-
oa The Eighth Grove Fuel Cell Symposium
Developing a Fuel Cell Manufacturing Industry
- Source: Platinum Metals Review, Volume 48, Issue 1, Jan 2004, p. 32 - 37
-
- 01 Jan 2004
Preview this article:
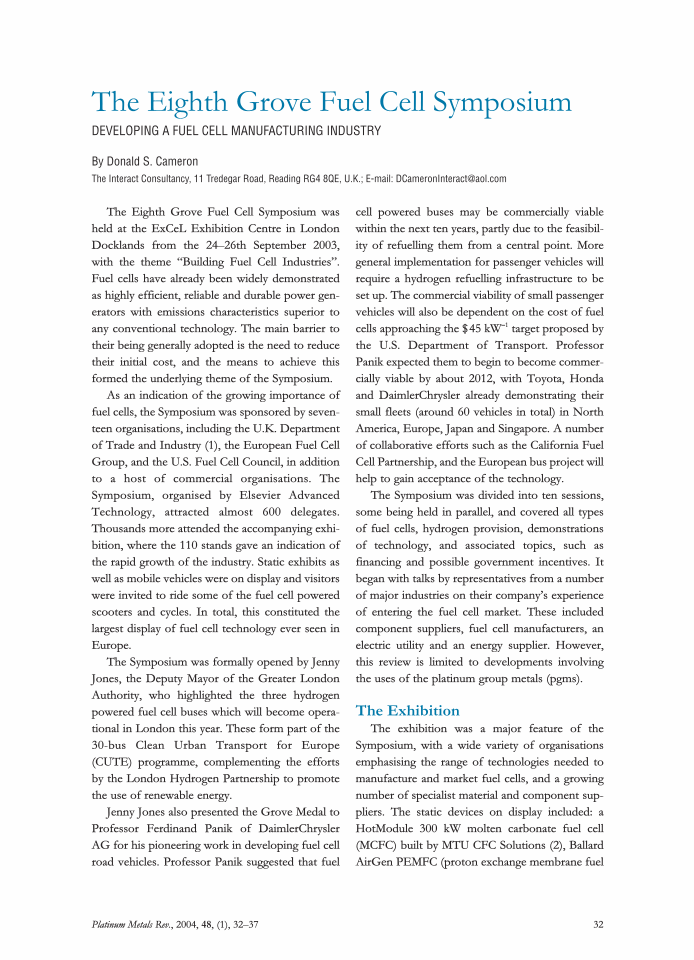



The Eighth Grove Fuel Cell Symposium, Page 1 of 1
< Previous page Next page > /docserver/preview/fulltext/pmr/48/1/pmr0048-0032-1.gif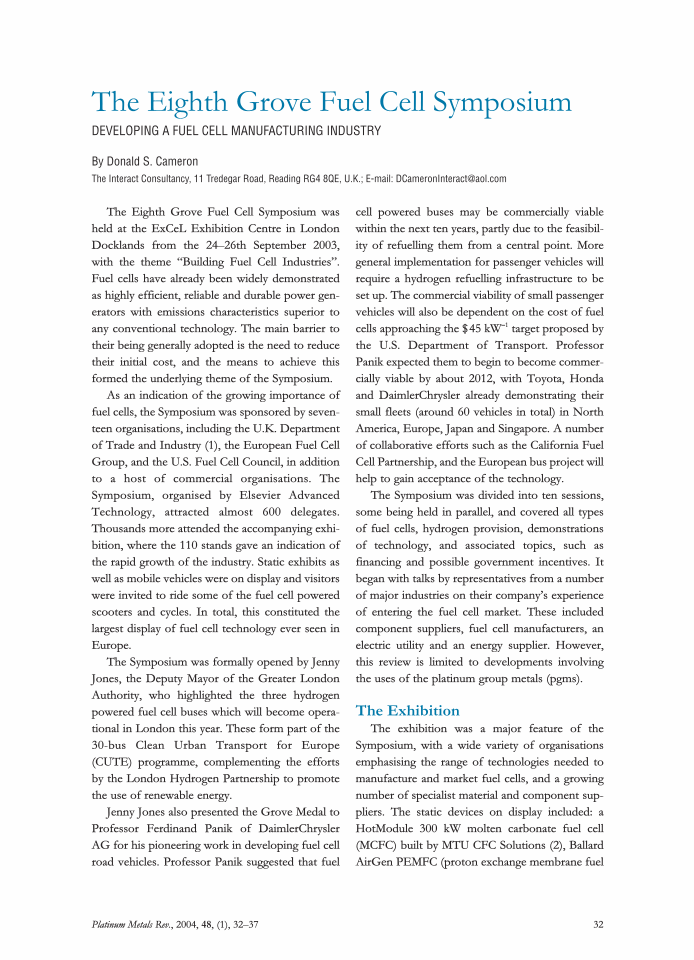
There is no abstract available.
© Johnson Matthey