-
oa Fourth Grove Fuel Cell Symposium
From Technical Success to the Challenges Facing Commercialisation
- Source: Platinum Metals Review, Volume 39, Issue 4, Oct 1995, p. 160 - 164
-
- 01 Jan 1995
Preview this article:
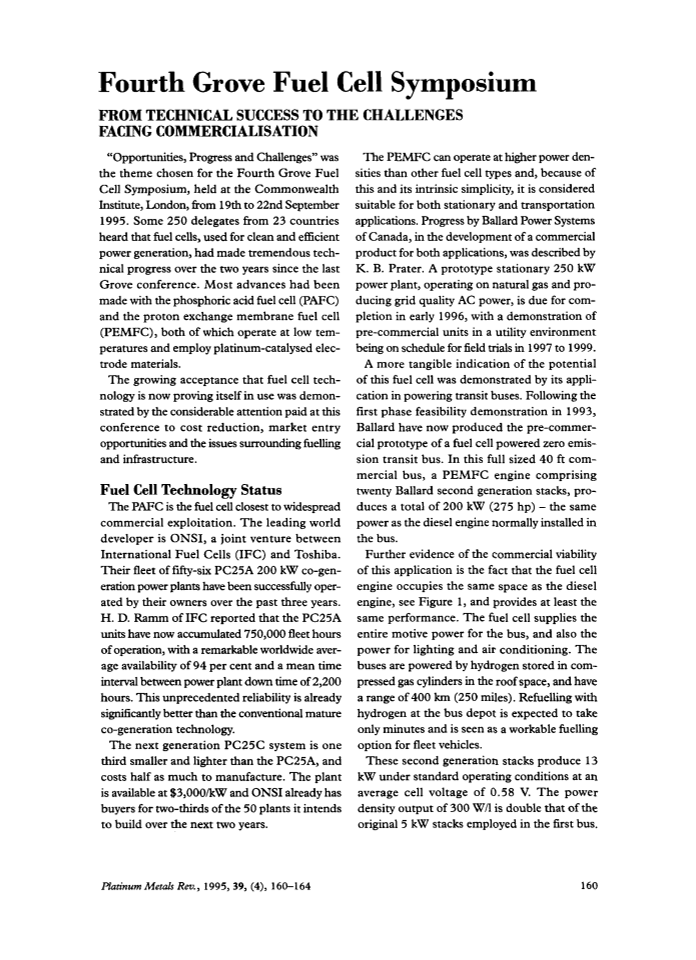



Fourth Grove Fuel Cell Symposium, Page 1 of 1
< Previous page Next page > /docserver/preview/fulltext/pmr/39/4/pmr0039-0160-1.gif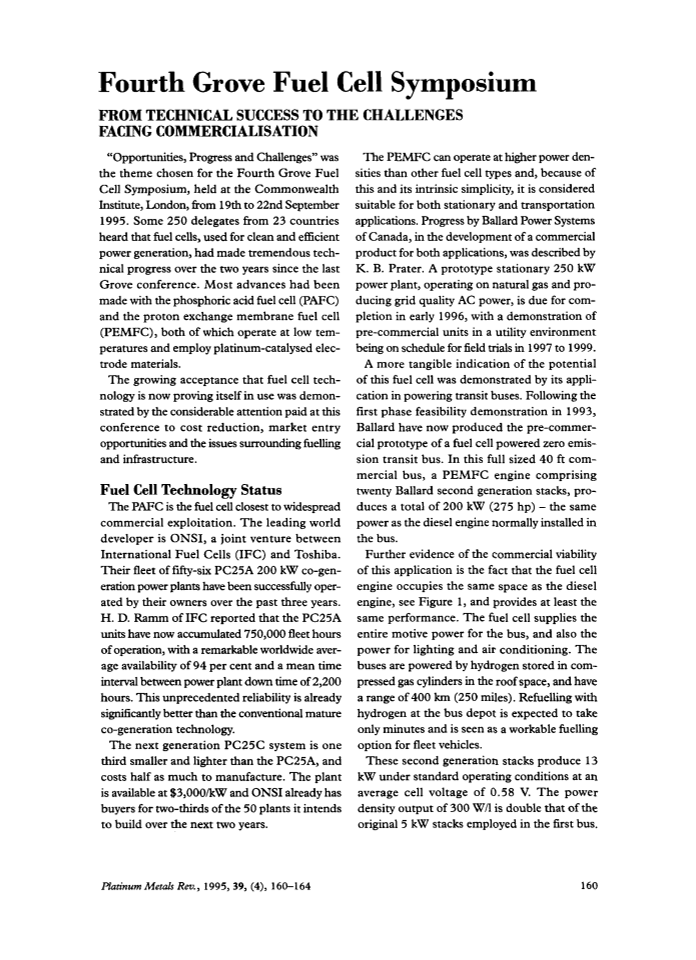
There is no abstract available.
© Johnson Matthey