-
oa The Use of Platinum in High Power Thermionic Valves
- Source: Platinum Metals Review, Volume 4, Issue 3, Jul 1960, p. 82 - 85
-
- 01 Jul 1960
Preview this article:
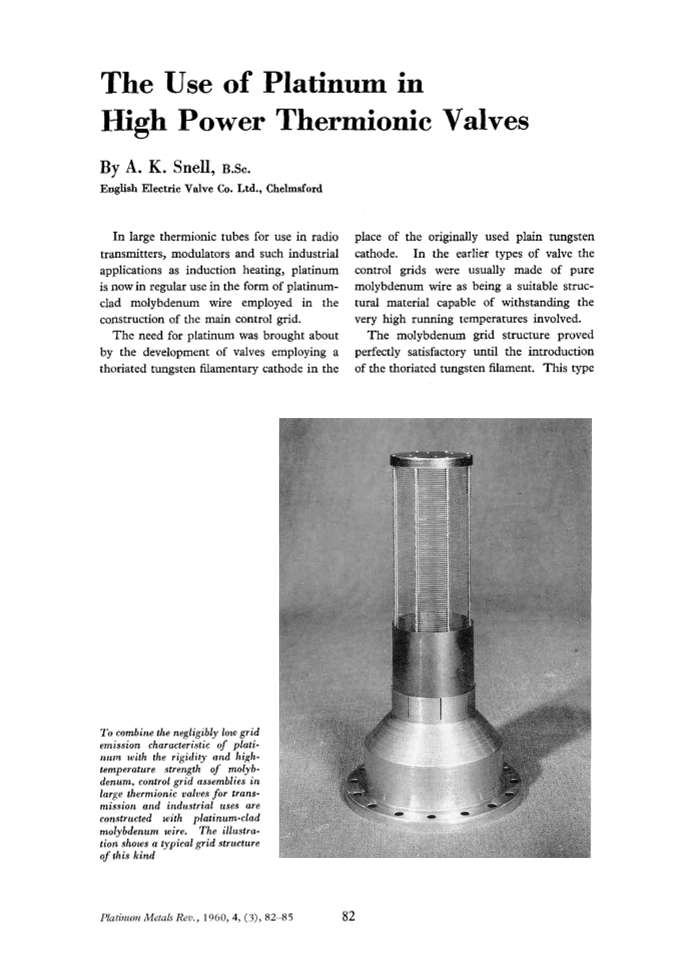



The Use of Platinum in High Power Thermionic Valves, Page 1 of 1
< Previous page Next page > /docserver/preview/fulltext/pmr/4/3/pmr0004-0082-1.gif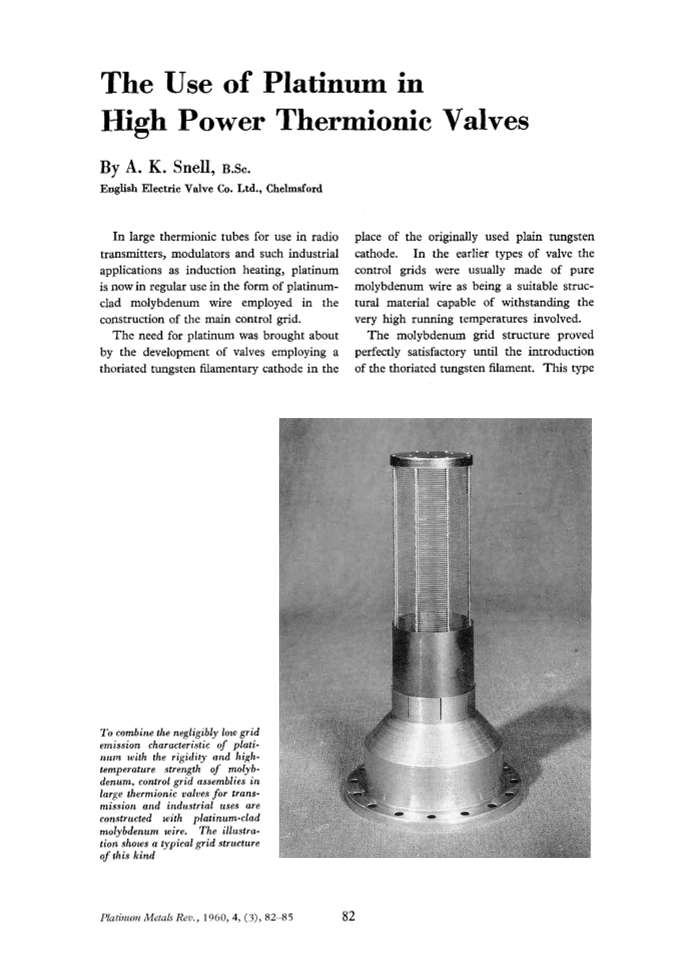
There is no abstract available.
© Johnson Matthey