-
oa Solid State Amorphisation of the Platinum Metals
A Review of Some Recent Publications
- Source: Platinum Metals Review, Volume 35, Issue 2, Apr 1991, p. 83 - 85
-
- 01 Jan 1991
Preview this article:
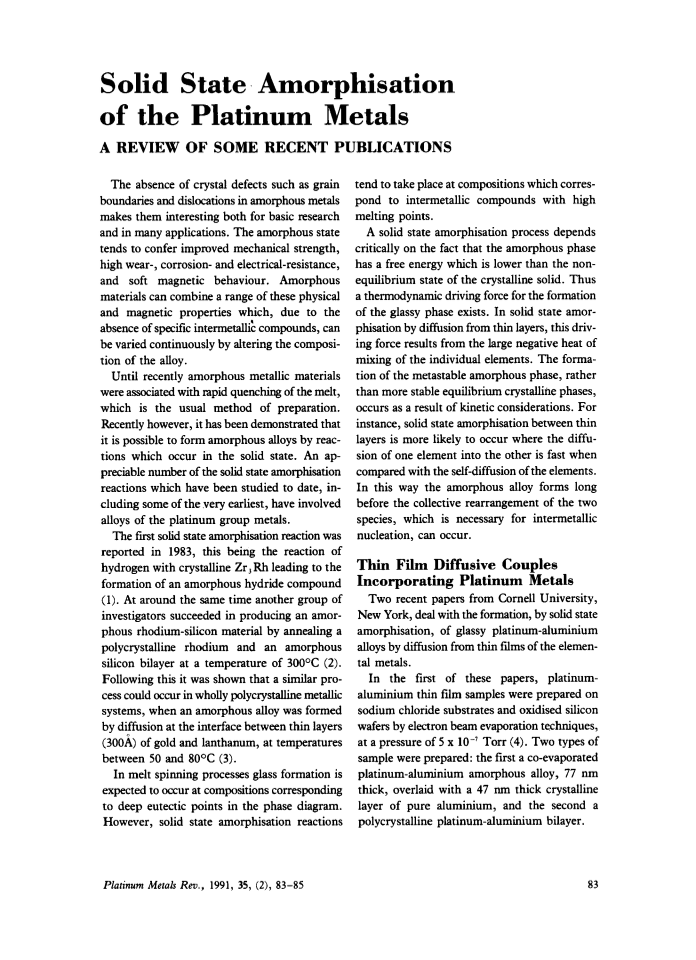



Solid State Amorphisation of the Platinum Metals, Page 1 of 1
< Previous page Next page > /docserver/preview/fulltext/pmr/35/2/pmr0035-0083-1.gif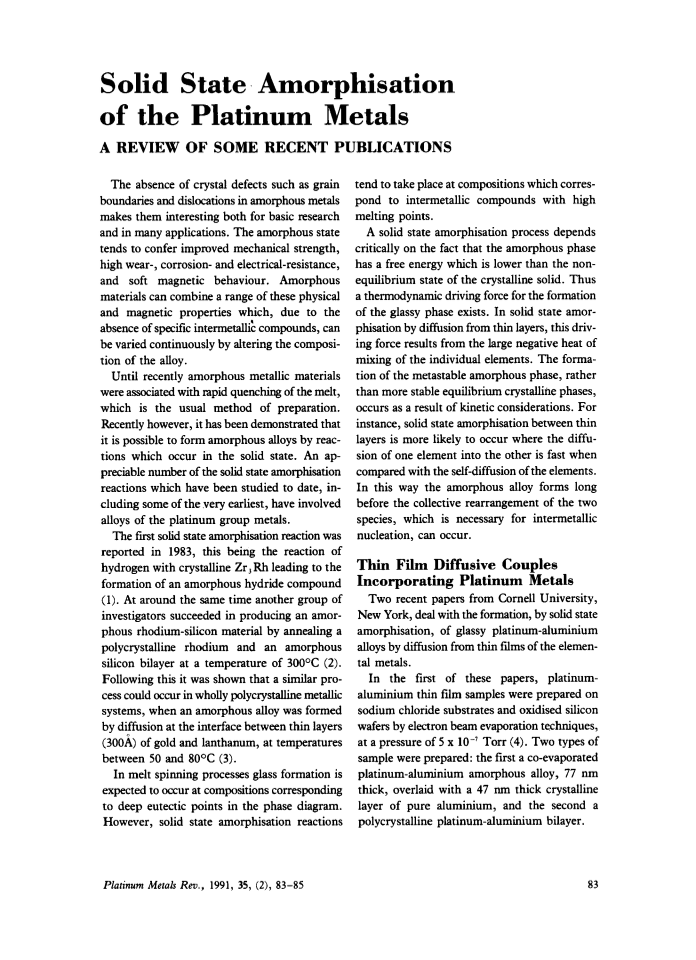
There is no abstract available.
© Johnson Matthey