-
oa Membrane Catalysis and the Platinum Group Metals
A Review of Two Recent Publications
- Source: Platinum Metals Review, Volume 37, Issue 3, Jul 1993, p. 153 - 158
-
- 01 Jan 1993
Preview this article:
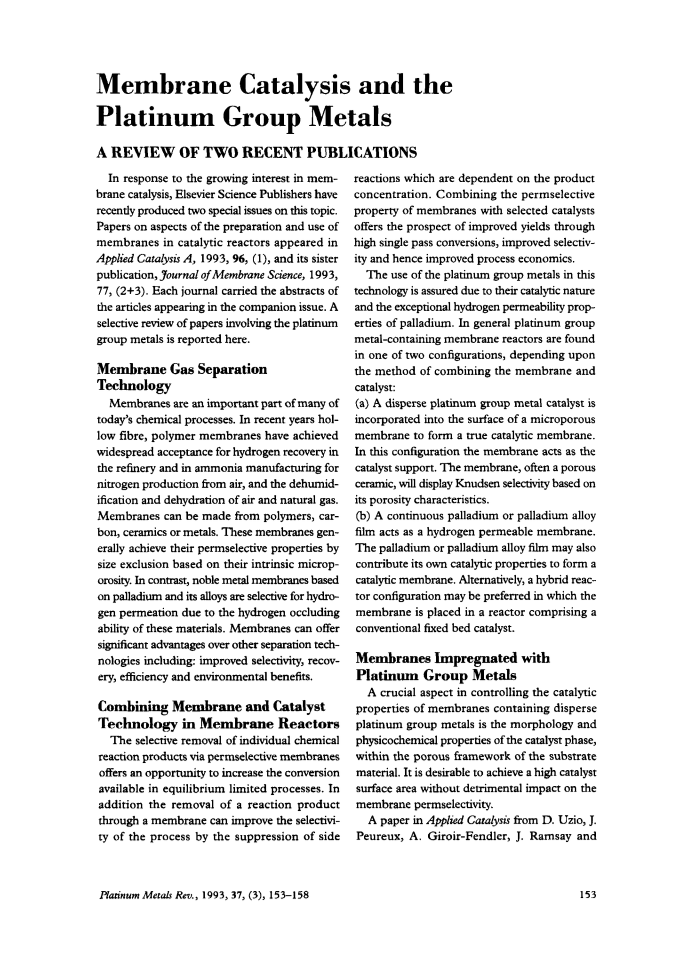



Membrane Catalysis and the Platinum Group Metals, Page 1 of 1
< Previous page Next page > /docserver/preview/fulltext/pmr/37/3/pmr0037-0153-1.gif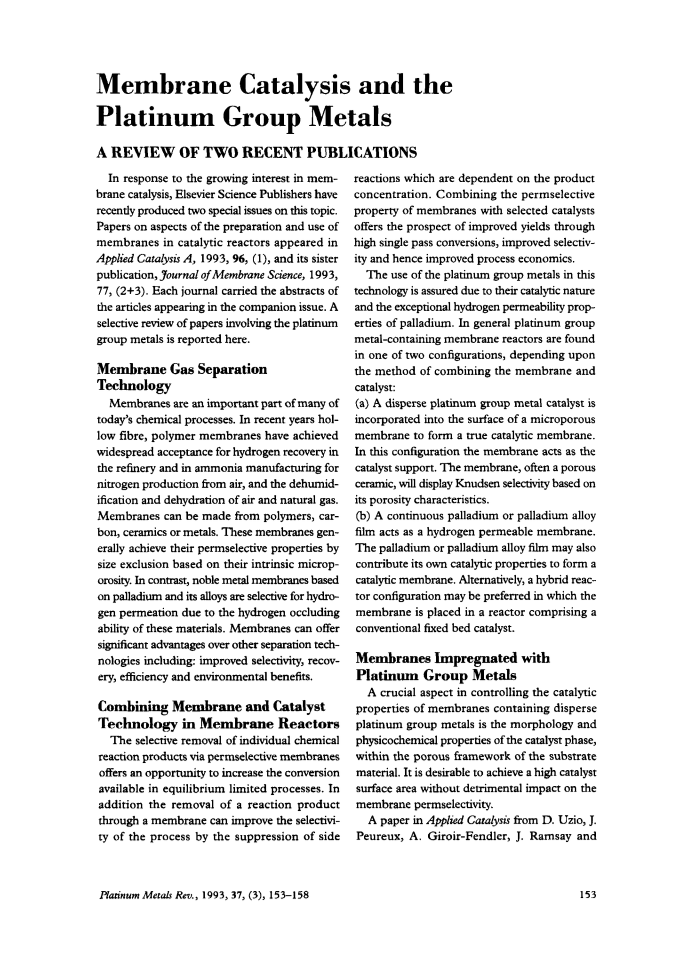
There is no abstract available.
© Johnson Matthey