-
oa Intermetallic Compounds for High-Temperature Structural Use
Unique Iridium and Ruthenium Compounds
- Source: Platinum Metals Review, Volume 36, Issue 3, Jul 1992, p. 138 - 145
-
- 01 Jan 1992
Preview this article:
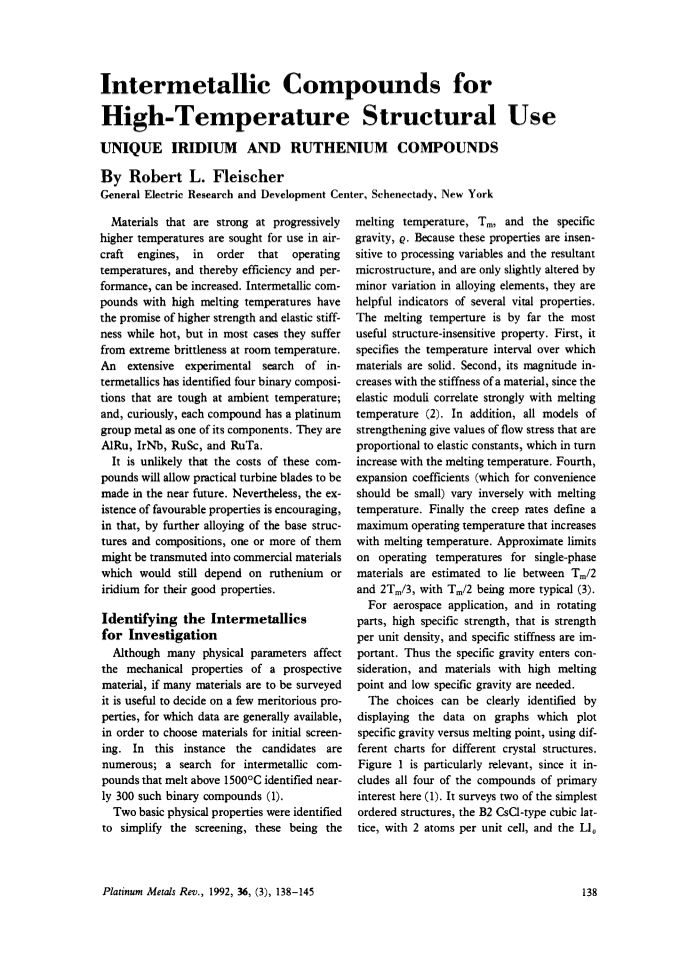



Intermetallic Compounds for High-Temperature Structural Use, Page 1 of 1
< Previous page Next page > /docserver/preview/fulltext/pmr/36/3/pmr0036-0138-1.gif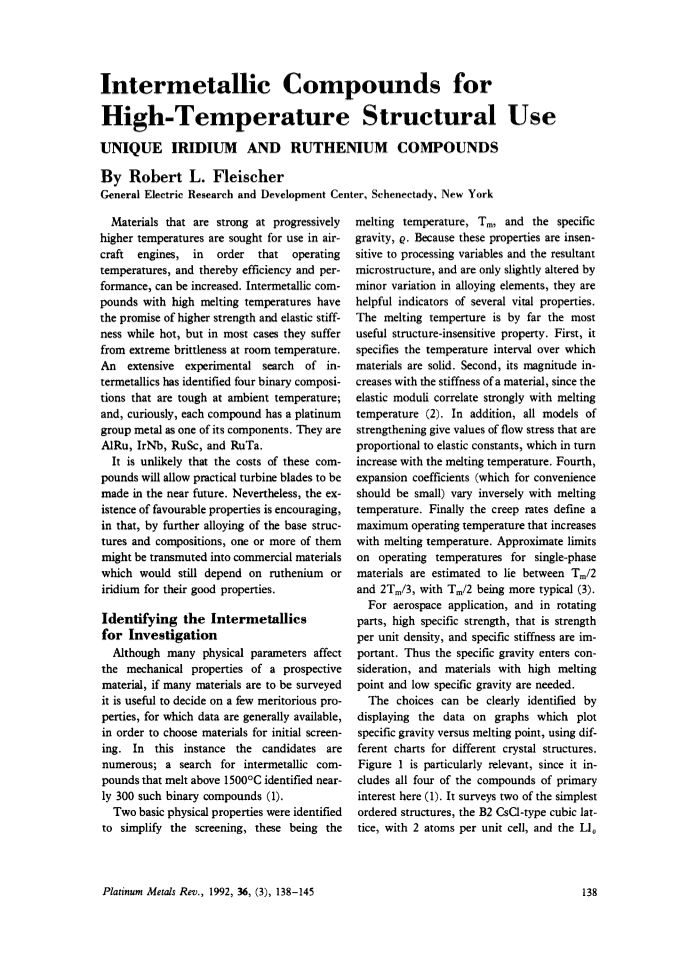
There is no abstract available.
© Johnson Matthey