-
oa Thermocouples – Minimising Drift
- Source: Platinum Metals Review, Volume 48, Issue 3, Jul 2004, p. 145 - 145
-
- 01 Jan 2004
Preview this article:
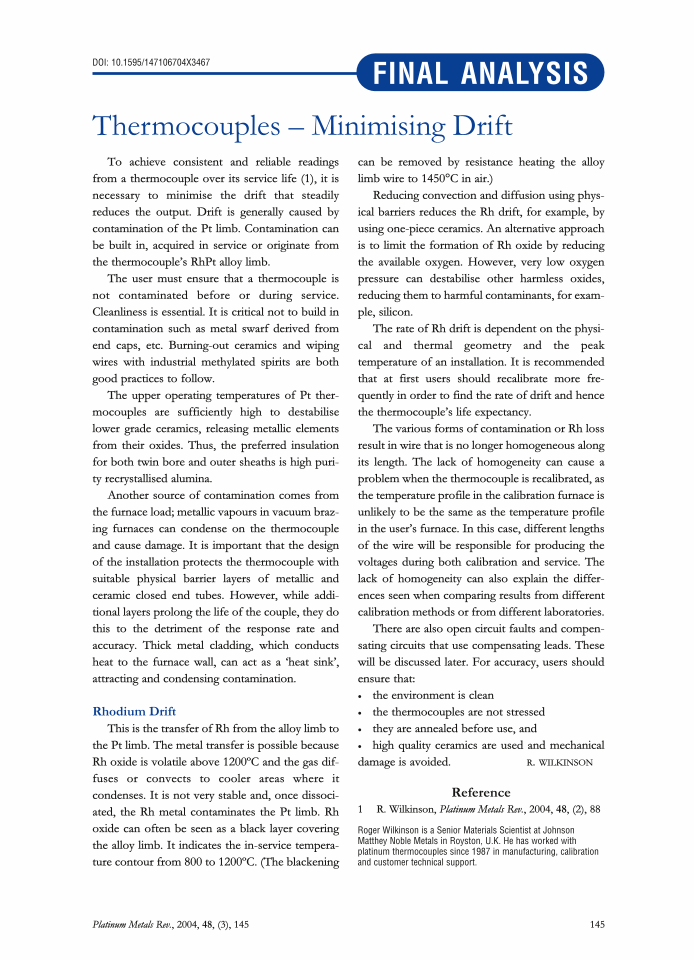



Thermocouples – Minimising Drift, Page 1 of 1
< Previous page Next page > /docserver/preview/fulltext/pmr/48/3/pmr0048-0145-1.gif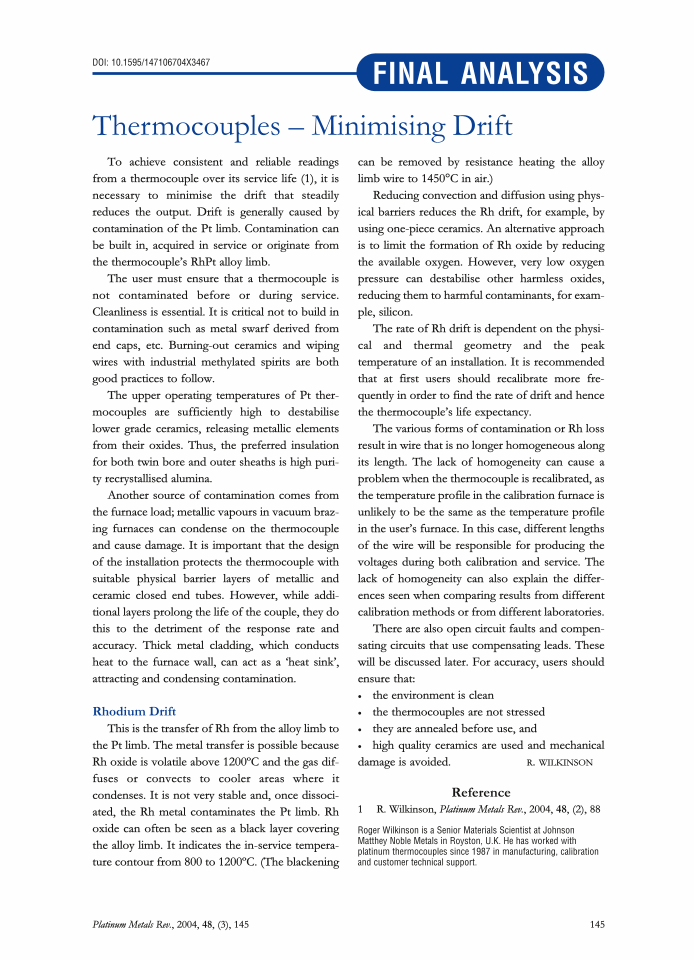
There is no abstract available.
© Johnson Matthey