-
oa Enhanced Oxidation Resistance
Role of Palladium in Refractory Metal Alloys
- Source: Platinum Metals Review, Volume 35, Issue 3, Jul 1991, p. 133 - 133
-
- 01 Jan 1991
Preview this article:
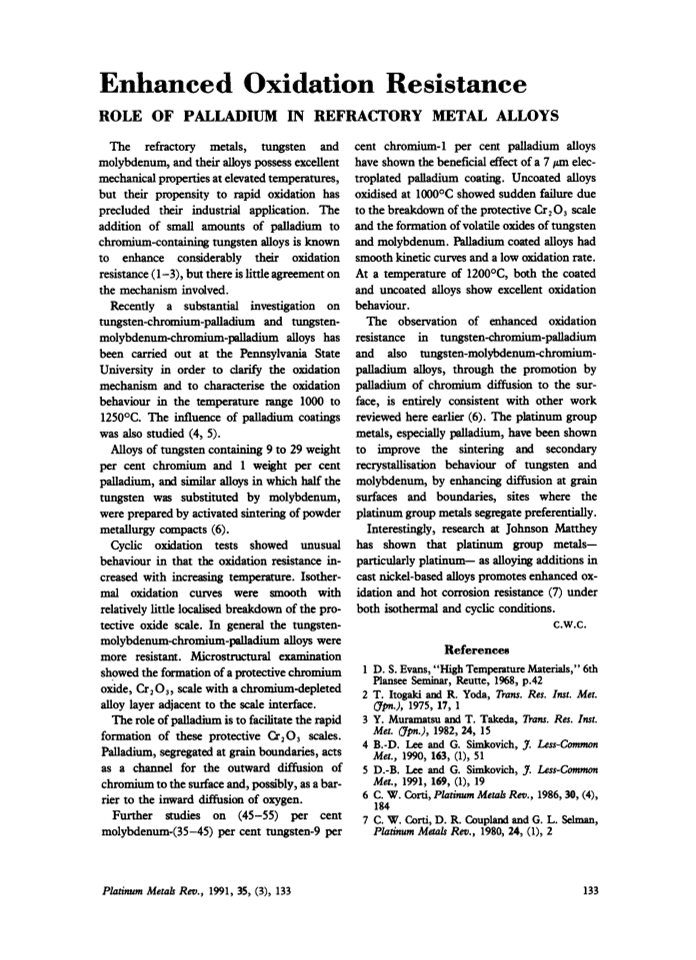



Enhanced Oxidation Resistance, Page 1 of 1
< Previous page Next page > /docserver/preview/fulltext/pmr/35/3/pmr0035-0133-1.gif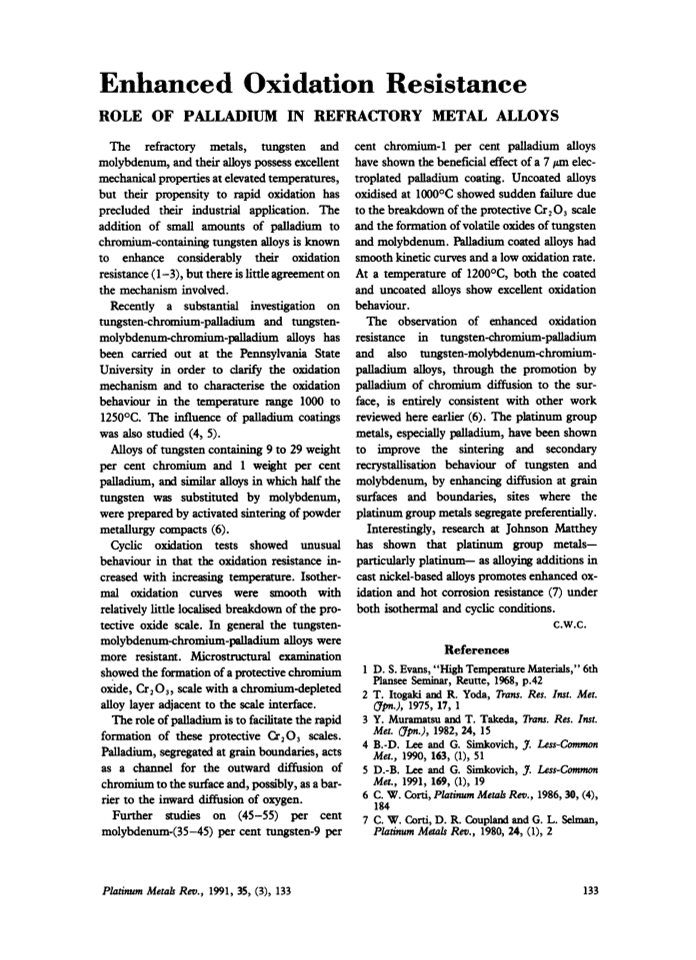
There is no abstract available.
© Johnson Matthey