-
oa Fuel Cells Science and Technology 2006
SCIENTIFIC ADVANCES IN FUEL CELL SYSTEMS
- Source: Platinum Metals Review, Volume 51, Issue 1, Jan 2007, p. 27 - 33
-
- 01 Jan 2007
Preview this article:
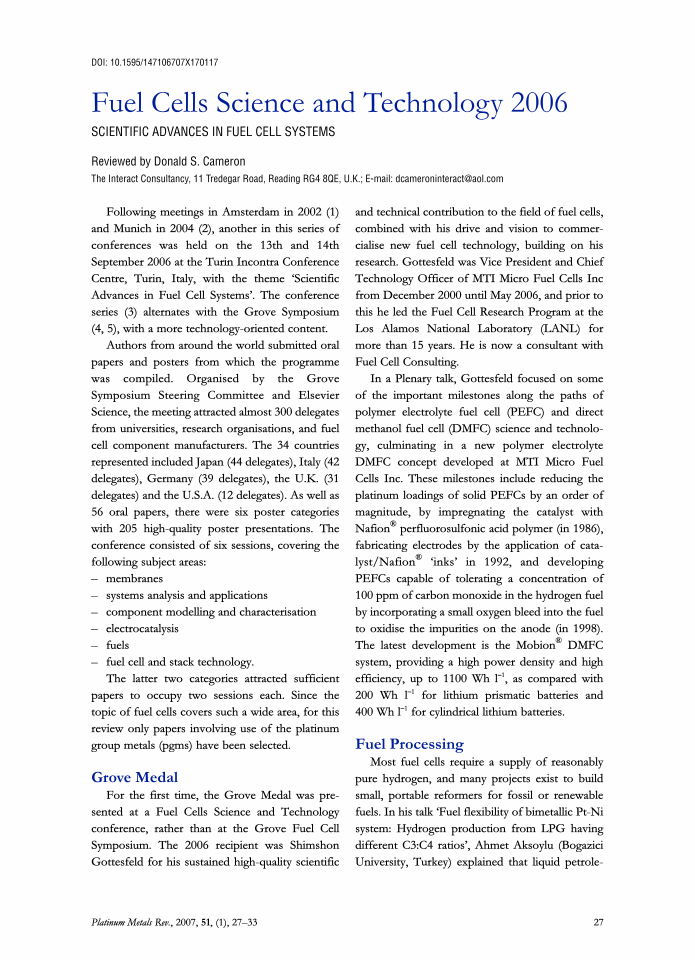



Fuel Cells Science and Technology 2006, Page 1 of 1
< Previous page Next page > /docserver/preview/fulltext/pmr/51/1/PMR-51-1-Cameron-1.gif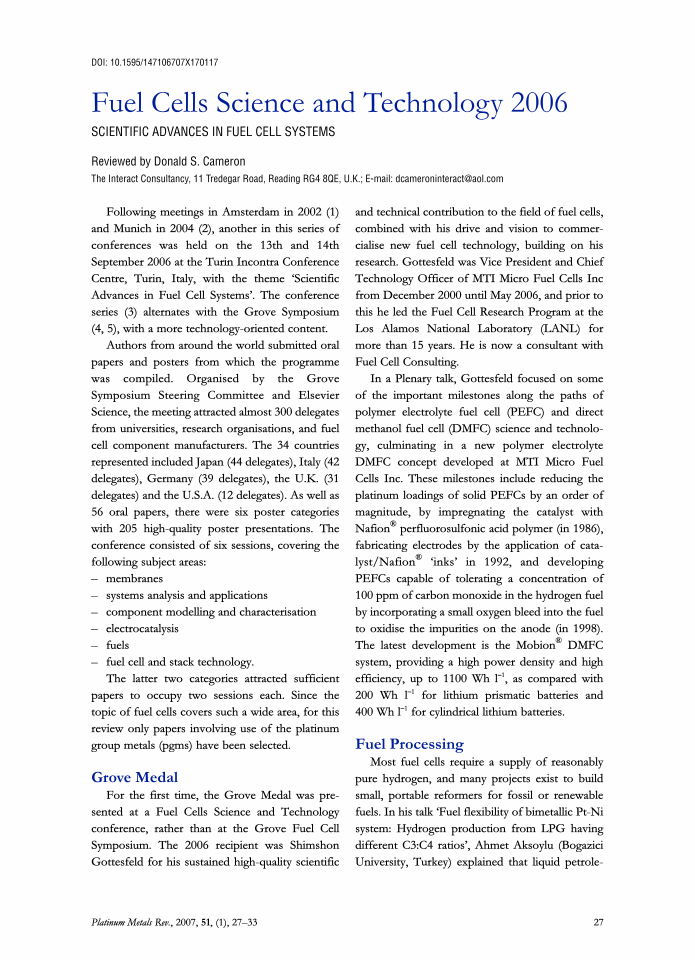
There is no abstract available.
© Johnson Matthey