-
oa Plastic Deformation and Fracture of Ruthenium Single Crystals
- Source: Platinum Metals Review, Volume 38, Issue 1, Jan 1994, p. 12 - 15
-
- 01 Jan 1994
Preview this article:
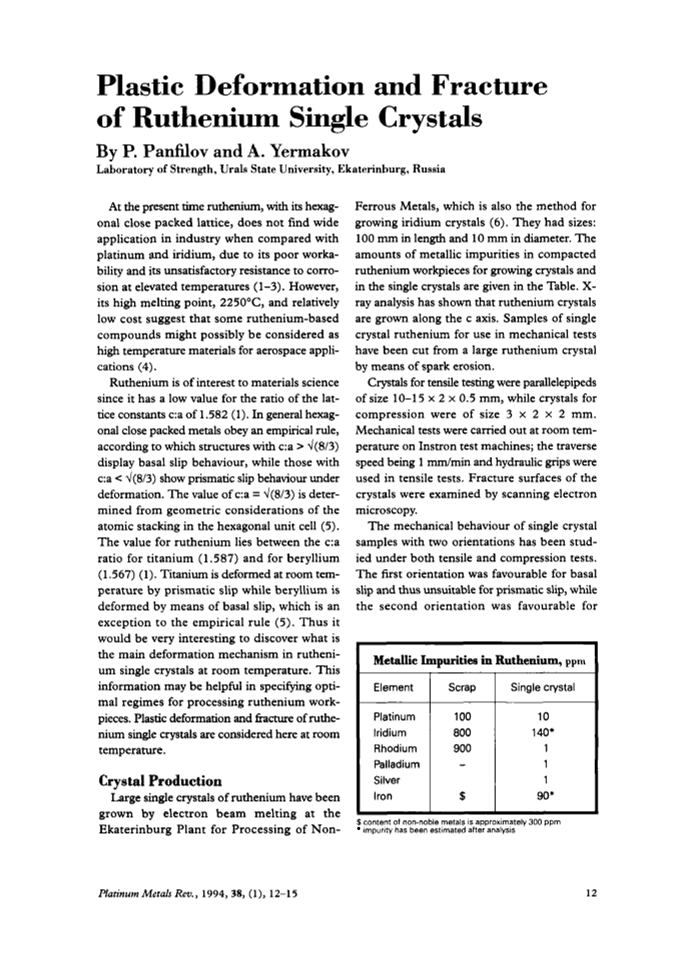



Plastic Deformation and Fracture of Ruthenium Single Crystals, Page 1 of 1
< Previous page Next page > /docserver/preview/fulltext/pmr/38/1/pmr0038-0012-1.gif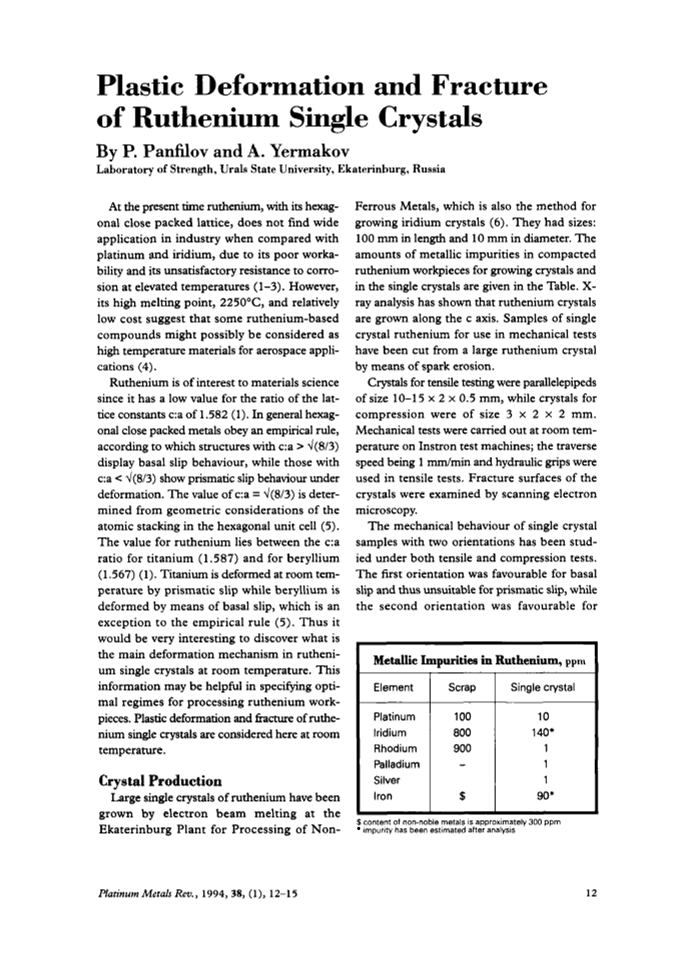
There is no abstract available.
© Johnson Matthey