-
oa The Large Scale Production of Hydrogen from Gas Mixtures
A Use for Ultra Thin Palladium Alloy Membranes
- Source: Platinum Metals Review, Volume 36, Issue 2, Apr 1992, p. 90 - 97
-
- 01 Jan 1992
Preview this article:
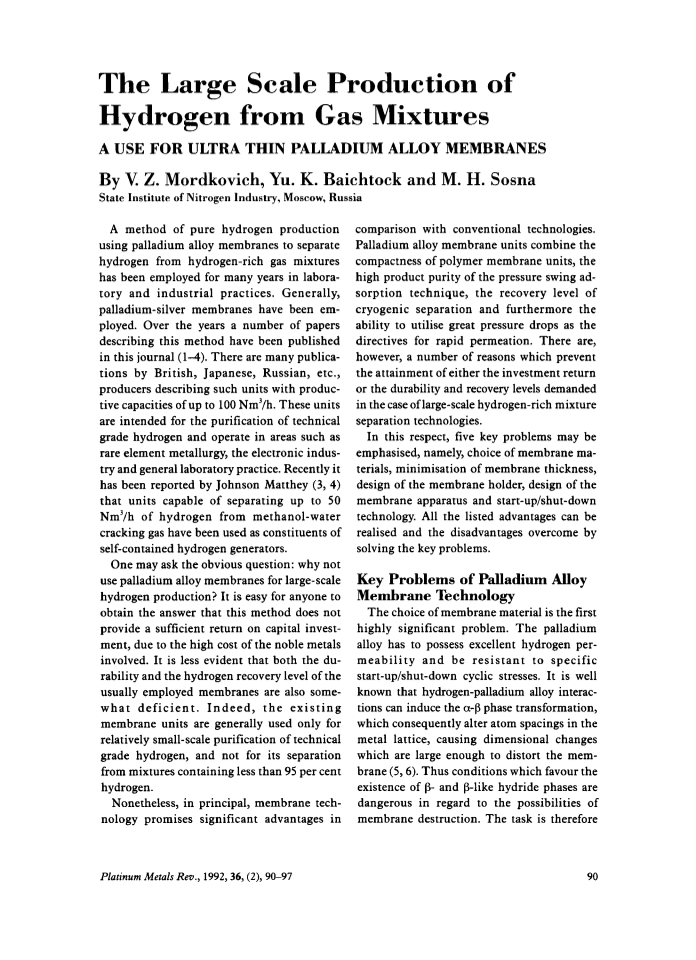



The Large Scale Production of Hydrogen from Gas Mixtures, Page 1 of 1
< Previous page Next page > /docserver/preview/fulltext/pmr/36/2/pmr0036-0090-1.gif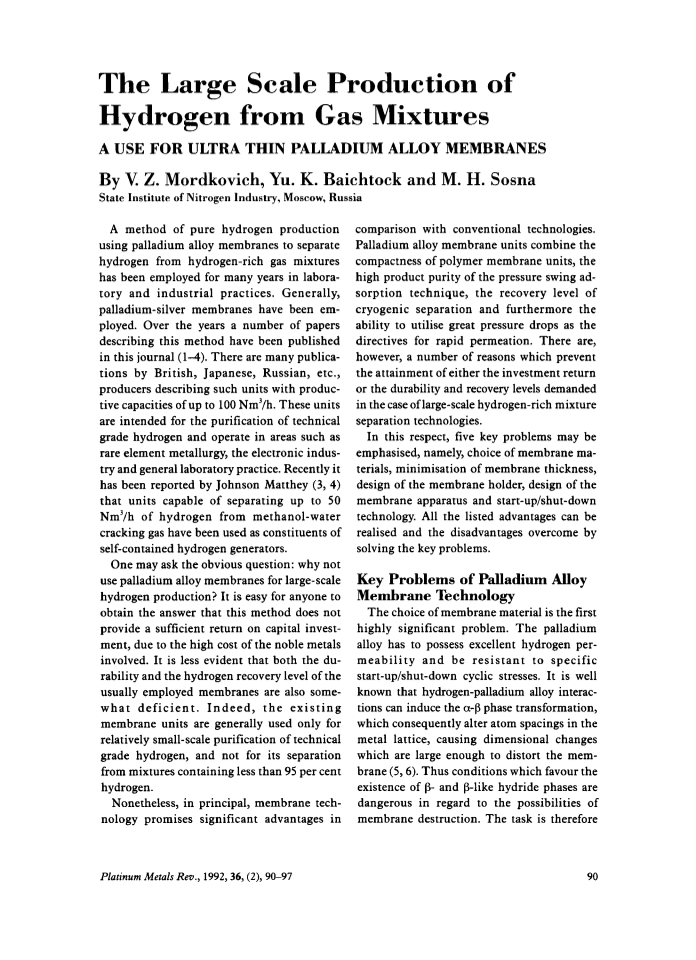
There is no abstract available.
© Johnson Matthey