-
oa Clean Fuel Cell Energy for Today
- Source: Platinum Metals Review, Volume 43, Issue 1, Jan 1999, p. 14 - 17
Preview this article:
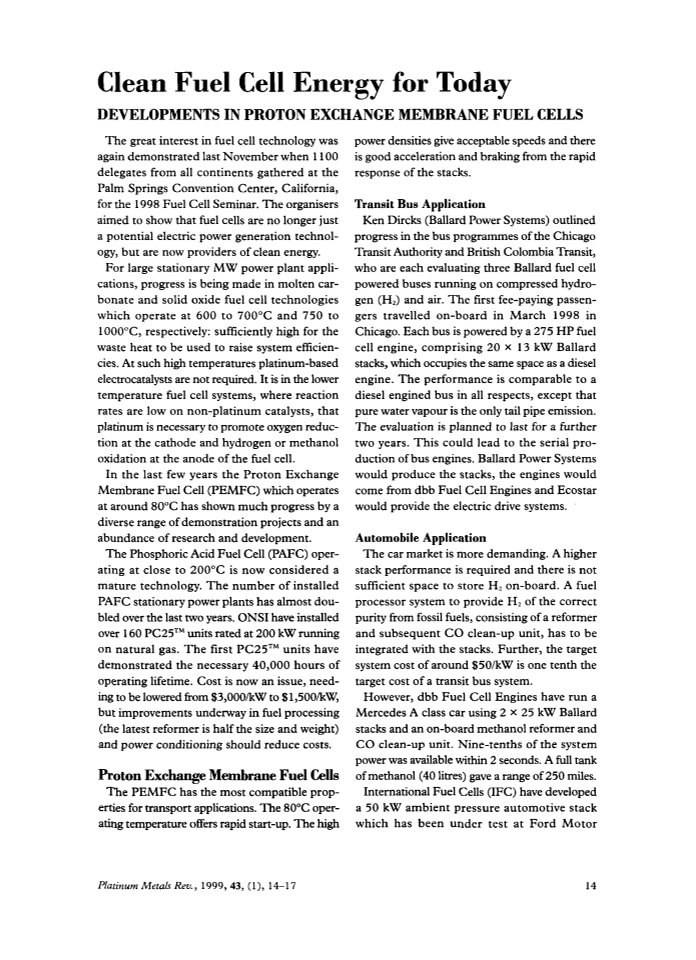



Clean Fuel Cell Energy for Today, Page 1 of 1
< Previous page Next page > /docserver/preview/fulltext/pmr/43/1/s5-1.gif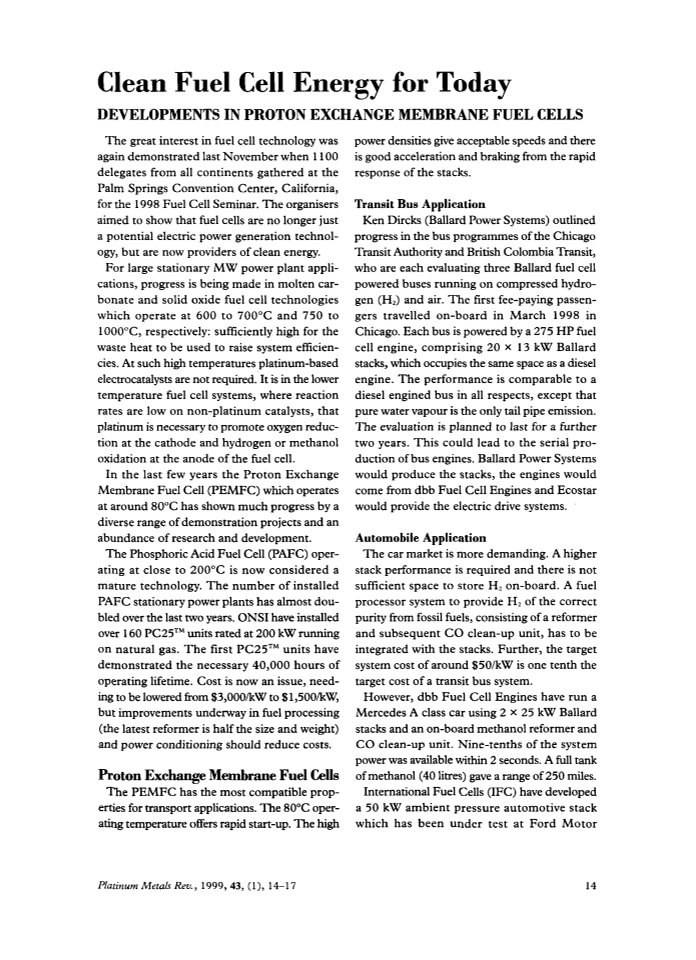
There is no abstract available.
© Johnson Matthey