-
oa New Materials for Fuel Cell Systems
A Report of the First International Symposium
- Source: Platinum Metals Review, Volume 39, Issue 4, Oct 1995, p. 165 - 166
-
- 01 Jan 1995
Preview this article:
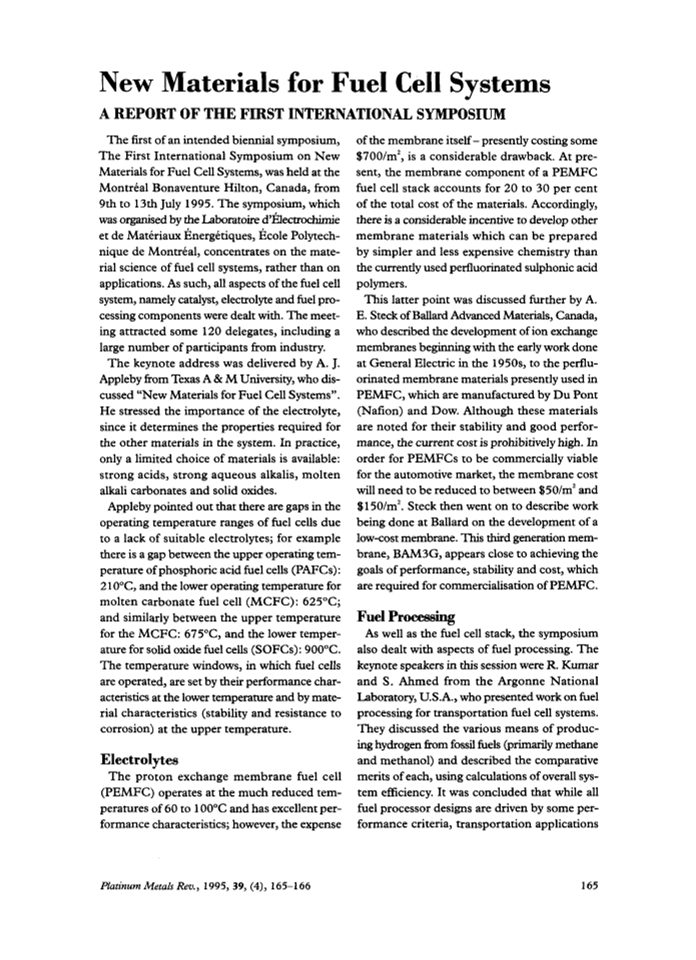



New Materials for Fuel Cell Systems, Page 1 of 1
< Previous page Next page > /docserver/preview/fulltext/pmr/39/4/pmr0039-0165-1.gif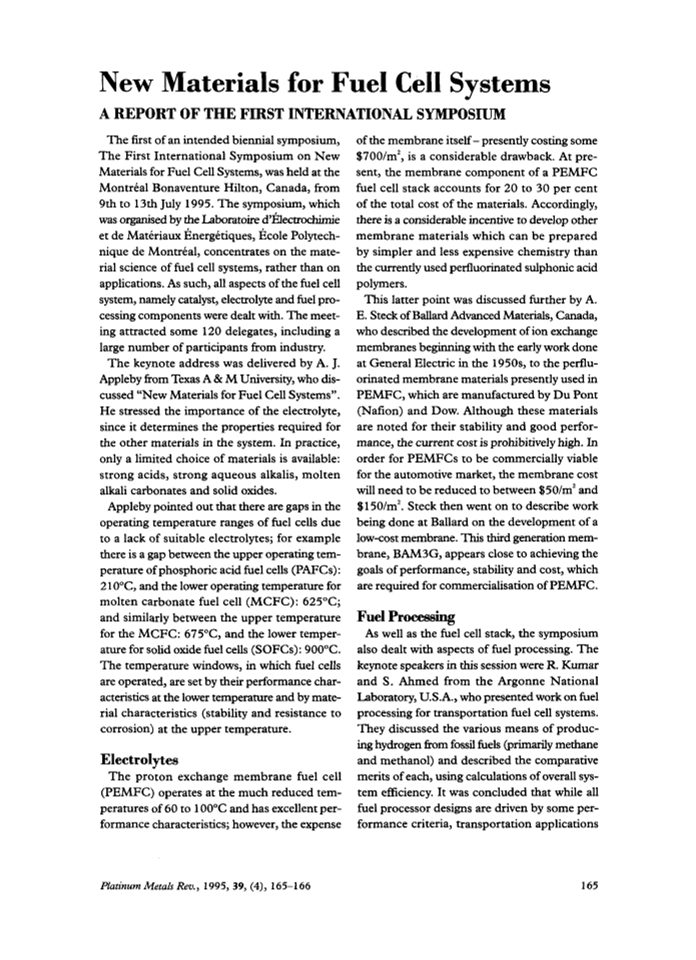
There is no abstract available.
© Johnson Matthey