-
oa Iridium Oxide Sensors for Industrial Lubricants
- Source: Platinum Metals Review, Volume 48, Issue 2, Apr 2004, p. 58 - 58
-
- 01 Jan 2004
Preview this article:
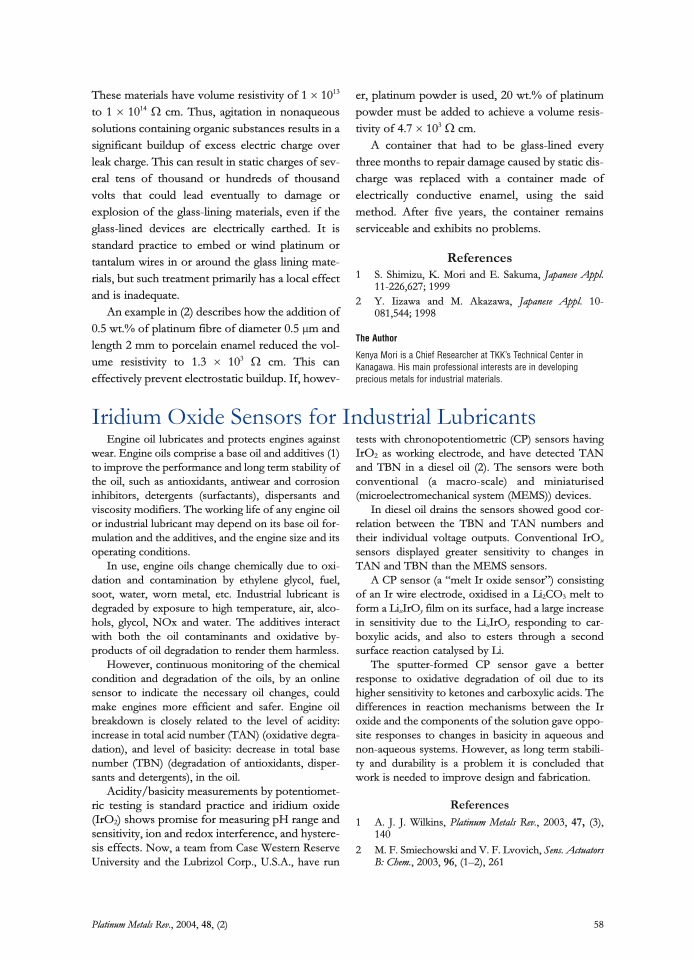



Iridium Oxide Sensors for Industrial Lubricants, Page 1 of 1
< Previous page Next page > /docserver/preview/fulltext/pmr/48/2/pmr0048-0058-1.gif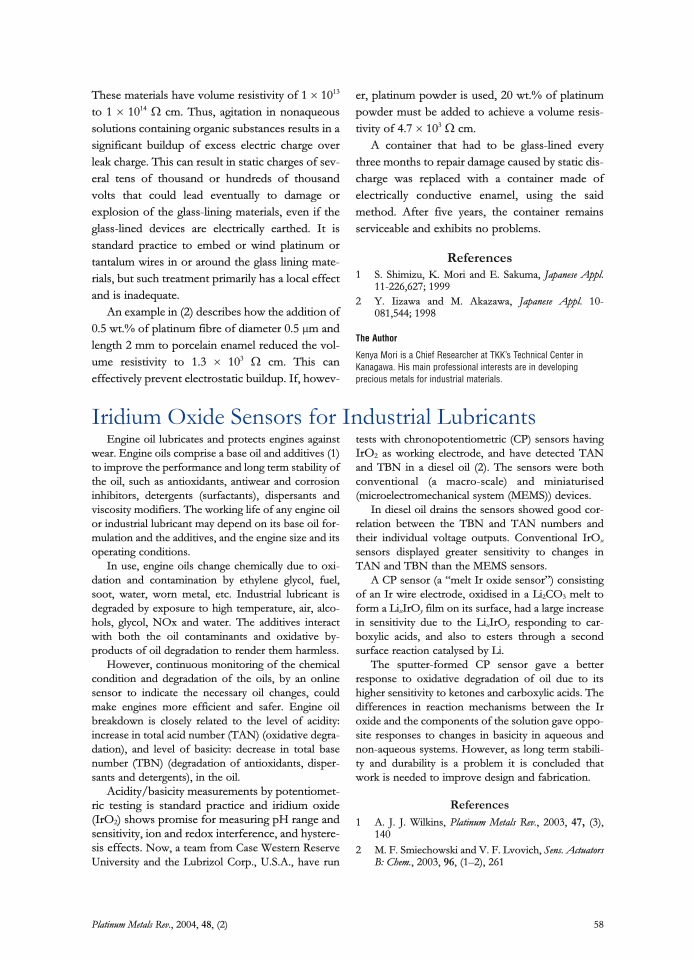
There is no abstract available.
© Johnson Matthey