-
oa Iridium Coatings on Structural Carbon Materials
- Source: Platinum Metals Review, Volume 37, Issue 4, Oct 1993, p. 219 - 219
-
- 01 Jan 1993
Preview this article:
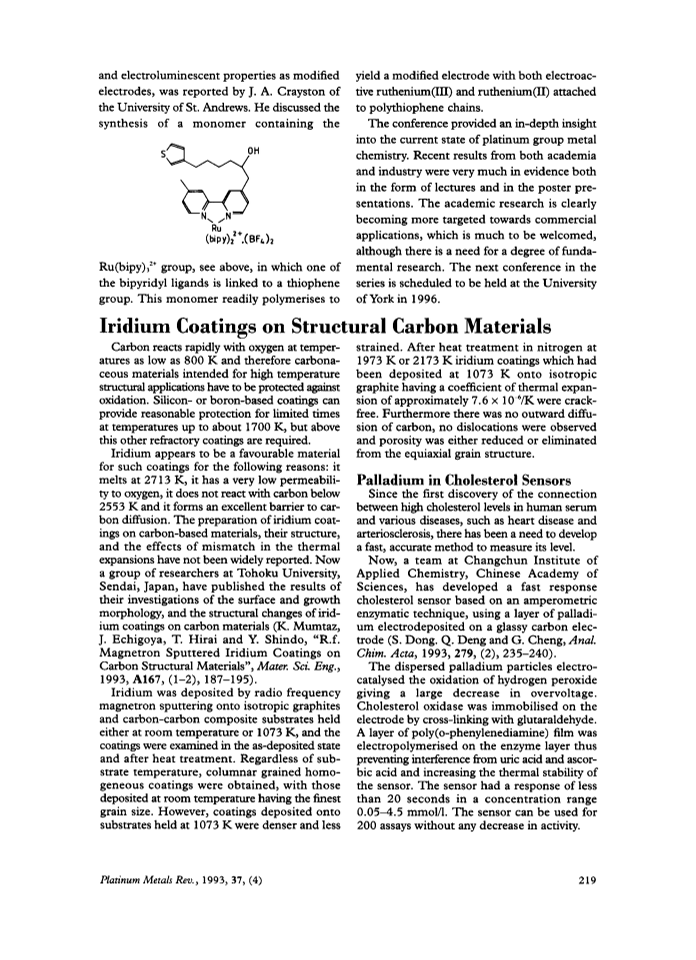



Iridium Coatings on Structural Carbon Materials, Page 1 of 1
< Previous page Next page > /docserver/preview/fulltext/pmr/37/4/pmr0037-0219a-1.gif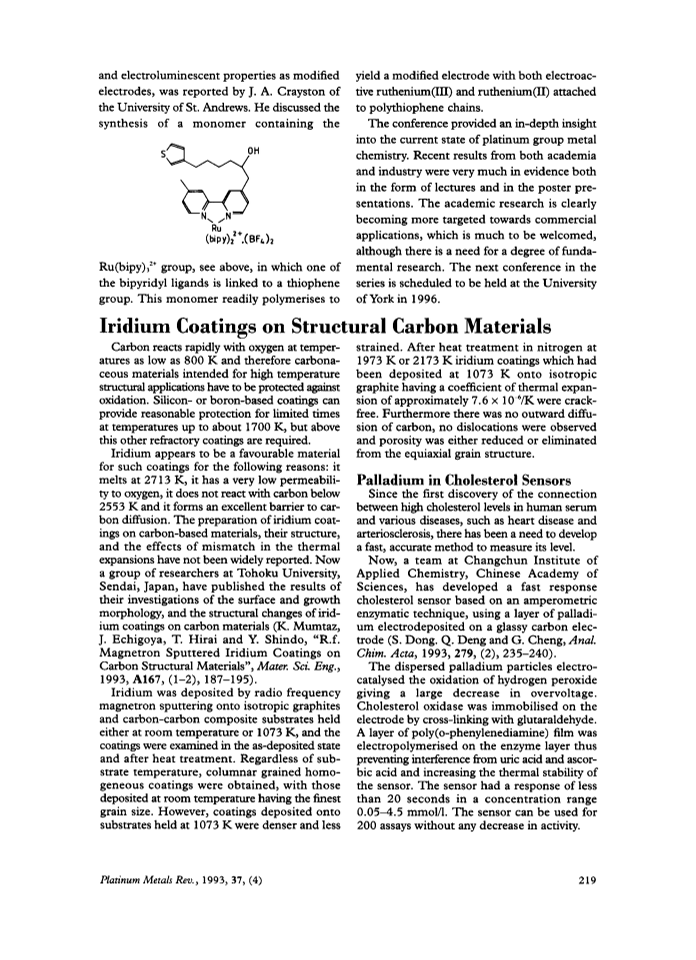
There is no abstract available.
© Johnson Matthey