-
oa Platinum Assists in Coal Flue Gas Desulphurisation
- Source: Platinum Metals Review, Volume 38, Issue 2, Apr 1994, p. 70 - 70
-
- 01 Jan 1994
Preview this article:
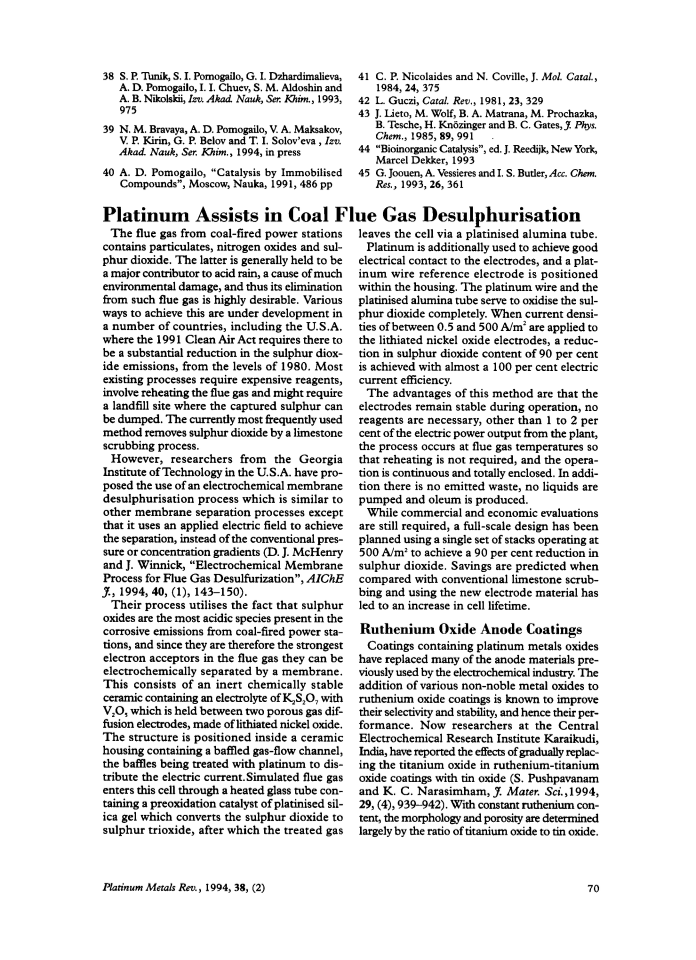



Platinum Assists in Coal Flue Gas Desulphurisation, Page 1 of 1
< Previous page Next page > /docserver/preview/fulltext/pmr/38/2/pmr0038-0070a-1.gif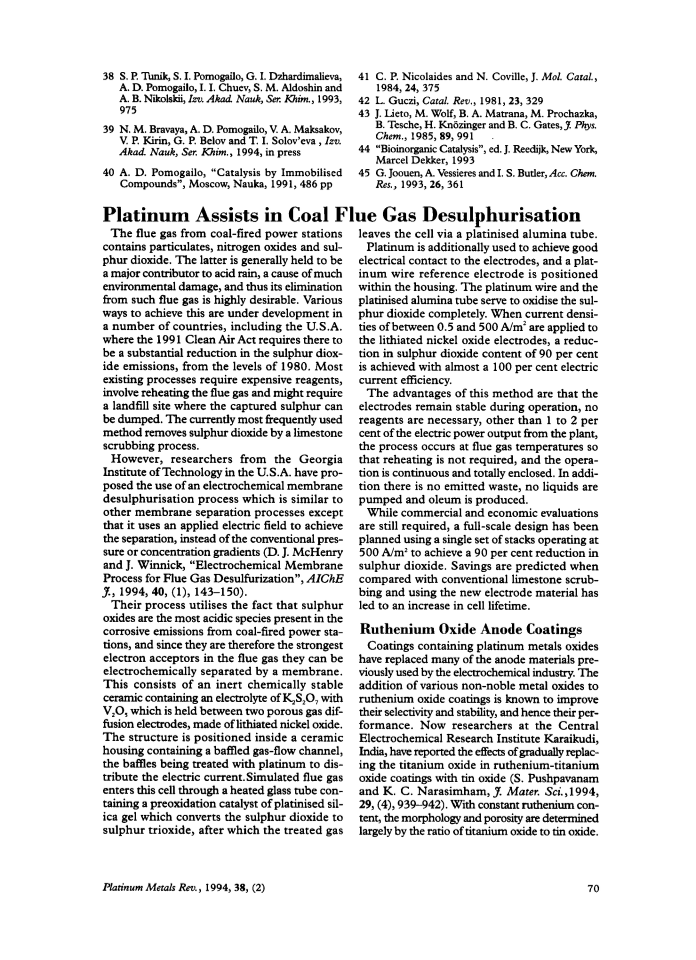
There is no abstract available.
© Johnson Matthey