-
oa Techniques for Catalyst Manufacture
Review of a Royal Society of Chemistry Meeting on Applied Catalysis
- Source: Platinum Metals Review, Volume 45, Issue 1, Jan 2001, p. 20 - 21
-
- 01 Jan 2001
Preview this article:
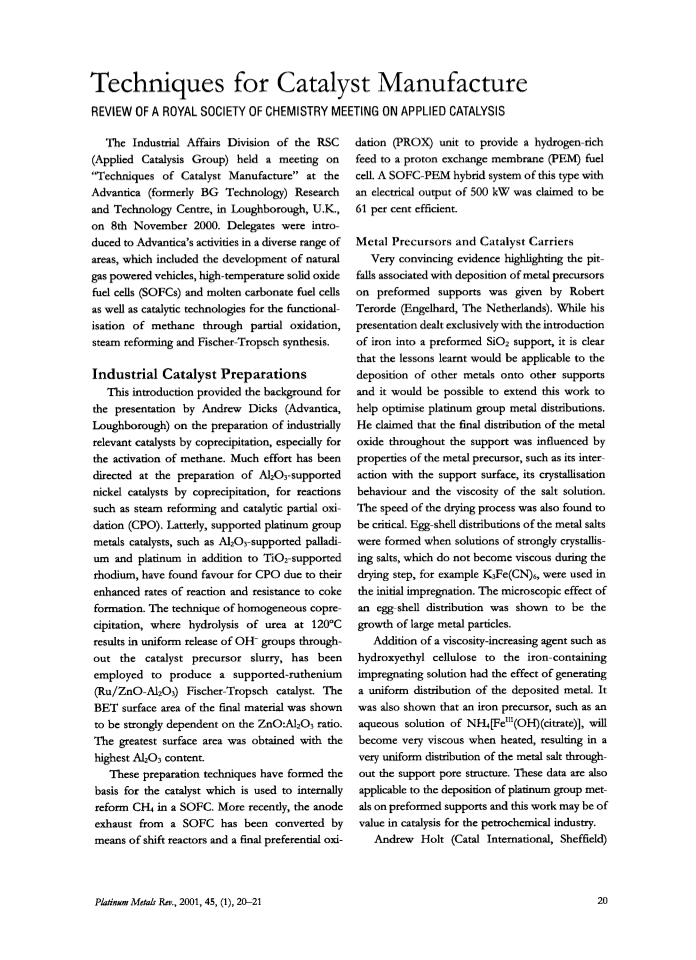



Techniques for Catalyst Manufacture, Page 1 of 1
< Previous page Next page > /docserver/preview/fulltext/pmr/45/1/pmr0045-0020-1.gif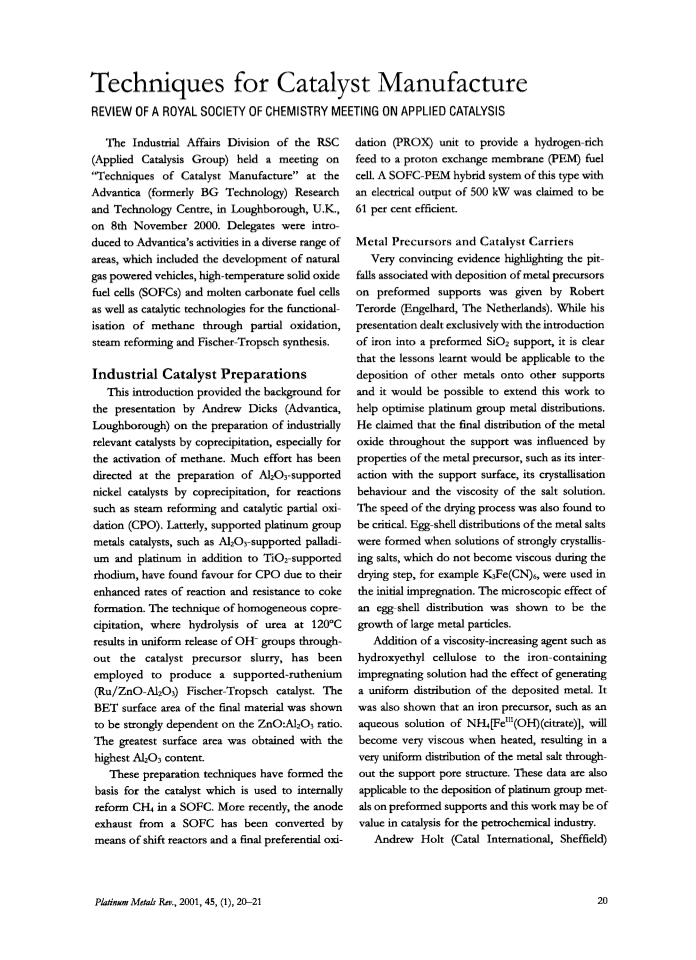
There is no abstract available.
© Johnson Matthey