-
oa Exhaust Emissions Control Developments
A Selective Review of the Detroit 2001 Sae World Congress
- Source: Platinum Metals Review, Volume 45, Issue 2, Apr 2001, p. 71 - 73
-
- 01 Jan 2001
Preview this article:
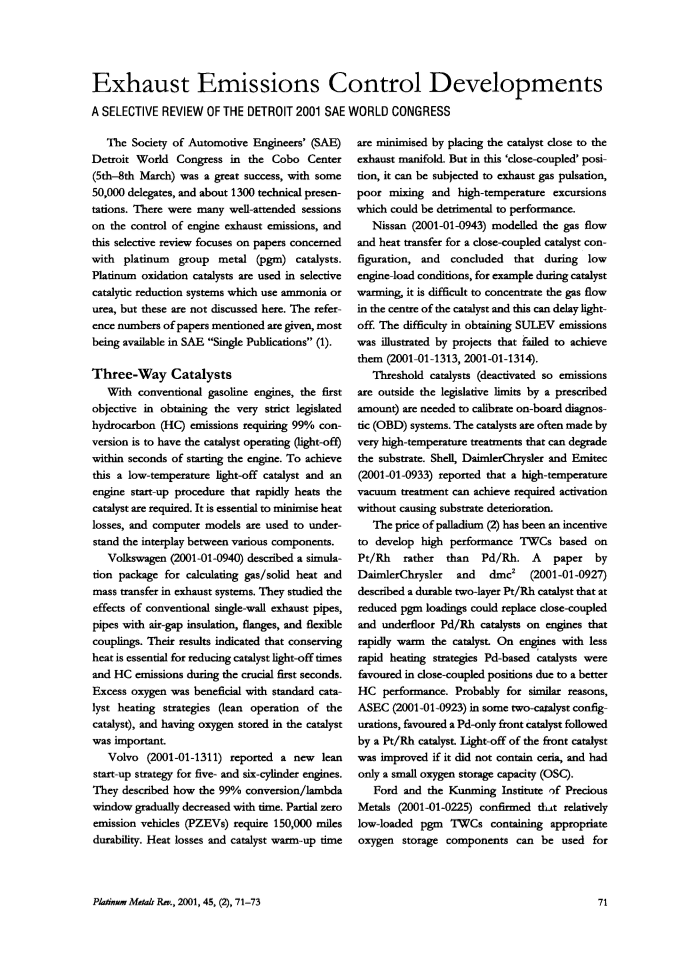



Exhaust Emissions Control Developments, Page 1 of 1
< Previous page Next page > /docserver/preview/fulltext/pmr/45/2/pmr0045-0071-1.gif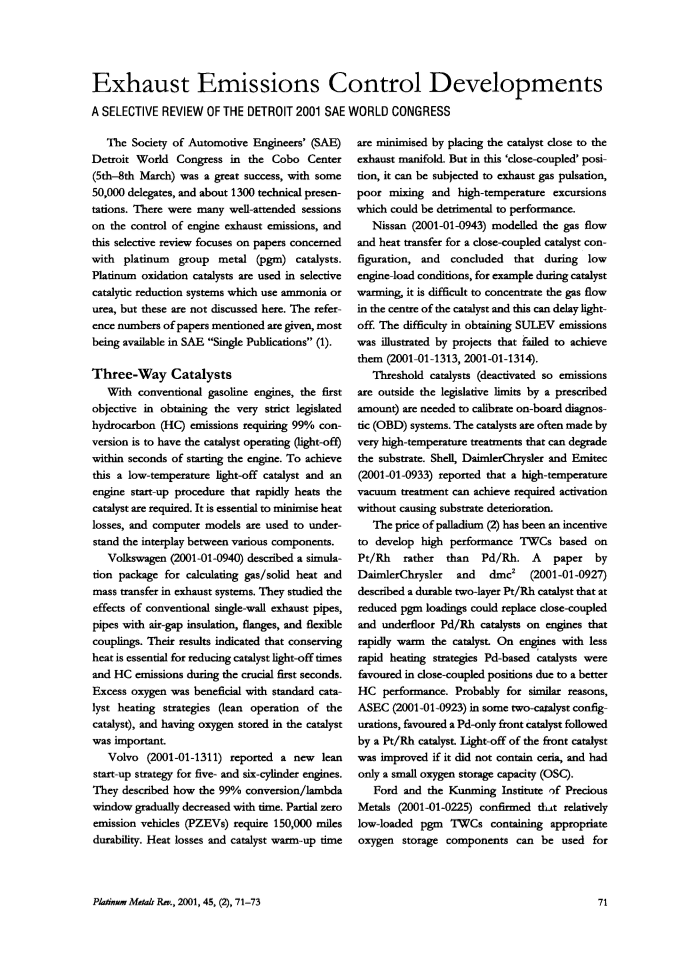
There is no abstract available.
© Johnson Matthey