-
oa European Precious Metals Conference
New Technology and Advances in Automotive Applications
- Source: Platinum Metals Review, Volume 39, Issue 3, Jul 1995, p. 112 - 116
-
- 01 Jan 1995
Preview this article:
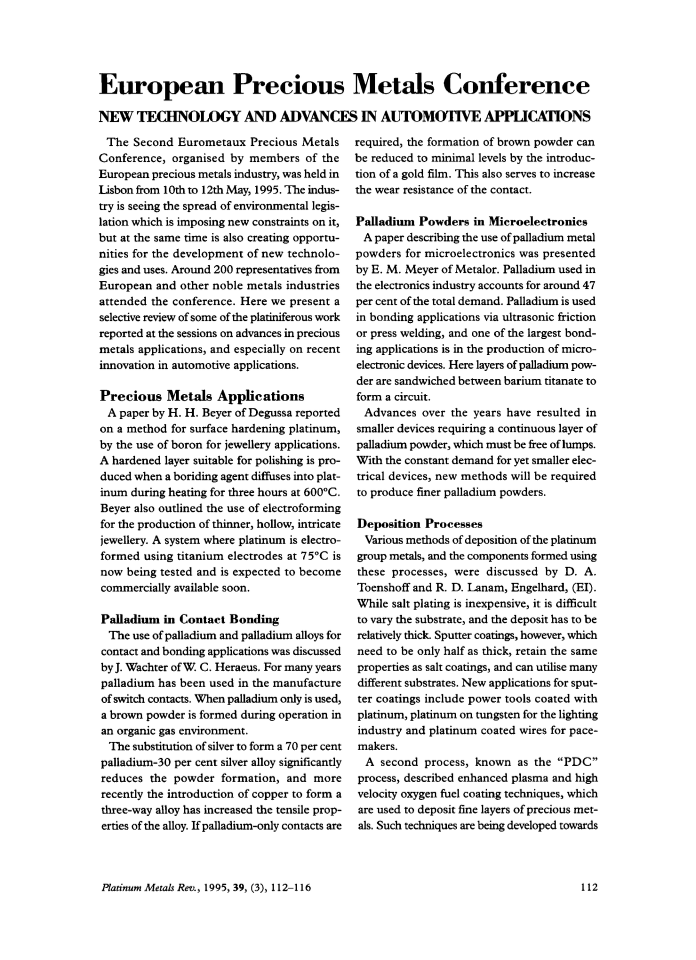



European Precious Metals Conference, Page 1 of 1
< Previous page Next page > /docserver/preview/fulltext/pmr/39/3/pmr0039-0112-1.gif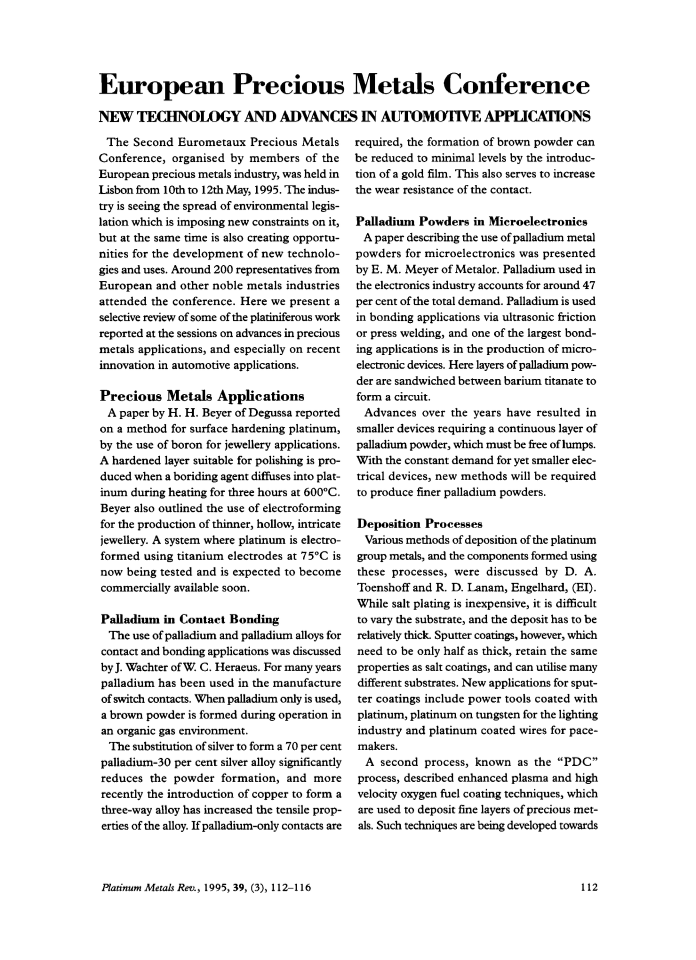
There is no abstract available.
© Johnson Matthey