-
oa Catalysts Aid Cleaner Environment
Thermal Incineration Process Enhanced by Platinum-Based Catalyst
- Source: Platinum Metals Review, Volume 38, Issue 4, Oct 1994, p. 160 - 163
-
- 01 Jan 1994
Preview this article:
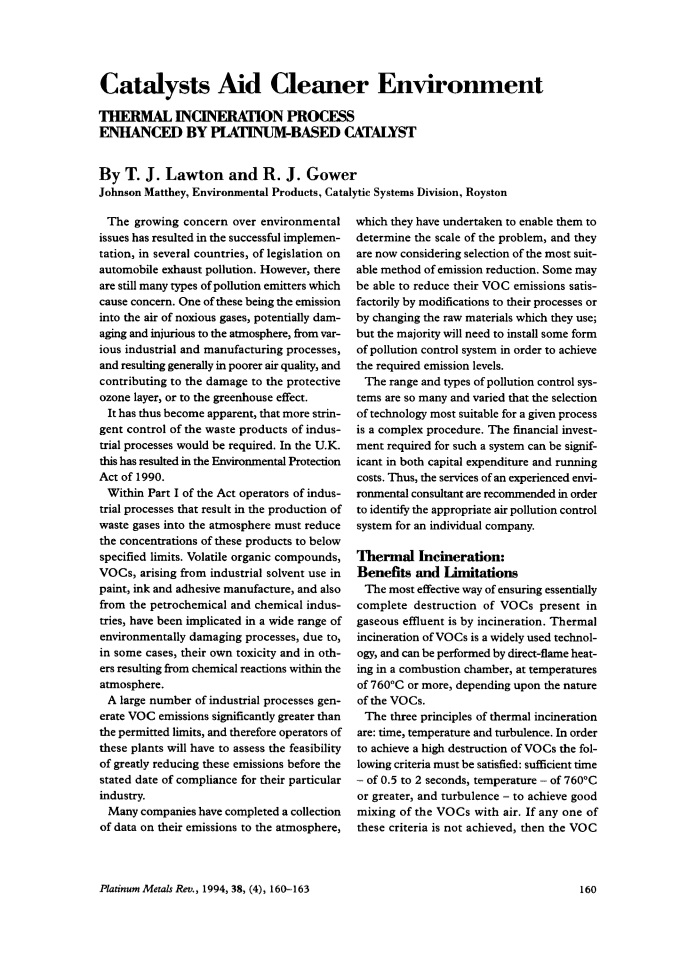



Catalysts Aid Cleaner Environment, Page 1 of 1
< Previous page Next page > /docserver/preview/fulltext/pmr/38/4/pmr0038-0160-1.gif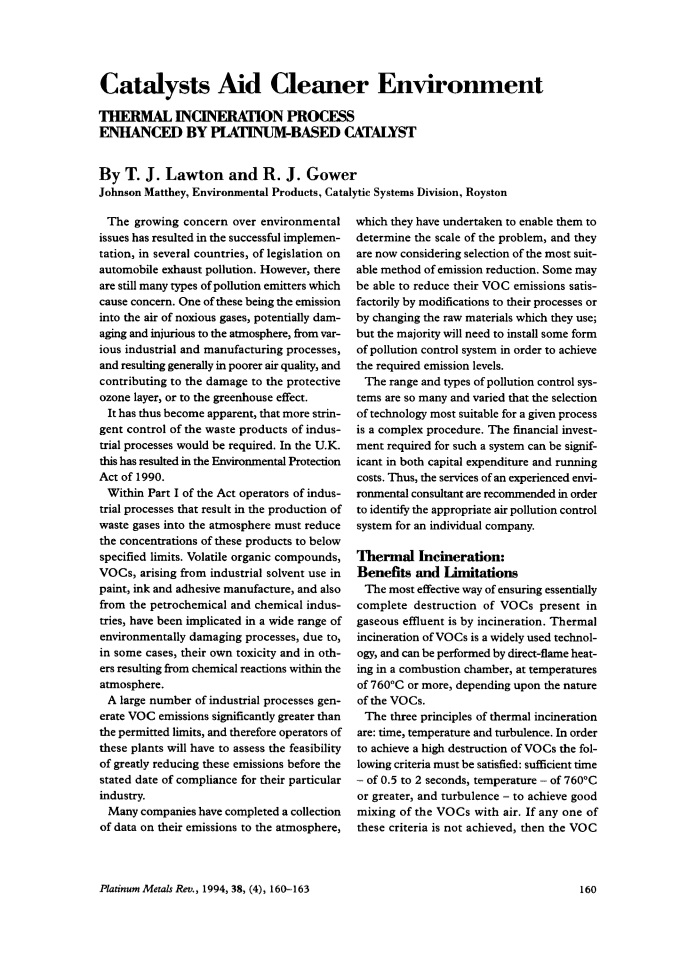
There is no abstract available.
© Johnson Matthey