-
oa Tough Wear Resistant Alloys of Zirconium-Palladium-Ruthenium
- Source: Platinum Metals Review, Volume 37, Issue 4, Oct 1993, p. 194 - 196
-
- 01 Jan 1993
Preview this article:
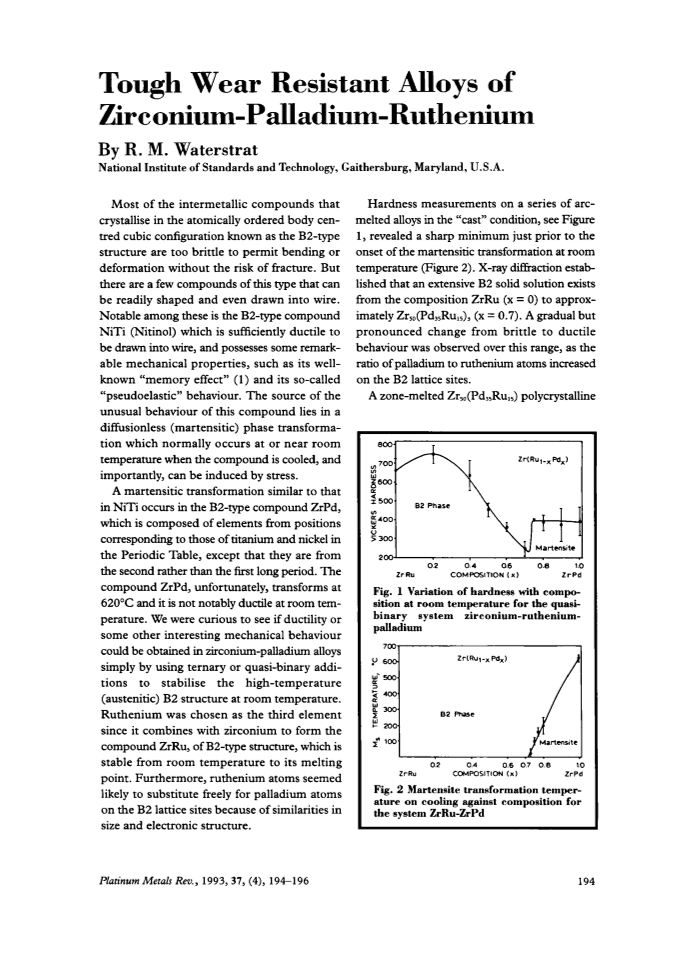



Tough Wear Resistant Alloys of Zirconium-Palladium-Ruthenium, Page 1 of 1
< Previous page Next page > /docserver/preview/fulltext/pmr/37/4/pmr0037-0194-1.gif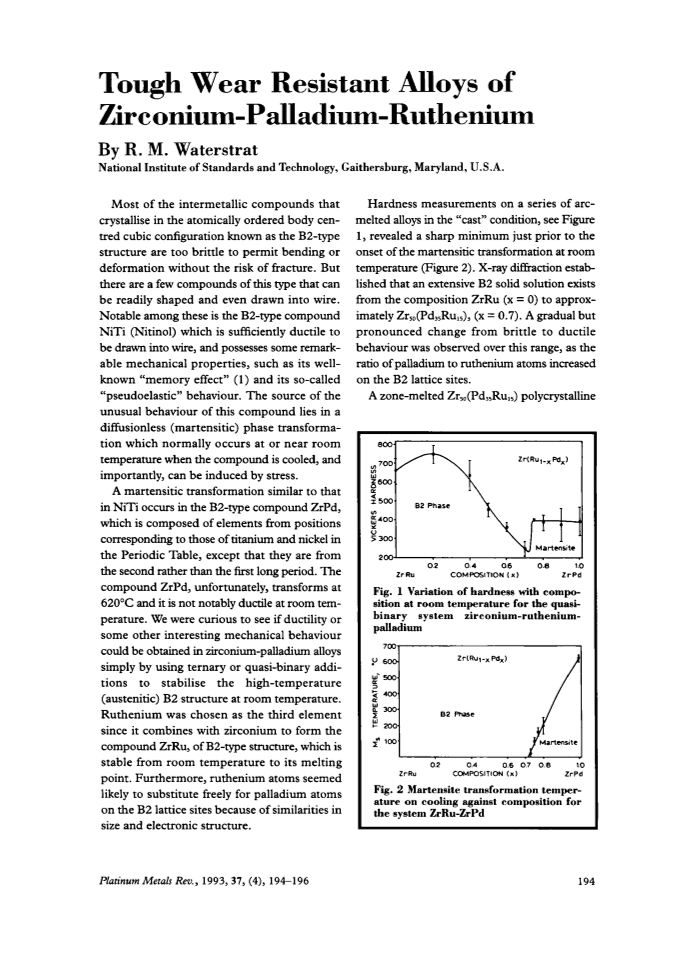
There is no abstract available.
© Johnson Matthey