-
oa III-V Semiconductor Vapour Growth
Application of Palladium-Silver Diffusion Membranes and the Restoration of Hydrogen Output
- Source: Platinum Metals Review, Volume 36, Issue 1, Jan 1992, p. 12 - 13
-
- 01 Jan 1992
Preview this article:
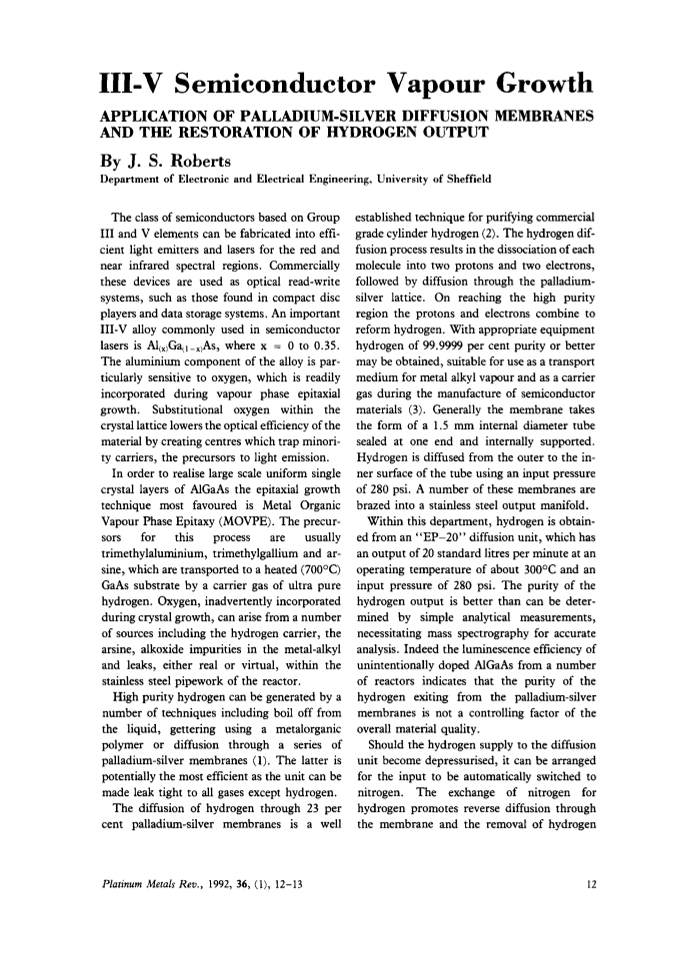



III-V Semiconductor Vapour Growth, Page 1 of 1
< Previous page Next page > /docserver/preview/fulltext/pmr/36/1/pmr0036-0012-1.gif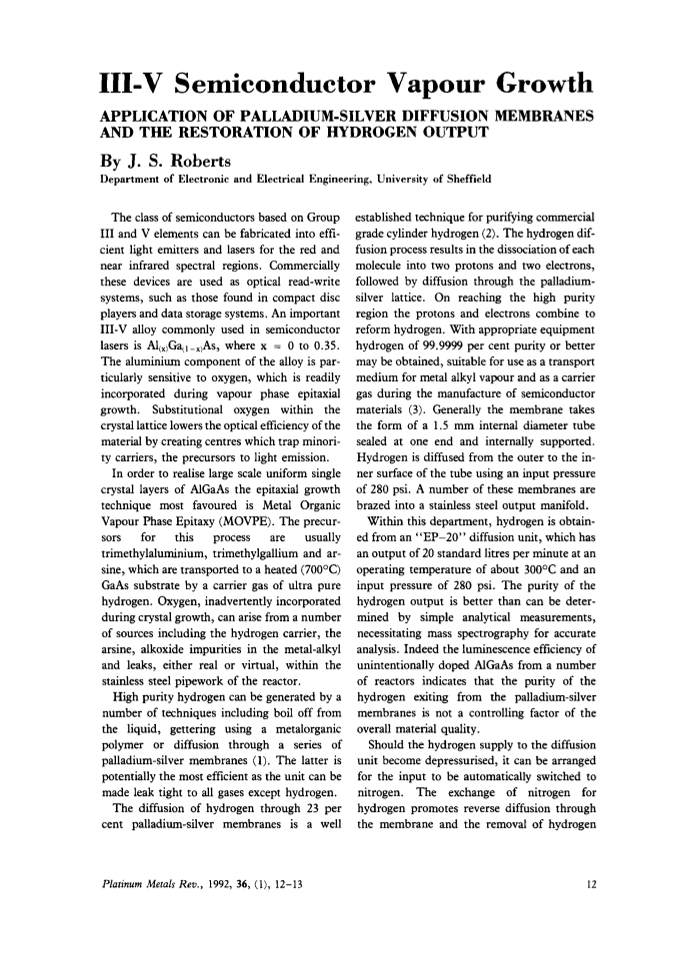
There is no abstract available.
© Johnson Matthey