-
oa A Selective Review of Metal-Hydrogen Technology in the Former U.S.S.R.
Advanced Palladium Applications Featured
- Source: Platinum Metals Review, Volume 37, Issue 2, Apr 1993, p. 97 - 101
-
- 01 Jan 1993
Preview this article:
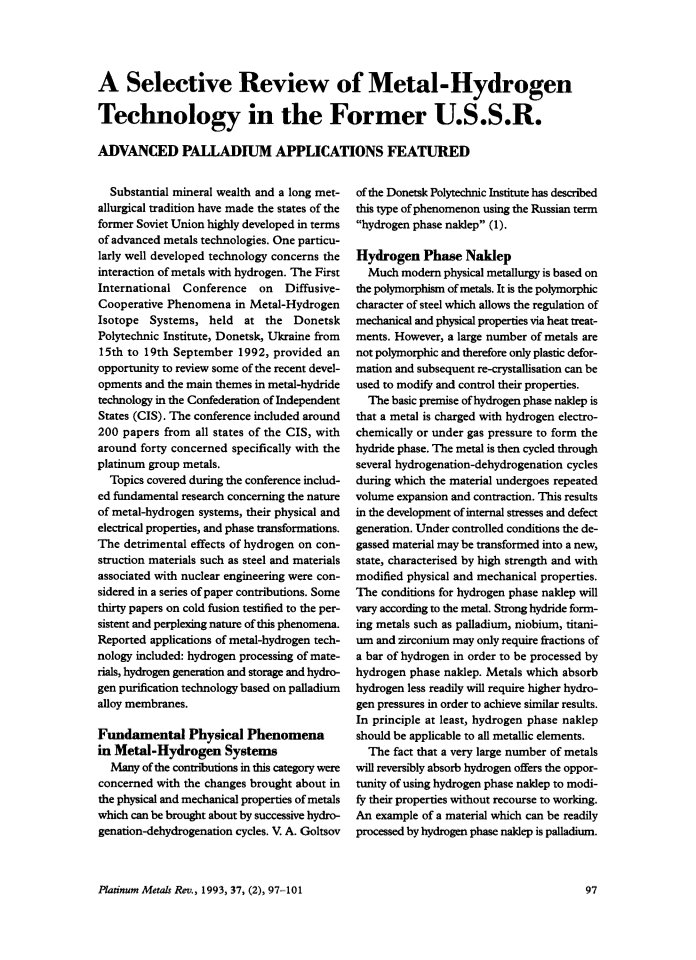



A Selective Review of Metal-Hydrogen Technology in the Former U.S.S.R., Page 1 of 1
< Previous page Next page > /docserver/preview/fulltext/pmr/37/2/pmr0037-0097-1.gif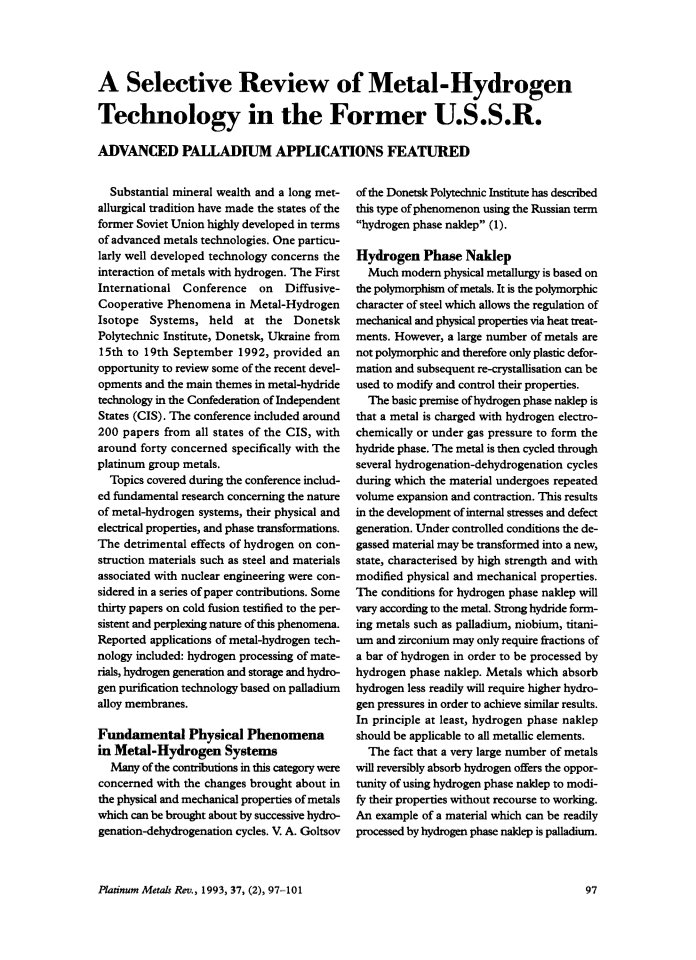
There is no abstract available.
© Johnson Matthey