-
oa Successful Scale-Up of Catalytic Processes
PALLADIUM IN INDUSTRIAL CATALYSIS
- Source: Platinum Metals Review, Volume 51, Issue 2, Apr 2007, p. 83 - 84
-
- 01 Jan 2007
Preview this article:
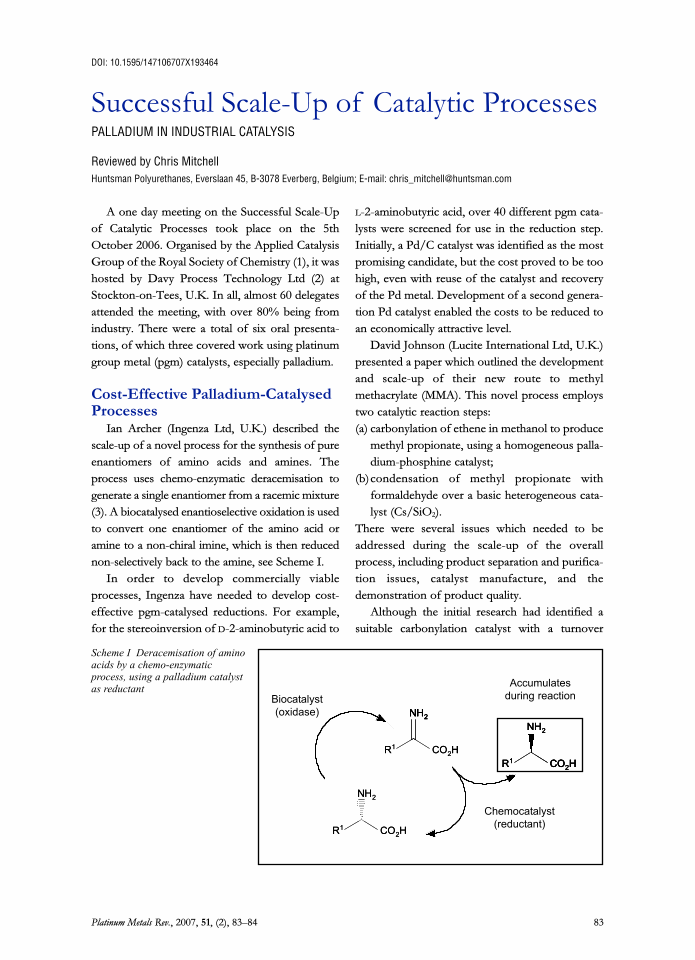



Successful Scale-Up of Catalytic Processes, Page 1 of 1
< Previous page Next page > /docserver/preview/fulltext/pmr/51/2/PMR-51-2-Mitchell-1.gif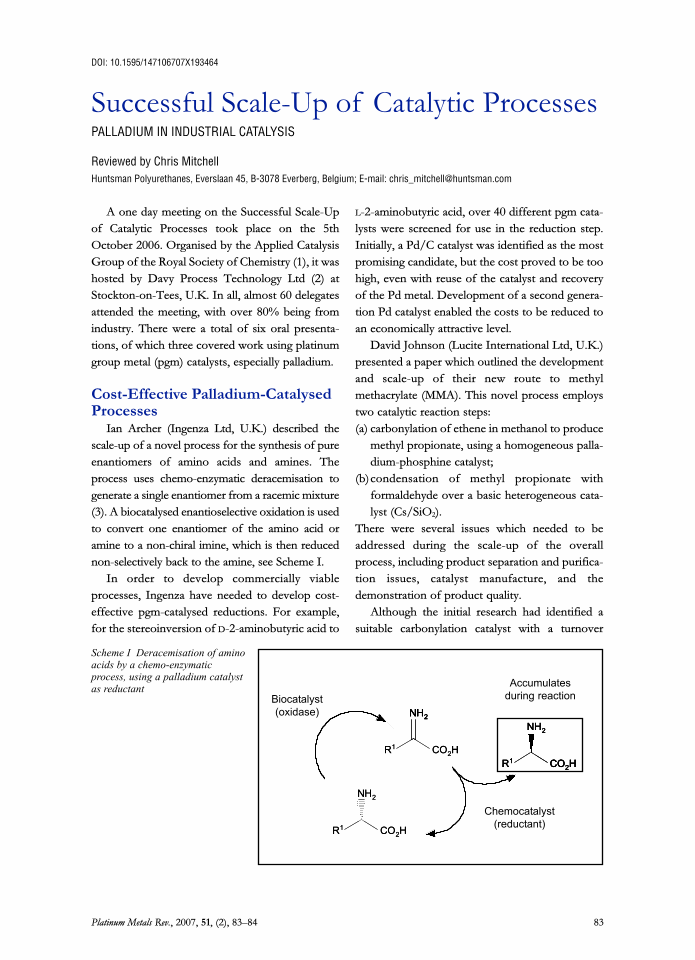
There is no abstract available.
© Johnson Matthey