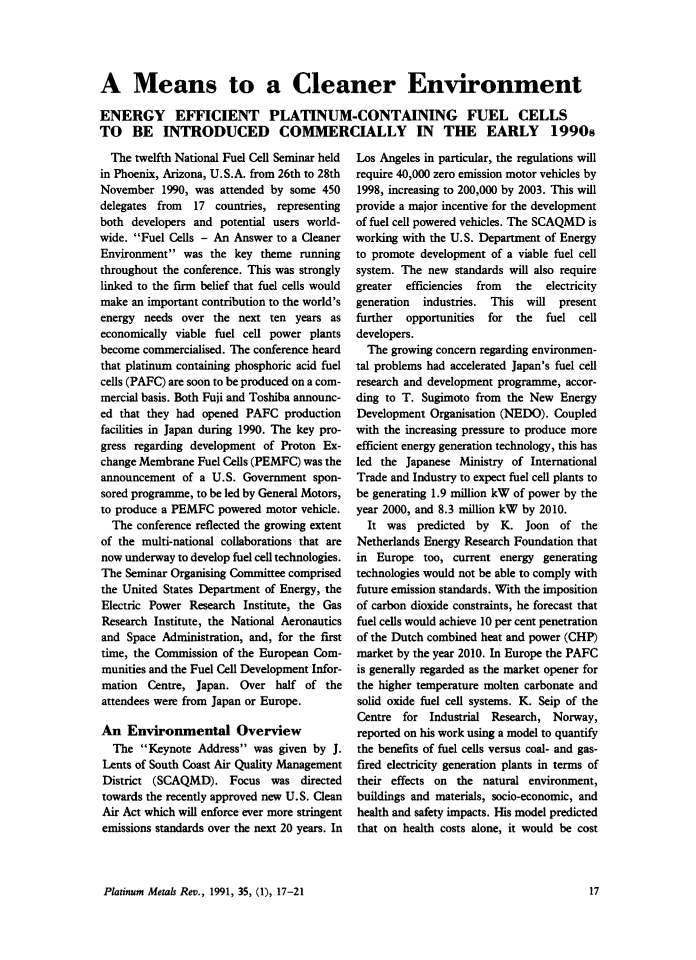



A Means to a Cleaner Environment, Page 1 of 1
< Previous page Next page > /docserver/preview/fulltext/pmr/35/1/pmr0035-0017-1.gif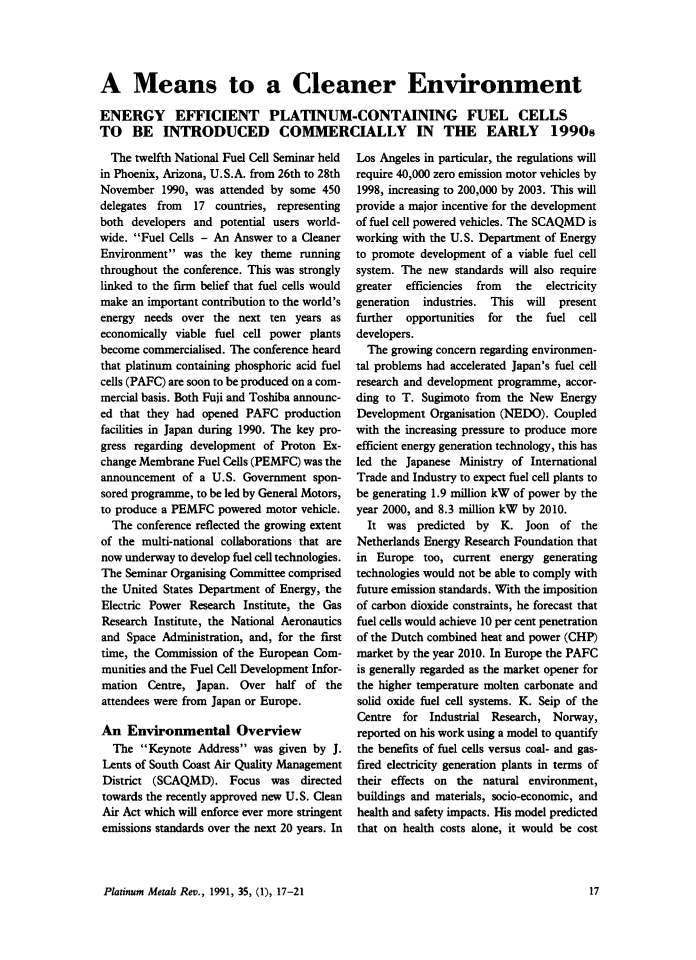
There is no abstract available.
© Johnson Matthey