-
oa Third Grove Fuel Cell Symposium
Platinum Metals-Loaded Polymer Membrane Fuel Cells Progress to Electric Traction
- Source: Platinum Metals Review, Volume 37, Issue 4, Oct 1993, p. 197 - 209
-
- 01 Jan 1993
Preview this article:
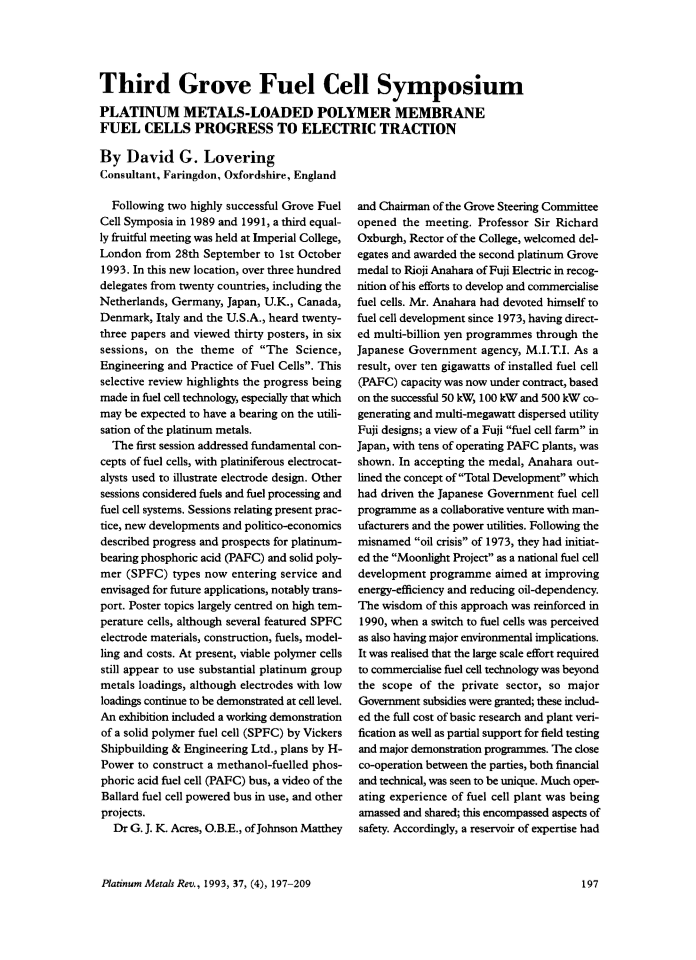



Third Grove Fuel Cell Symposium, Page 1 of 1
< Previous page Next page > /docserver/preview/fulltext/pmr/37/4/pmr0037-0197-1.gif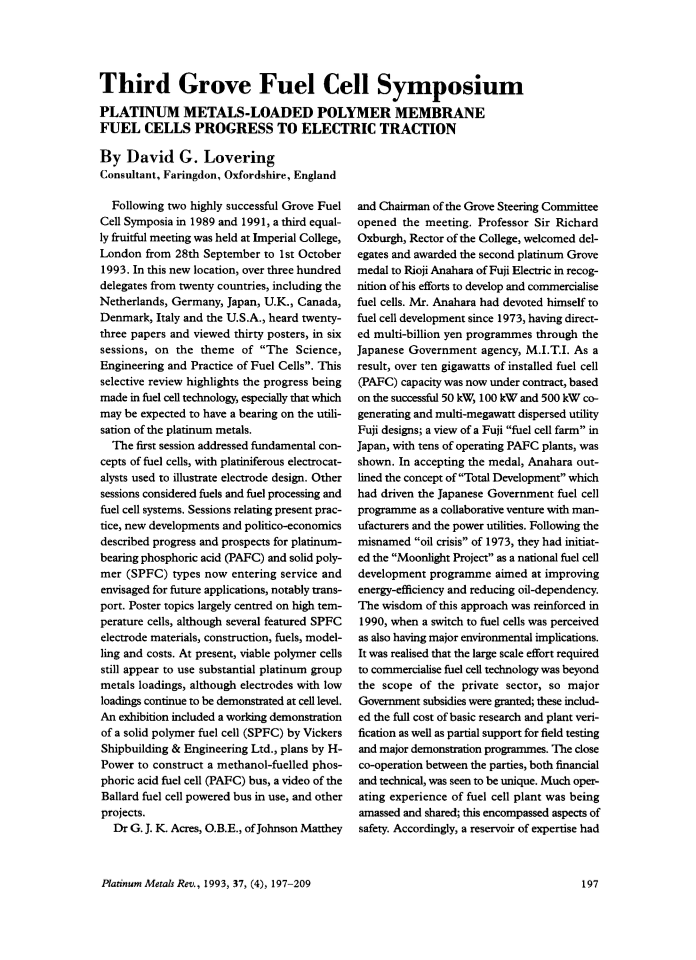
There is no abstract available.
© Johnson Matthey