-
oa Vehicle Emissions Control Technologies
- Source: Platinum Metals Review, Volume 47, Issue 1, Jan 2003, p. 15 - 19
-
- 01 Jan 2003
Preview this article:
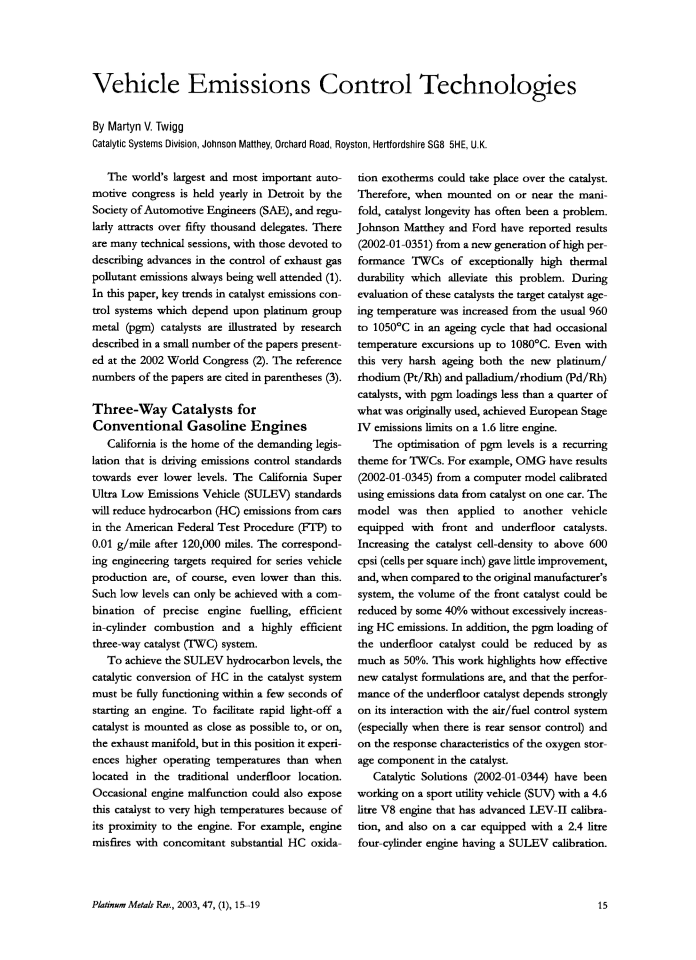



Vehicle Emissions Control Technologies, Page 1 of 1
< Previous page Next page > /docserver/preview/fulltext/pmr/47/1/pmr0047-0015-1.gif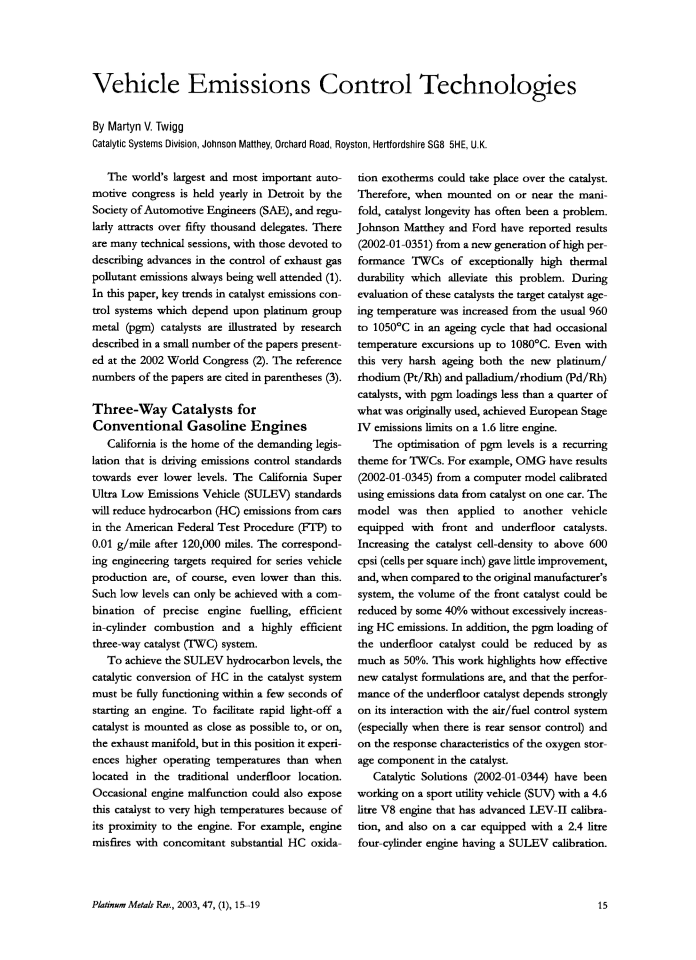
There is no abstract available.
© Johnson Matthey