-
oa Advanced Exhaust Emissions Control
A Selective Review of the Detroit 2000 SAE World Congress
- Source: Platinum Metals Review, Volume 44, Issue 2, Apr 2000, p. 67 - 71
-
- 01 Jan 2000
Preview this article:
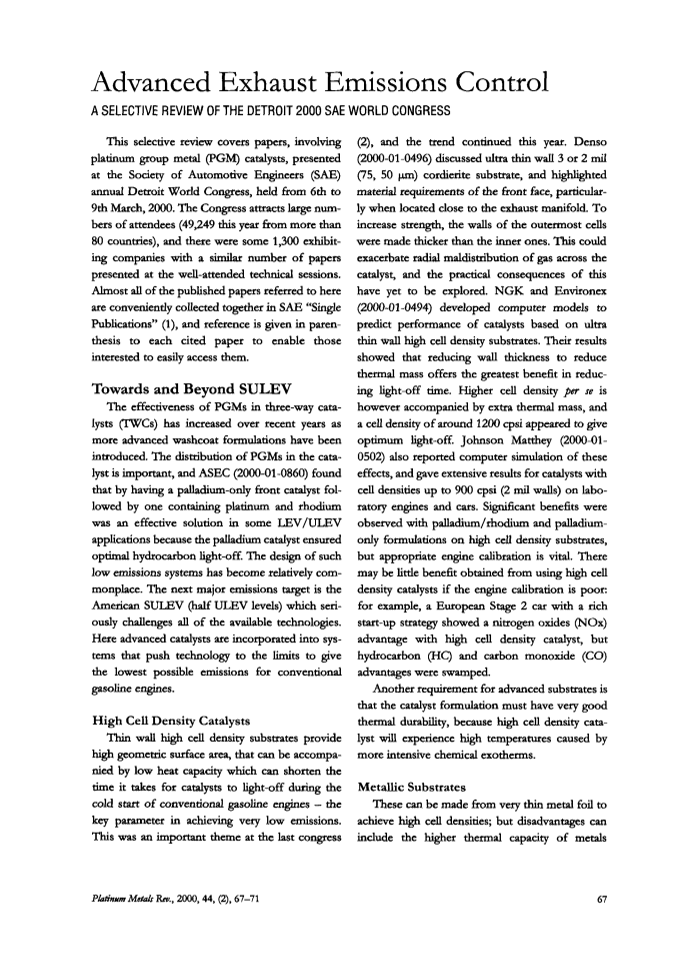



Advanced Exhaust Emissions Control, Page 1 of 1
< Previous page Next page > /docserver/preview/fulltext/pmr/44/2/pmr0044-0067-1.gif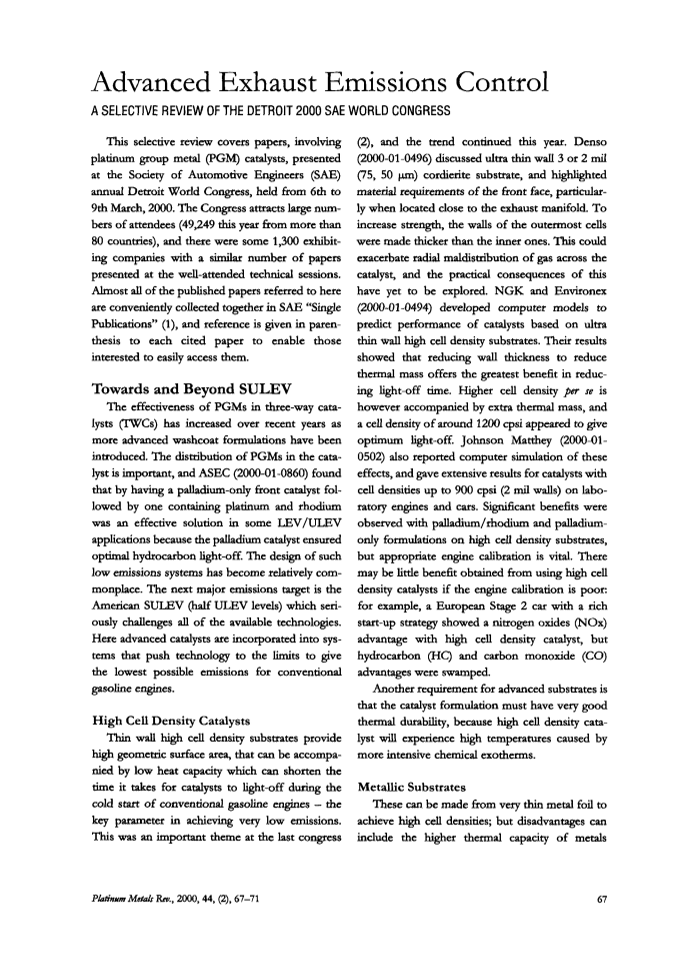
There is no abstract available.
© Johnson Matthey