-
oa Safeguarding Thermocouple Performance
- Source: Platinum Metals Review, Volume 48, Issue 2, Apr 2004, p. 88 - 88
-
- 01 Jan 2004
Preview this article:
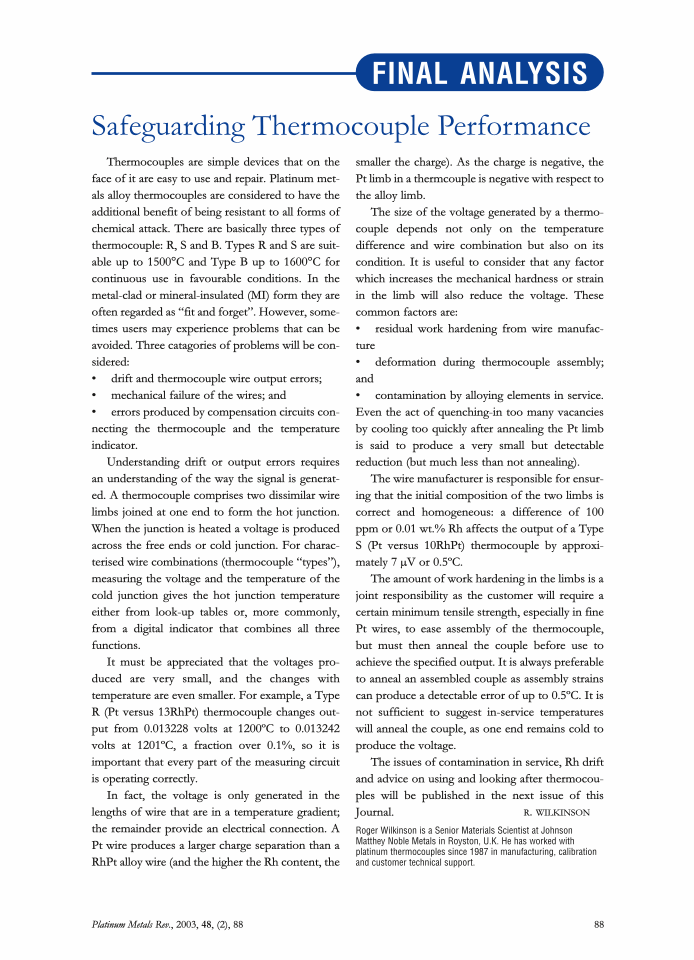



Safeguarding Thermocouple Performance, Page 1 of 1
< Previous page Next page > /docserver/preview/fulltext/pmr/48/2/pmr0048-0088-1.gif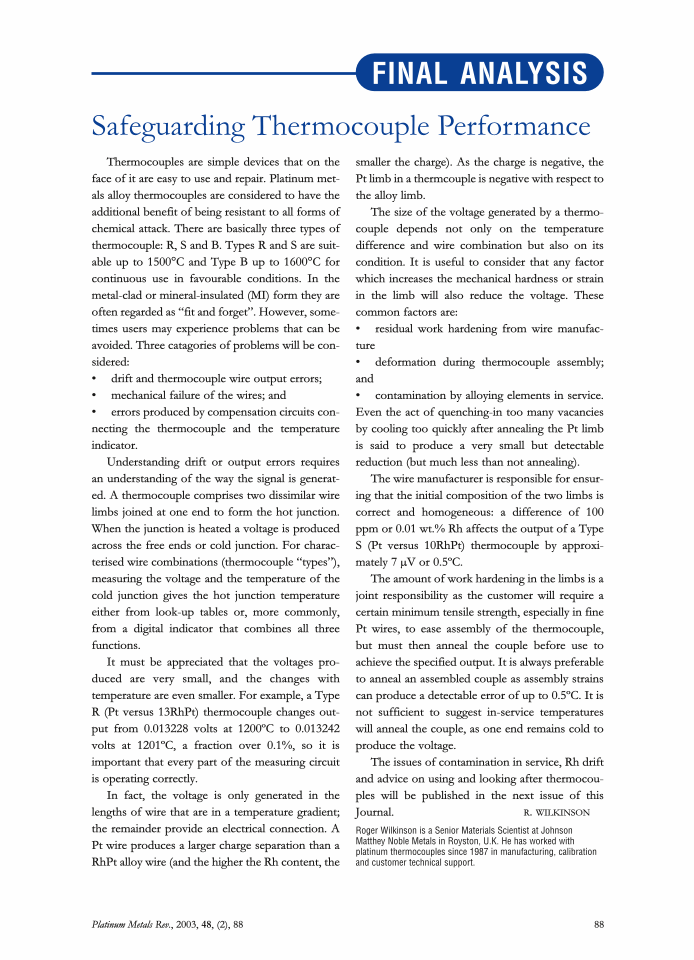
There is no abstract available.
© Johnson Matthey