-
oa Platinum Group Metals Technology in Ekaterinburg
- Source: Platinum Metals Review, Volume 47, Issue 1, Jan 2003, p. 36 - 36
-
- 01 Jan 2003
Preview this article:
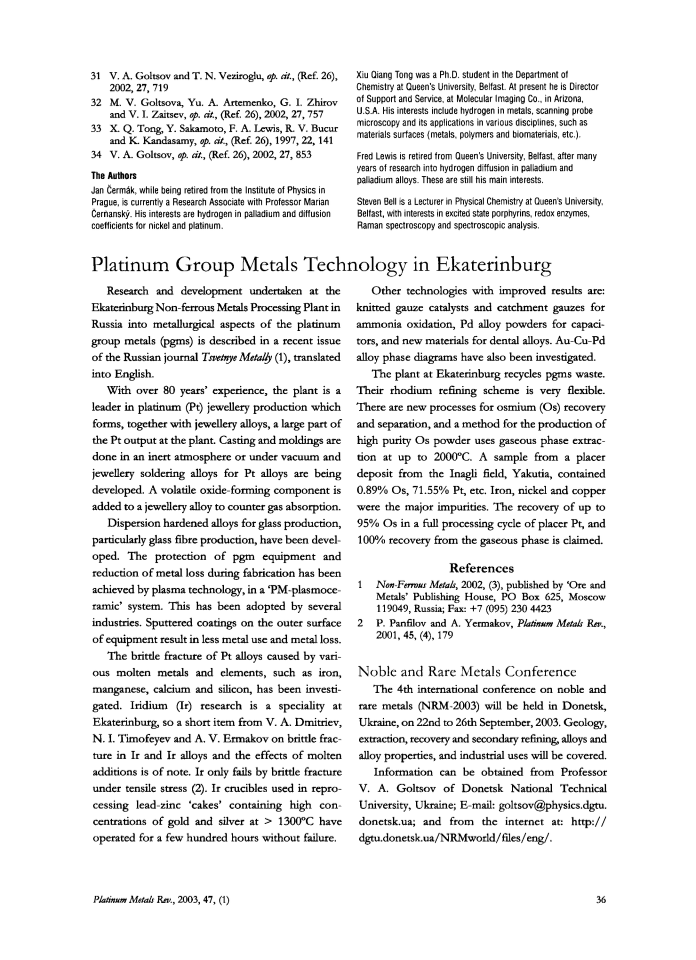



Platinum Group Metals Technology in Ekaterinburg, Page 1 of 1
< Previous page Next page > /docserver/preview/fulltext/pmr/47/1/pmr0047-0036a-1.gif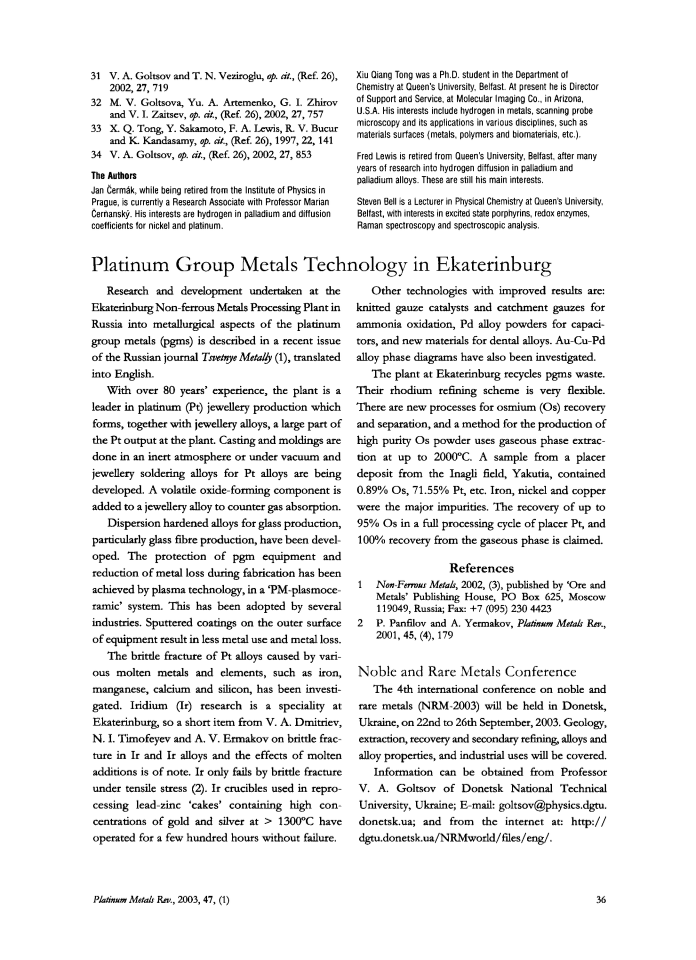
There is no abstract available.
© Johnson Matthey